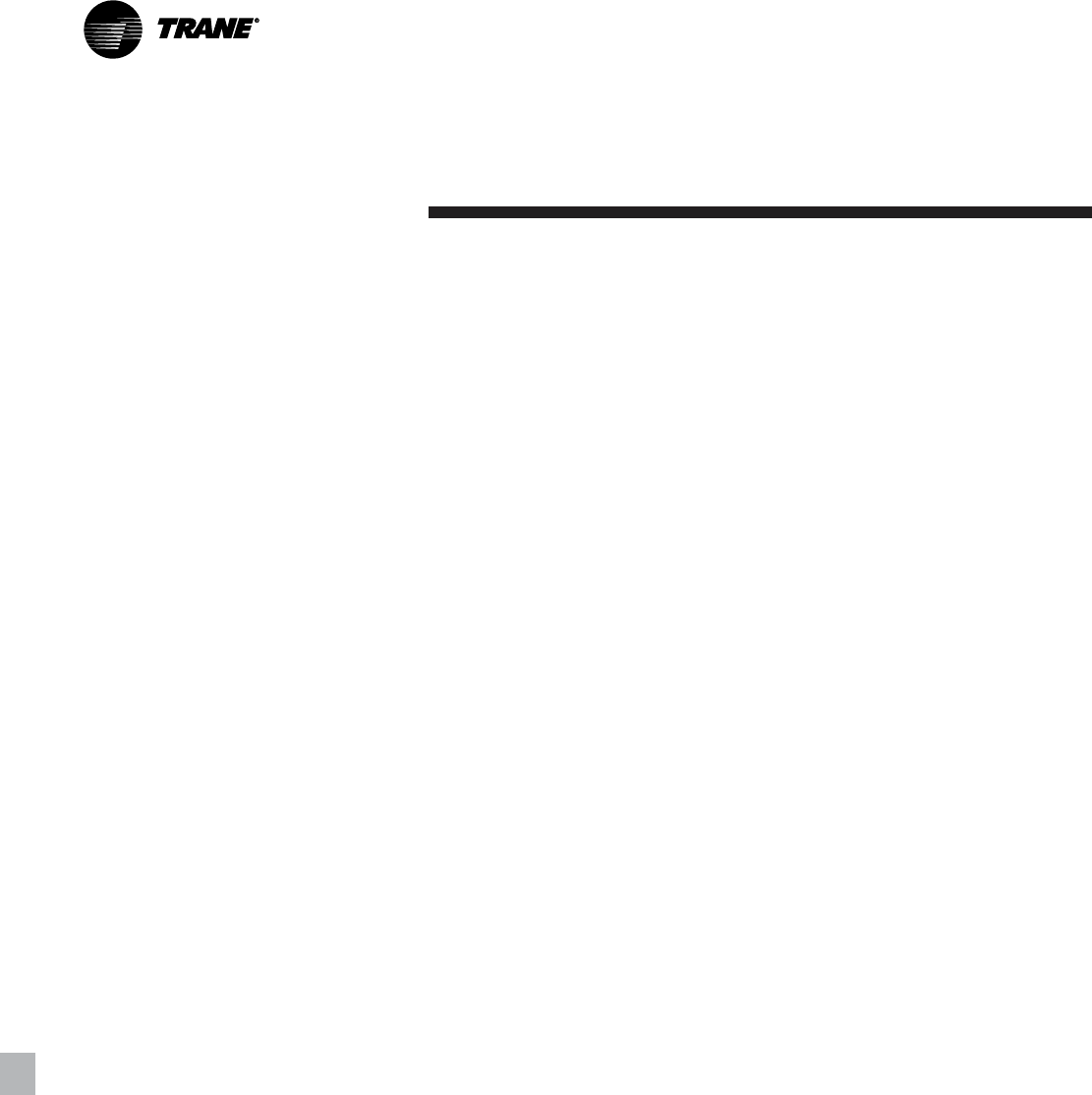
CG-PRC012-EN38
General
All scroll chillers are factory tested and
monitored for power and control
operation (CGWF only). CGWF units ship
with a full operating charge of refrigerant
and oil. CCAF units ship with a full
operating charge of oil. Exposed
surfaces are painted with an air-dry
beige primer-finisher prior to shipment.
Compressor-Motor
Direct-drive, hermetic, 3600 rpm, 60 Hz
[3000 rpm, 50 Hz] fixed compression,
scroll compressors (20 to 30 tons - two
compressors; 40 to 60 tons - four
compressors). Each compressor has:
centrifugal oil pump, oil level sightglass,
oil charging valve, two point lubrication
for each motor bearing, flooded
lubrication for the journal and thrust
bearings, and a check valve on the scroll
discharge port.
Motor is suction gas-cooled,
hermetically sealed, two-pole, squirrel
cage induction type.
Evaporator
Shell and tube design with seamless
copper tubes roller expanded into tube
sheets. Designed, tested and stamped in
accordance with ASME Code for
refrigerant side working pressure of 300
psig. Water side working pressure is 300
psig for CGWF 20-50 and CCAF 20-60,
215 psig for CGWF 60. One water pass
with a series of internal baffles. Each
shell includes drain connections,
entering and leaving temperature
sensors, and ¾ inch Armaflex II (or
equal) insulation (K= 0.26).
Condenser (CGWF only)
Shell and tube design with seamless
internally enhanced copper tubes.
Designed, tested and stamped in
accordance with ASME Code (CGWF 60
only) the refrigerant side working
pressure of 450 psig. Water side
working pressure is 300 psig for CGWF
20-50, 150 psig for CGWF 60. Two pass
construction with six-inch diameter shell
(20 to 30 tons). One pass construction
with two separate condensers connected
in series (40 to 60 tons). Each condenser
includes a subcooler circuit. Tubes are
cleanable and replaceable.
Refrigerant Circuit
Each refrigeration circuit shall be
completely independent and shall
include liquid line and discharge line
service valves, filter dryer, combination
moisture indicator-sightglass, charging
port, insulated suction line, liquid line
solenoid valve and thermal expansion
valve.
Isolation valves provide means of
isolating refrigerant charge in either the
high or low pressure side while
servicing. One refrigerant circuit on
20 to 30 tons; two refrigerant circuits on
40 to 60 tons.
Condenserless units (CCAF) shall be
equipped with discharge check valve
and moisture indicator sightglass.
Unit Controls (CH530)
The microprocessor-based control panel
is factory-installed and factory-tested.
Chilled water reset based on return
water is standard.
The CH530 microprocessor
automatically acts to prevent unit
shutdown due to abnormal operating
conditions associated with low
evaporator refrigerant temperature, high
condensing temperature, and/or motor
current overload. If an abnormal
operating condition continues and the
protective limit is reached, the machine
should shut down.
The panel includes machine protection
shutdown requiring
manual reset
for the
following conditions:
• low evaporator refrigerant temperature
and pressure
• high condenser refrigerant pressure
• critical sensor or detection circuit faults
• motor current overload
• high compressor discharge
temperature
• lost communication between main
processor and LLID
• electrical distribution faults: current loss
or phase reversal
• external and local emergency stop
• starter contactor interrupt failure
The panel also includes machine
protection shutdown with
automatic
reset
for the following correctable
conditions:
• power loss
• loss of evaporator or condenser water
flow
When a fault is detected, the control
system conducts more than 60
diagnostic checks and displays results.
The display will identify the fault,
indicate date, time, and operating mode
at time of occurrence, and provide type
of reset required and a help message.
The diagnostic history will display the
last ten diagnostics with their times and
dates of occurrence.
Mechanical
Specifications