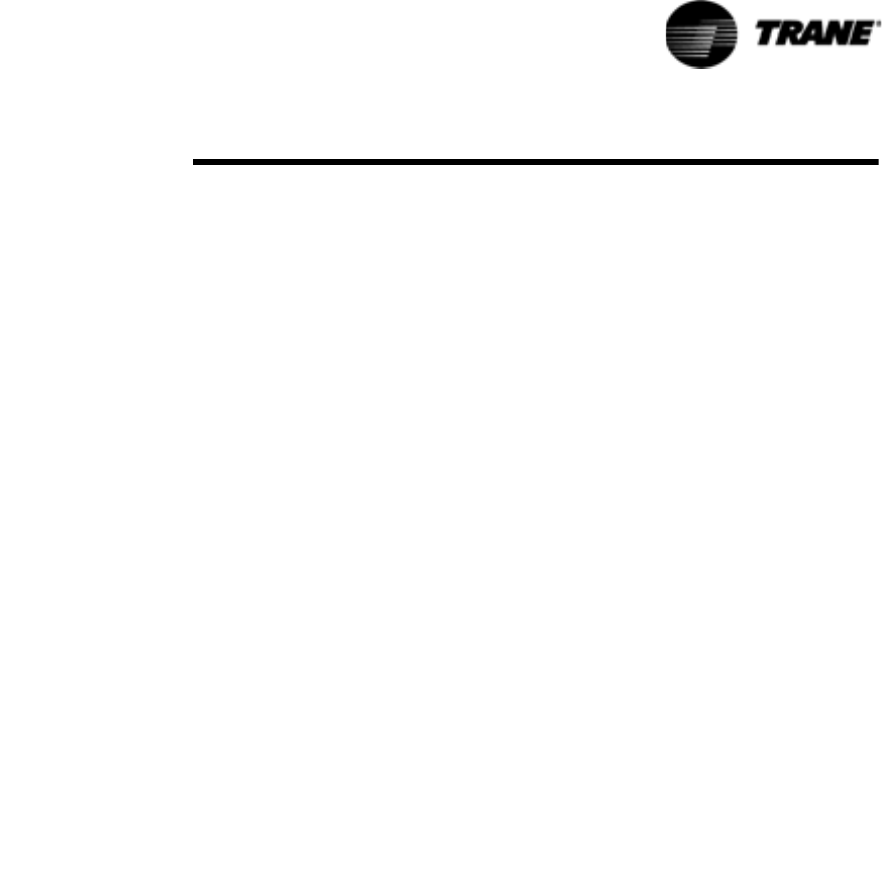
RLC-SVD03A-EN 67
Module Power and Miscellaneous I/O
SEHI Electronic Expansion Valve Servicing
The procedures listed below are to. be followed for proper disassembly,
inspection, cleaning and reassembly to the valve. The valve does not need to
be removed from the refrigerant piping before servicing. If the motor is found
to be defective the entire motor assembly must be replaced.
1. Before disassembly of the valve, be sure the refrigerant pressure in the
system has been reduced to a safe level (0 psig) on both sides of valve.
See RTAA-SB-10 for preferred refrigerant handling in this area.
ƽ WARNING
Hazardous Voltage w/Capacitors!
Disconnect all electric power, including remote disconnects
before servicing. Follow proper lockout/tagout procedures to
ensure the power cannot be inadvertently energized. For variable
frequency drives or other energy storing components provided by
Trane or others, refer to the appropriate manufacturer’s literature
for allowable waiting periods for discharge of capacitors. Verify
with an appropriate voltmeter that all capacitors have discharged.
Failure to disconnect power and discharge capacitors before
servicing could result in death or serious injury.
Note: For additional information regarding the safe discharge of
capacitors, see PROD-SVB06A-EN or PROD-SVB06A-FR
2. Disconnect all the line voltage to the power supply of this unit.
3. Refer to the exploded view in Figure 19 while performing the remaining
instructions.
4. Unplug valve.
5. Using the appropriate wrenches or a vice to properly support the valve
body, remove the motor assembly from the valve body by loosening the
lock nut. To prevent permanent damage to the motor, DO NOT attempt to
disassemble the motor housing.
NOTE: Regardless of whether the valve is in the system or in a vise,
care must be taken to prevent distorting the valve parts when tight-
ening.
6. Verify that the new motor assembly is in the "OPEN" position.
7. Lightly oil the threads and knife-edge on the new motor adapter. Carefully
seat the adapter on the valve body.
8. Engage and tighten the lock nut. One eighth turn more than hand tight is
sufficient to achieve a leak proof seal.
9. Pressurize the system and check for leaks.