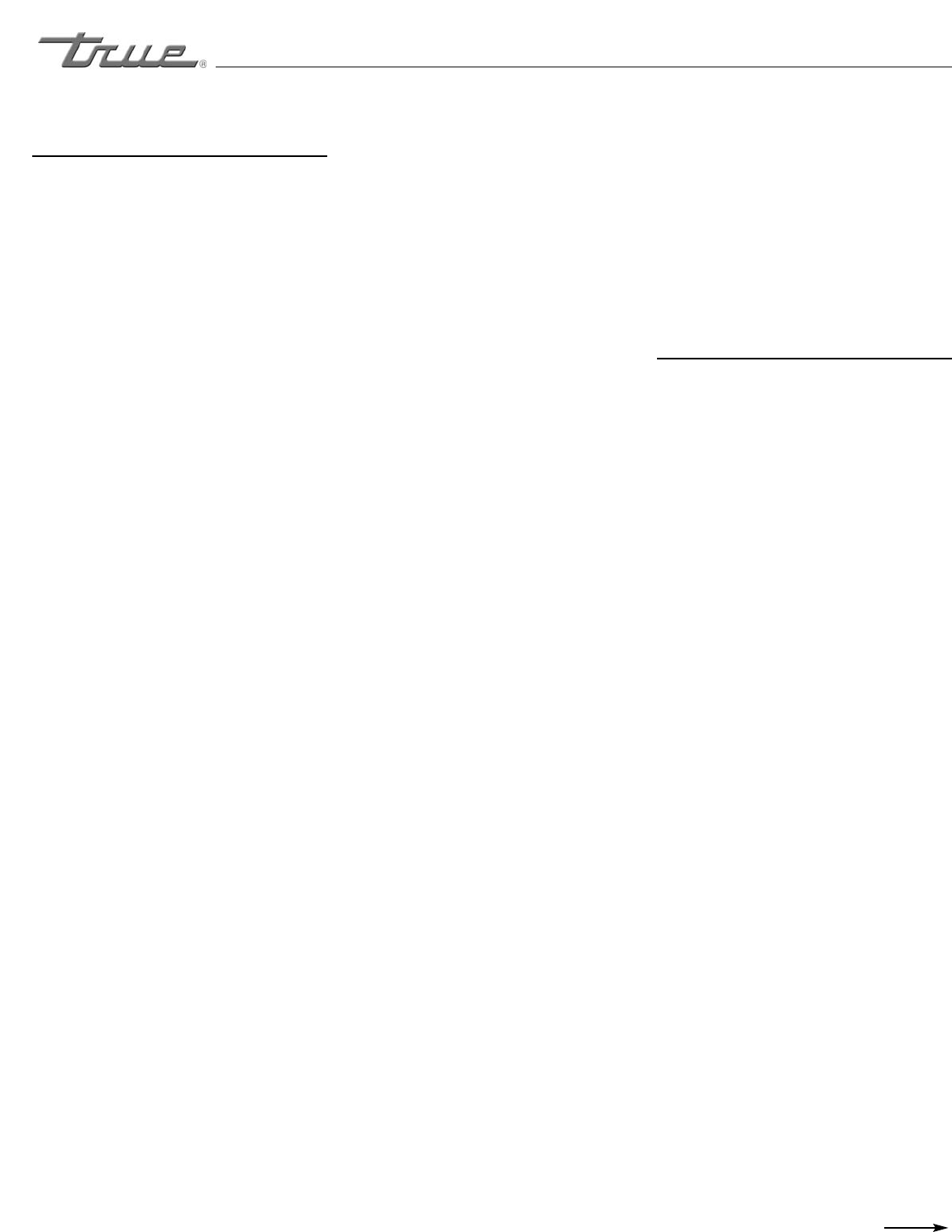
............ www.truemfg.com ............
............ www.truemfg.com ............
True Food Service Equipment, Inc.
True Food Service Equipment, Inc.
