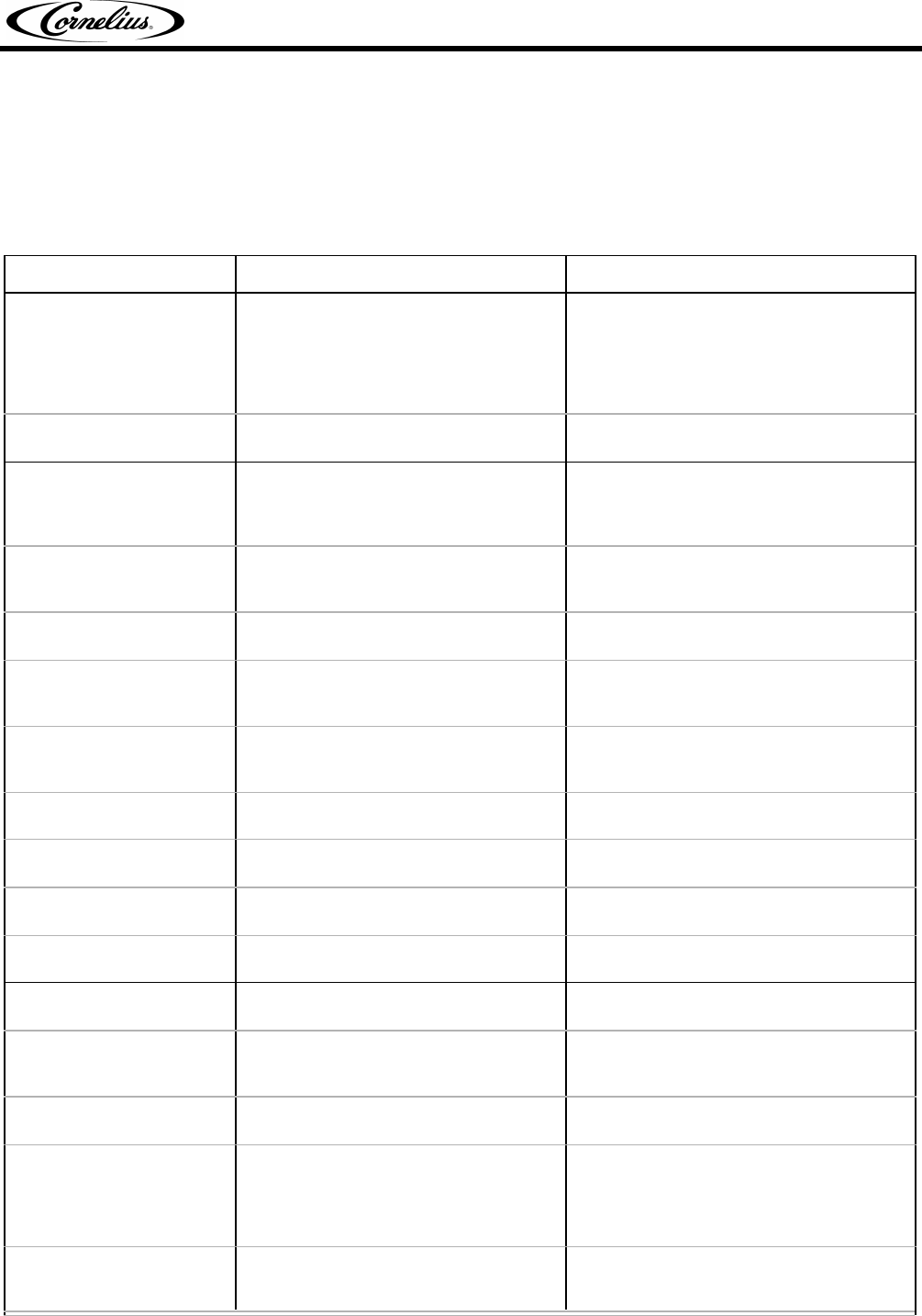
Quest Juice Training Manual
© 2004, IMI Cornelius Inc. - 35 - Publication Number: TP00968
TROUBLESHOOTING GUIDE
The following pages contain troubleshooting information intended to aid an experienced service person
in diagnosing operational problems that may occur. For further assistance, contact the IMI Cornelius
Technical Services department at 1-888-248-5568 (630-539-6850 outside the United States) between
the hours of 7:30A.M. and 5:00P.M. Central Standard Time. You must have the model and serial number
(Located on the right side of the dispenser) prior to calling.
PROBLEM PROBABLE CAUSE REMEDY
Totally Inoperative • No power to dispenser due to
tripped circuit breaker
• Reset circuit breaker. Confirm that
breaker is correct size and no other
equipment is operating on the same
circuit. Also confirm that supply volt-
age is +/- 10% of nameplate specifi-
cations.
• Loose or broken power supply
connection inside dispenser.
• Repair connection.
No cooling • Line voltage is not within +/-
10% of nameplate specifications
causing compressor overload to
trip
• Contact an electrician
• No water in water ice bath or
water level extremely low exposing
the ice bank sensing probe
• Fill ice bath to proper water level
• Defective Ice Bank Control or
sensing probe
• Replace
• Cabinet fan is inoperative result-
ing in warm concentrate (water
continues to cool)
• Replace
• Compressor short cycles on
overload
• Excessively high discharge pres-
sure due to restricted condenser or
inoperative condenser fan motor
• Compressor starts but hums
and trips overload
• Seized or shorted compressor,
replace
• Defective compressor overload
or start capacitor
• Test and replace
• Compressor starts but does not
switch off of start winding
• Relay or compressor is defective.
Test and replace faulty item
• Refrigerant leak • Repair leak, evacuate and
recharge system
No water dispensed,
concentrate only
• No water to dispenser • Restore Water
• Water supply line inside refriger-
ated cabinet disconnected from
pump platform
• Reconnect
• Water solenoid located on pump
platform clogged or defective
• Disassemble and clean solenoid.
Replace if necessary.
• Main water solenoid/strainer
located at the rear of dispenser is
clogged, binding or defective
• Remove and clean strainer. Con-
firm 28VDC is present at solenoid
during dispense. Confirm solenoid
coil is not open. Disassemble and
clean solenoid.
• Water supply pressure is
greater than 80 psi (5.5 bar) forc-
ing the brix flow control closed
• Add external regulator and lower
pressure to 50 psi (3.5 bar)