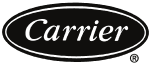
25
D. Unit shall be shipped with firmly attached labels that
indicate name of manufacturer, chiller model num-
ber, chiller serial number, and refrigerant used.
E. If the unit is to be exported, the manufacturer shall
provide sufficient protection against sea water corro-
sion, making the unit suitable for shipment in a
standard open top ocean shipping container.
F. Chiller and starter shall be stored indoors, protected
from construction dirt and moisture. Chiller shall be
inspected under shipping tarps, bags, or crates to be
sure water has not collected during transit. Protec-
tive shipping covers shall be kept in place until
machine is ready for installation. The inside of the
protective cover shall meet the following criteria:
1. Temperature is between 40 F (4.4 C) and
120 F (48.9 C)
2. Relative humidity is between 10% and 80%
non-condensing.
1.04 WARRANTY
Warranty shall include parts and labor for one year
after start-up or 18 months from shipment, which-
ever occurs first. A refrigerant warranty shall be
provided for a period of 5 years.
Part 2 — Products
2.01 EQUIPMENT
A. General:
Factory-assembled, single piece, liquid chiller shall
consist of compressor, motor, VFD, lubrication sys-
tem, cooler, condenser, initial oil and refrigerant
operating charges, microprocessor control system,
and documentation required prior to start-up.
B. Compressor:
1. One variable speed, tri-rotor screw compressor
of the high performance type.
2. Compressor and motor shall be hermetically
sealed into a common assembly and arranged
for easy field servicing.
3. The compressor motor shall be accessible for
servicing without removing the compressor
base from the chiller. Connections to the com-
pressor casing shall use O-rings and gaskets to
reduce the occurrence of refrigerant leakage.
Connections to the compressor shall be flanged
or bolted for easy disassembly.
4. Compressor bearings must have individual
design life of 500,000 hours or greater.
5. Compressor shall provide capacity modulation
from 100% to 15% capacity without the use of
hot gas bypass or mechanical unloaders.
6. Compressor shall be provided with a factory-
installed positive pressure lubrication system to
deliver oil under pressure to bearings and rotors
at all operating conditions. Lubrication system
shall include:
a. Oil pump with factory-installed motor con-
tactor with overload protection.
b. Oil pressure sensor with differential readout
at main control center.
c. Oil pressure regulator.
d. Oil filter with isolation valves to allow filter
change without removal of refrigerant
charge.
e. Oil sump heater [115 v, 50 or 60 Hz] con-
trolled from unit microprocessor.
f. Oil reservoir temperature sensor with main
control center digital readout.
g. All wiring to oil pump, oil heater, and con-
trols shall be pre-wired in the factory and
power shall be applied to check proper
operation prior to shipment.
7. Compressor shall be fully field serviceable.
Compressors that must be removed and
returned to the factory for service shall be
unacceptable.
8. Acoustical attenuation shall be provided as
required, to achieve a maximum (full load
or part load) sound level, measured per AHRI
Standard 575 (latest edition).
C. Motor:
1. Compressor motor shall be of the semi-
hermetic, liquid refrigerant cooled, squirrel
cage, induction type suitable for voltage shown
on the equipment schedule.
2. If an open (air cooled) motor is provided, a
compressor shaft seal leakage containment
system shall be provided:
a. An oil reservoir shall collect oil and refriger-
ant that leaks past the seal.
b. A float device shall be provided to open
when the reservoir is full, directing the
refrigerant/oil mixture back into the com-
pressor housing.
c. A refrigerant sensor shall be located next to
the open drive seal to detect leaks.
3. Motors shall be suitable for operation in a
refrigerant atmosphere and shall be cooled by
atomized refrigerant in contact with the motor
windings.
4. Motor stator shall be arranged for service or
removal with only minor compressor disassem-
bly and without removing main refrigerant
piping connections.
5. Full load operation of the motor shall not
exceed nameplate rating.
6. One motor winding temperature sensor (and on
spare) shall be provided.
7. Should the mechanical contractor choose to
provide a chiller with an air-cooled motor
instead of the specified semi-hermetic motor,
the contractor shall install additional cooling