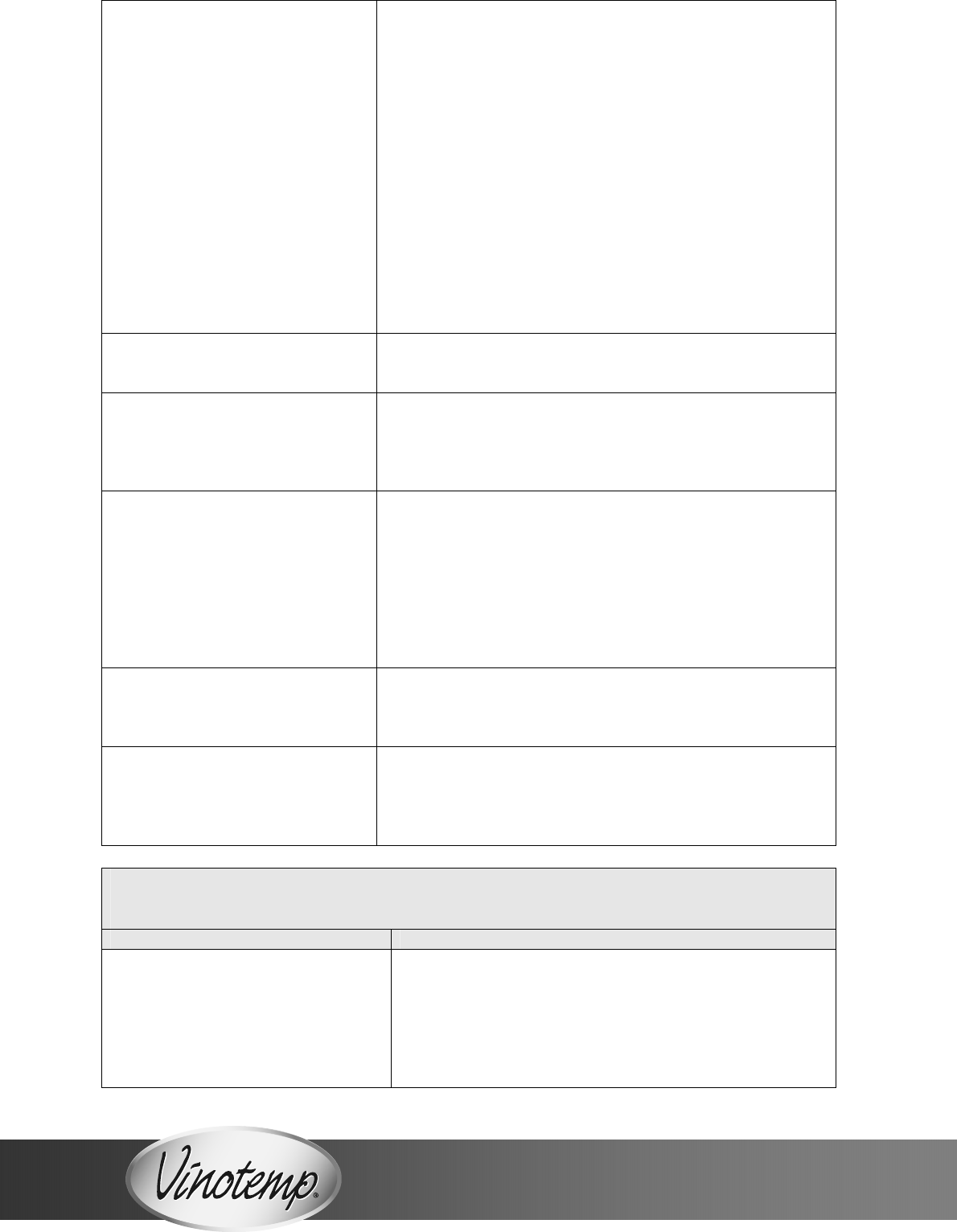
5) Beer is too warm • Temperature at faucet must always be at least 2
degrees colder than at barrel.
• In sweet-water refrigerated, or ice-water system,
faucet shank must always be submerged.
• In Cold Air System, the coldest air from the
blower must first be directed to the faucet, and
then circulated back to pre-cooler.
• Insulate all beer lines; a long beer run must be
constantly refrigerated. Insulation helps. But
insulation is not refrigeration.
• Keep all beer lines away from hot water pipes, hot
air ducts, and steam lines. A cold steam pipe in
the summer is a hot steam pipe in the winter.
• If direct draw temperature cannot be lowered,
increase applied pressure; however, balance the
system by changing to smaller diameter length of
vinyl tubing or install a foam control faucet.
6) No cold storage space for
delivered beer
• Keep kegs refrigerated at all times.
7) Too much air pressure • Too much pressure if using straight CO
2
will over
carbonate the beer. Check source of pressure.
Adjust pressure to suit properly balanced system.
• Check for proper regulator function and replace a
creeping regulator and gauge.
8) Excess CO
2
• Adjust pressure when using CO
2
as low as
possible, however, remembering that the applied
pressure must be slightly higher than the internal
pressure of the beer (no more than 18 lbs. should
be applied.)
• The colder the beer and the higher the applied
CO
2
pressure, the more rapid the absorption of
CO
2
by the beer. This over-carbonates the beer,
causing Wild Beer.
9) Not enough pressure
• Make sure pressure is on. Always turn pressure on
before drawing beer.
• Check for defective air vents and clean or replace
as necessary.
10) Old Beer • Rotate stock. The oldest beer should be tapped
first; if beer has been allowed to stand in warm
temperature beyond 45° for any excessive length
of time, it may begin secondary fermentation.
• Store beer below 42° year round.
Problem: Tail End of Beer Keg
Note: Beer draws best at the beginning of the barrel. Towards the end of the barrel, the
beer may be flat. This is more likely to occur when beer turnover is slow.
Causes Corrections
1) Where air is used as a
pressure source, air replaced the
CO
2
in beer causing flat beer.
Where beer is being drawn
rapidly, this problem is not so
evident.
• Wherever possible, CO
2
gas should be used as
pressure source.
• In high-pressure systems where CO
2
gas cannot
be used, a banner air-gas Blender should be
installed. This introduces a small amount of CO
2
back into the beer, thus maintaining normal CO
2
content in beer.
16
WWW.VINOTEMP.COM