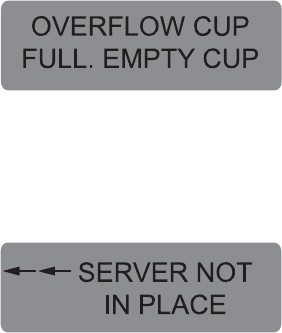
Page 36
29877 121302
TROUBLESHOOTING
A troubleshooting guide is provided to suggest probable causes and remedies for the most likely problems
encountered. If the problem remains after exhausting the troubleshooting steps, contact the Bunn-O-Matic
Technical Service Department.
• Inspection, testing, and repair of electrical equipment should be performed only by qualified service
personnel.
• All electronic components have 120 - 240 volt ac and low voltage dc potential on their terminals.
Shorting of terminals or the application of external voltages may result in board failure.
• Intermittent operation of electronic circuit boards is unlikely. Board failure will normally be
permanent. If an intermittent condition is encountered, the cause will likely be a switch contact or
a loose connection at a terminal or crimp.
• Solenoid removal requires interrupting the water supply to the valve. Damage may result if
solenoids are energized for more than ten minutes without a supply of water.
• The use of two wrenches is recommended whenever plumbing fittings are tightened or loosened.
This will help avoid twists and kinks in the tubing.
• Make certain that all plumbing connections are sealed and electrical connections tight and isolated.
• This brewer is heated at all times. Keep away from combustibles.
WARNING
• Exercise extreme caution when servicing electrical equipment.
• Disconnect the brewer from the power source when servicing, except when electrical tests are
specified.
• Follow recommended service procedures.
• Replace all protective shields or safety notices.
Screen Displayed
Possible Cause
Troubleshooting Procedures
1. Overflow cup is full of water.
1. Soft Heat
®
Server not correctly
positioned on base.
2. Not using a Soft Heat
®
Server, and
the SERVER DETECT function is ac-
tivated (on).
Empty cup
Position the server so that the con-
nector pins on the server make con-
tact with connector on the brewer.
Disable the SERVER DETECT func-
tion. See page 32 for procedure.