12
12
12
12
IF THE COMPRESSOR WILL
NOT RUN
1. If there is no voltage at the
compressor terminals, follow the wiring
diagram and check back from
compressor to the power supply to find
where the circuit is interrupted.
2. If power is available at the
compressor terminals, and the
compressor does not run, check the
voltage at the compressor terminals
while attempting to start the
compressor.
If voltage at the compressor terminals
is below 90% of the nameplate voltage,
it is possible the motor may not
develop sufficient torque to start.
Check to determine if wire sizes are
adequate, electrical connections are
loose, the circuit is overloaded, or if the
power supply is inadequate.
3. On single phase compressors, a
defective capacitor or relay may
prevent the compressor starting. If the
compressor attempts to start but is
unable to do so, or if there is a
humming sound, check the relay to see
if the relay contacts are damaged or
fused. The relay points should be
closed during the initial starting cycle,
but should open as the compressor
comes up to speed.
Remove the wires from the starting
relay and capacitors. Use a high
voltage ohmmeter to check for
continuity throughout the relay coil.
Replace the relay if there is not
continuity. Use an ohmmeter to check
across the relay contacts. Potential
relay contacts are normally closed
when the relay is not energized, current
relay contacts are normally open. If
either gives an incorrect reading,
replace the relay.
Any capacitor found to be bulging,
leaking, or damaged should be
replaced.
Make sure capacitors are discharged
before checking. Check for continuity
between each capacitor terminal and
the case. Continuity indicates a short,
and the capacitor should be replaced.
Substitute a “known to be good” start
capacitor if available. If compressor
then starts and runs properly, replace
the original start capacitor.
If a capacitor tester is not available, an
ohmmeter may be used to check run
and start capacitors for shorts or open
circuits. Use an ohmmeter set to its
highest resistance scale, and connect
prods to capacitor terminals.
a) With a good capacitor, the
indicator should first move zero, and
then gradually increase to infinity.
b) If there is no movement of the
ohmmeter indicator, an open circuit is
indicated.
c) If the ohmmeter indicator
moves to zero, and remains there or on
a low resistance reading, a short circuit
is indicated. Defective capacitors
should be replaced.
4. If the correct voltage is available at
the compressor terminals, and no
current is drawn, remove all wires from
the terminals and check for continuity
through the motor windings. On single
phase motor compressors, check for
continuity from terminals C to R, and C
to S. On compressors with line break
inherent protectors, an open overload
protector can cause a lack of continuity.
If the compressor is warm, wait one
hour for the compressor to cool and
recheck. If continuity cannot be
established through all motor windings,
the compressor should be replaced.
Check the motor for ground by means
of a continuity check between the
common terminal and the compressor
shell. If there is a ground, replace the
compressor.
5. If the compressor has an external
protector, check for continuity through
the protector or protectors.
All external inherent protectors on
compressors can be replaced in the
field.
IF THE MOTOR COMPRESSOR
STARTS BUT TRIPS
REPEATEDLY ON THE
OVERLOAD PROTECTOR
1. Check the compressor suction and
discharge pressures while the
compressor is operating. Be sure the
pressures are within the limitations of
the compressor. If pressures are
excessive it may be necessary to clean
the condenser, purge air from the
system, replace crankcase pressure
regulating valve.
An excessively low suction pressure
may indicate a loss of charge.
On units with no service gauge parts
where pressures can be checked, check
condenser to be sure it is clean and fan
is running. Excessive temperatures on
suction and discharge line may also
indicate abnormal operating conditions.
2. Check the line voltage at the motor
terminals while the compressor is
operating. The voltage should be
within 10% of the nameplate voltage
rating. If outside those limits, the
voltage supply must be brought within
the proper range, or a motor
compressor with different electrical
characteristics must be used.
3. Check the amperage drawn while
the compressor is operating. Under
normal operating conditions, the
amperage drawn will seldom exceed
110% of the nameplate amperage.
High amperage can be caused by low
damage, defective running capacitors,
or a defective starting relay.
Continued on next page
MAINTENANCE, CARE & CLEANING
MAINTENANCE, CARE & CLEANING