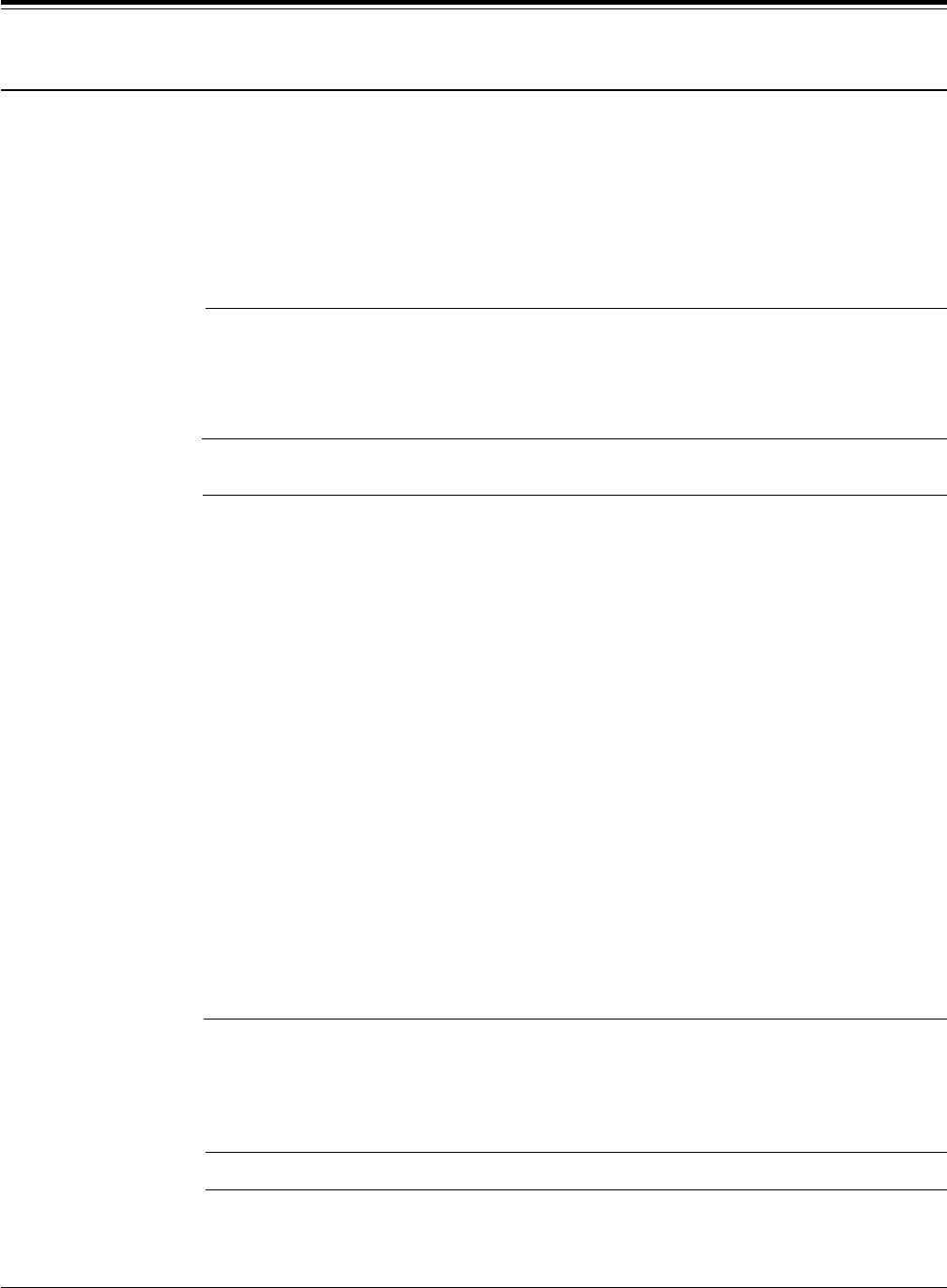
25
1a. Clean or replace drain line flow
control
2a. Check for minimum specified flow and
pressure requirements of filter system
3a. (Generally will only plug with the
presence of iron bacteria) Clean
aeration assembly and shock treat
the water supply with chlorine as
needed to control iron bacteria
4a. Rebed filter and correct the cause of
fouling
1a. Assure continuous electrical supply
(check plug, breaker, fuses, etc.)
2a. Replace timer motor
3a. Replace skipper wheel
4a. Replace 24 hour gear or timer
assembly
1a. Consult factory
1a. Check installation position of check
valve – Consult Installation and
Operation Manual for proper position
1b. Check for foreign material in seat of
check valve, clean or replace as
required
2a. Check aeration tank assembly and air
recharge line and fittings for any air
leaks and repair (Note: soapy water
solution works well for locating air
leaks)
3a. Assure permanent electrical service
(check plug, breaker, fuses, terminal
block on control valve, etc.)
3b. Check for adequate pressure and
volume production from air pump.
Repair or replace air pump
3c. Repair or replace check valve, and
clean, repair or replace aeration
pump
3d. Clean, repair or replace aeration
pump, ventilate environment or
provide external air source
4a. Increase regeneration frequency of
filter or Iron Curtain Remote Control
Center
1a. Install a flow control at filter system
outlet equal to or less than the design
flow rate of filter system
1b. Install additional filter(s) or a larger
single filter system which meets both
the service flow demand and
backwash flow requirements available
1a. Reset timer
1a. Assure all adapter base o-ring seals
are in place
1b. Replace seals, spacer and piston
assemblies
Troubleshooting
Complaint Problem Cause Solution
Iron or manganese* bleed-
through or staining
Sulphur odor bleed-through
*Manganese can be slow to oxidize when the pH is less than 8.5
1. Plugged drain line flow control
2. Insufficient water supply from well
3. Plugged aeration tank inlet
diffuser or pick-up tube
4. Media bed fouled
1. Interrupted electrical service
2. Faulty timer motor
3. Faulty skipper wheel
4. Faulty 24 hour gear
1. It is not uncommon for local water
conditions to change
1. Loss of air through inlet check
valve
2. Loss of air through air leak
3. Faulty aeration pump due to:
a. Electrical failure
b. Pneumatic failure
c. Faulty air line check valve
allowing water to back up
through aeration pump during
regeneration cycle
d. Damp environment
4. Air loss through high demand
1. Service flow rate demand is
higher than filter system design
flow rate
1. Time of day set incorrectly
1. Internal control valve leak
A. Inadequate backwash of filter
B. Fails to regenerate
C. Water contaminant levels are
greater than limits established by
the manufacturer
D. Inadequate aeration
E. Exceeding recommended filter
system flow rate
F. Regeneration during service flow
demand
G. Raw water bleeding through filter