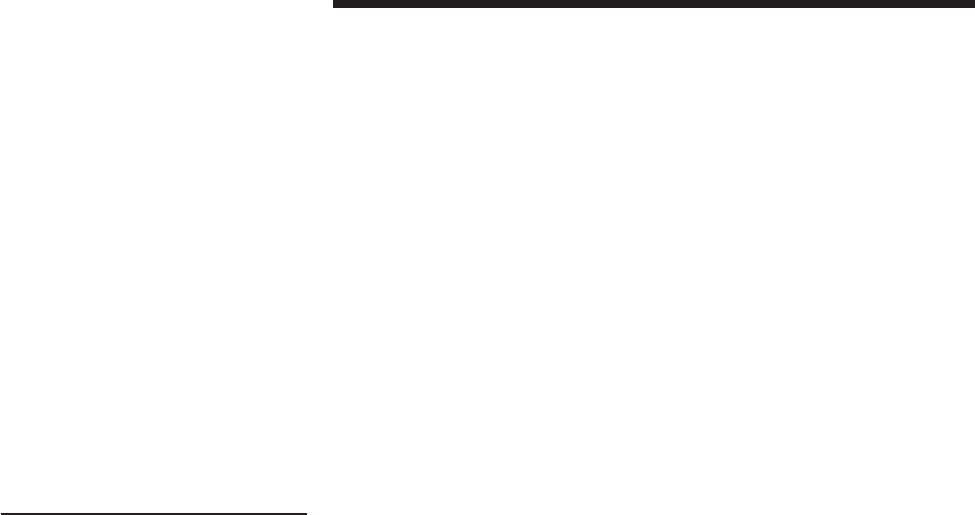
9
• Do not start the motor more than six times per hour. Short cycling
the tower will cause fuses, breakers or O.L.s to operate and will
decrease motor life.
When using a two-speed starter:
• Motor rotation must be the same at slow speed and high speed.
• Single winding motor requires a starter with a shorting contactor.
• Two-winding motor requires a starter with out a shorting
contactor.
• All two-speed starters must have a 20 second time delay relay
when switching from high speed to low speed.
• Do not start the motor more than six times per hour (each low
speed start and each high speed start count as one start).
When using a VFD:
Before beginning, ensure that the motor is rated for “Inverter Duty”
perNEMAMG-1,part31.
• Set the VFD solid state overload protection to 119% of motor
nameplate amps and set “maximum current parameter” in the
VFD to motor nameplate amps. “Maximum current parameter” will
reduce fan speed and limit amp draw to nameplate amps during
cold weather operation. If furnished with a mechanical O.L. set this
at 110% over motor nameplate amps.
• Motor rotation must be the same in both VFD mode and By-pass
mode.
• If cable distance between the VFD and motor is greater than 100
feet a DV/DT output lter is recommended to avoid damage to the
motor. 100 feet distance is based on our eld experience, the VFD
manufacture may state different distances and distance does vary
depending on the VFD manufacture.
• Program the VFD for variable torque output. Flux vector and con-
stant torque modes may damage the gearbox.
• Do not start and stop the motor using the safety switch at the motor.
If the drive is being commanded to run and the load side is cycled
ON and OFF with the safety switch this may damage the VFD.
Using a VFD in cooling applications has advantages over traditional single
or two speed motor control. A VFD can reduce the cost of electrical en-
ergy being used and provide better temperature control. In addition, it
reduces the mechanical and electrical stress on the motor and mechanical
➠
Installation
Note