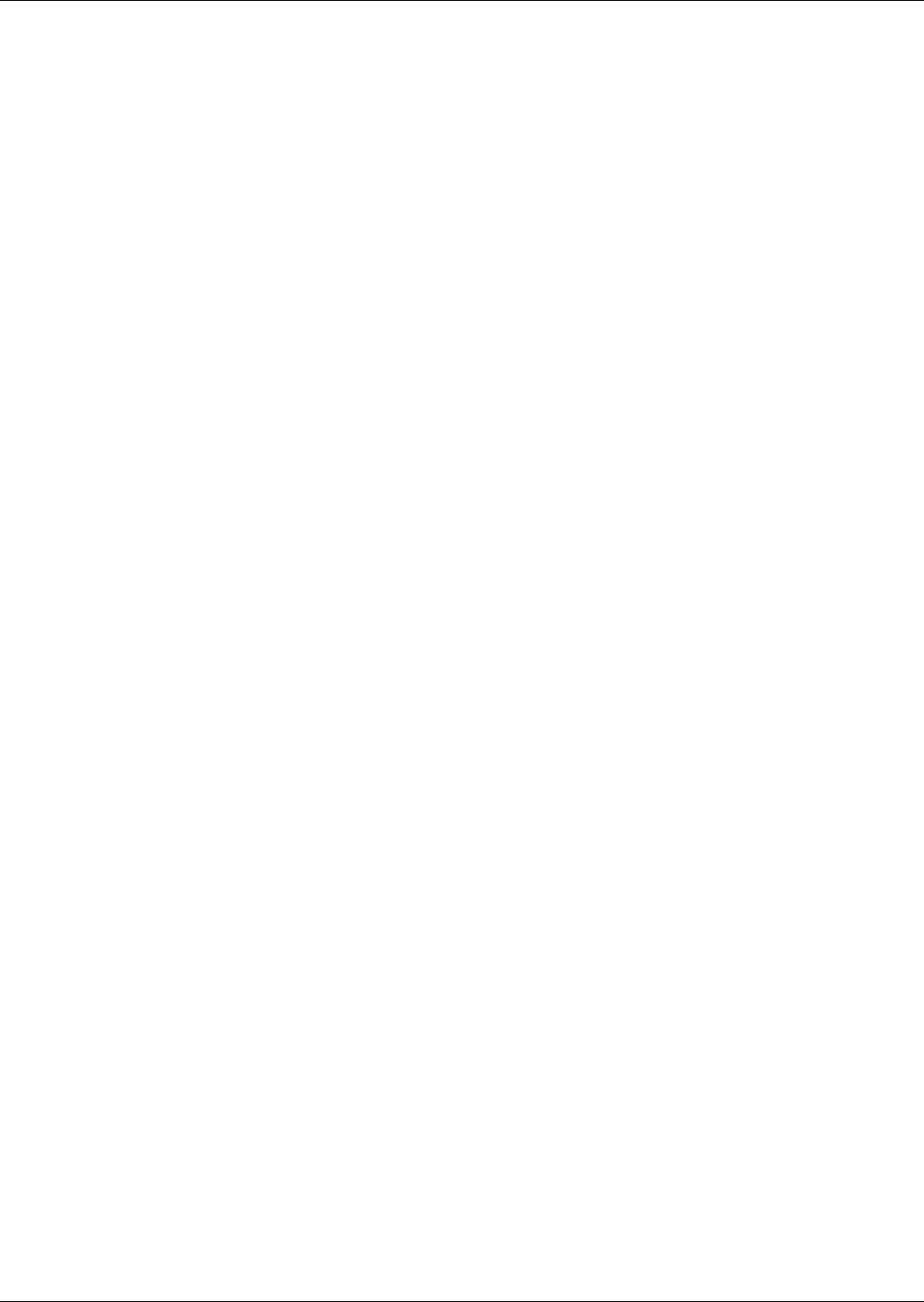
Response by Control Type—Advanced Microprocessor Controls
36
Dual Cooling Source Dehumidification
When dual cooling is available, the humidity control will calculate a total dehumidification require-
ment of 200% rather than 100%. The cooling valve opens proportionally as the requirement for dehu-
midification rises from 0 to 100%. If more than 100% dehumidification is required, then the
compressors are activated at 150% and 200% respectively. Dual cooling is available if the entering
chilled water temperature is 14°F (50% capacity) below the return air temperature. If dual cooling is
not available, the humidity control will operate the compressors in the same manner as a 2-stage
dehumidification system.
Chilled Water Dehumidification
The chilled water control valve is adjusted proportionally as the humidity control varies the require-
ment for dehumidification from 0 to 100%.
5.2.4 Humidification Operation
System Activation
The humidifier (infrared or steam) is activated when the humidity control calculates a requirement of
100% humidification, and deactivated when the requirement falls below 50%.
5.2.5 Control Types
Proportional Control
This is a standard control method that maintains the room at a temperature proportional to the load.
The temperature maintained increases as the room load increases. At full load the room would be con-
trolled at a temperature equal to the temperature setpoint plus the temperature sensitivity. If Pro-
portional Control is selected, the gain is factory set and cannot be adjusted by the user. Operator
inputs are the usual setpoint and sensitivity adjustments.
PID Control
The PID Control combines three individual terms to determine the control output for a given set of
conditions. Note that PID Control is used only for temperature. If PID Control is selected, humidity
will continue to use Proportional Control.
The proportional (P term) is determined by the difference between the current temperature and the
control setpoint. This term is expressed in % cooling (heating) desired for each degree above (below)
the setpoint. It is adjustable from 0% to 100% per degree. The purpose of this term is to adjust the
control output for any deviation between the current temperature and the control setpoint.
The integral (I term) is determined by two things: the difference between the temperature and control
setpoint and the amount of time this difference has existed. This term is expressed in % cooling (heat-
ing) desired for each minute and degree above (below) the setpoint. It is adjustable from 0% to 100%
per degree-minute. The purpose of this term is to force the control to maintain the temperature
around the setpoint by slowly but continuously adding (subtracting) a small amount of cooling (heat-
ing) to the total control output until the temperature is at the setpoint.
The derivative (D term) is determined by the rate of change of temperature. This term is expressed in
% cooling (heating) desired for each degree per minute rise (fall) in temperature. It is adjustable from
0% to 100% per degree/min. The purpose of this term is to adjust the control output for quickly chang-
ing temperatures, thus providing an anticipation control.
All three types are adjusted in the Select Control Type menu, a submenu of the Setup System menu.
If PID Control is selected, the temperature sensitivity setting is not used by the control.
For optimum performance, a PID Control must be adjusted or tuned according to the characteristics
of the particular space and load to be controlled. Improper tuning can cause the control to exhibit poor
response and/or hunting. The characteristics of the space and load may change seasonally, so occa-
sional retuning is required for optimum performance.