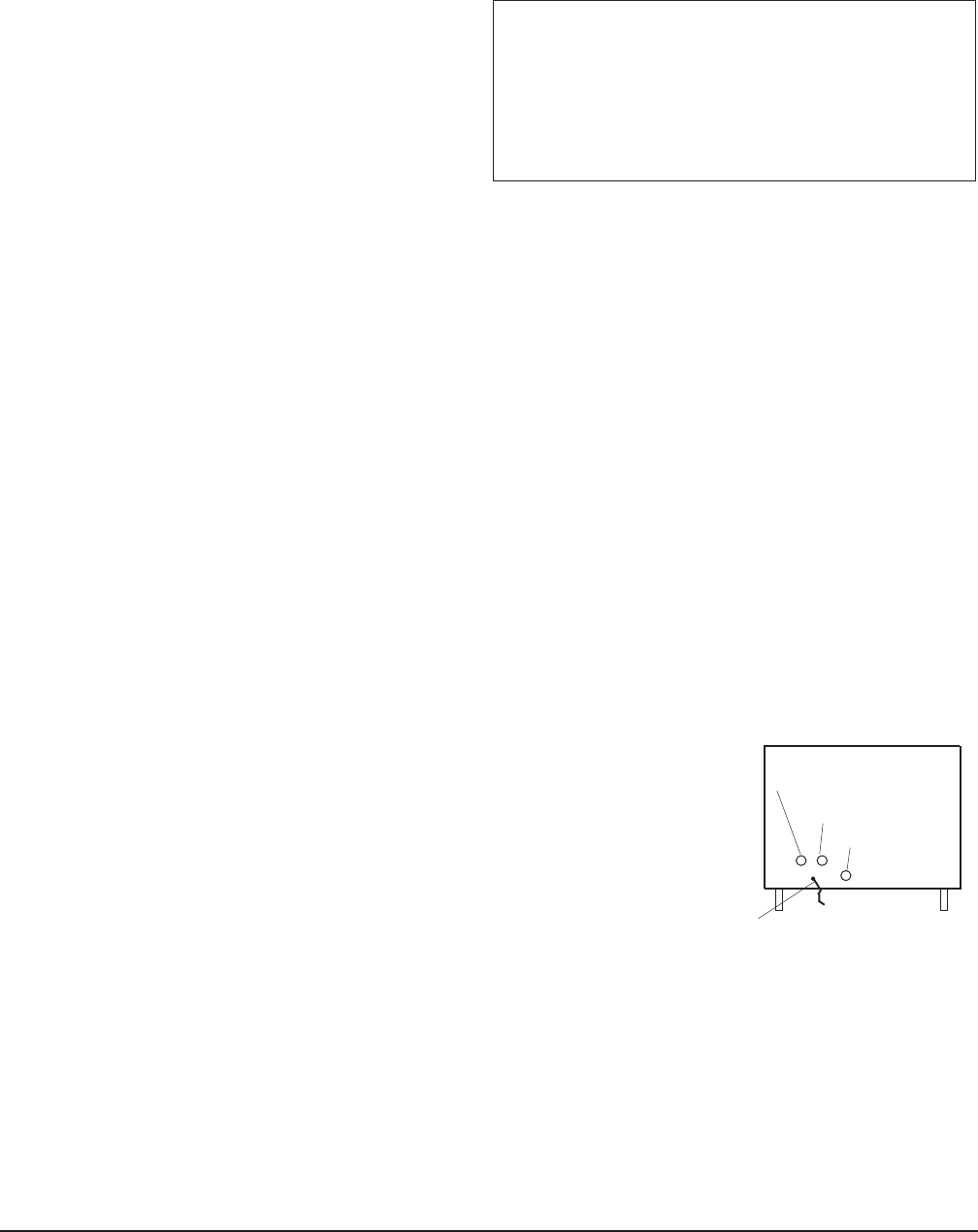
– 8 –
PLUMBING CONNECTIONS
WARNING: PLUMBING CONNECTIONS MUST COMPLY WITH APPLICABLE SANITARY, SAFETY
AND PLUMBING CODES.
Water Requirements
Proper water quality can improve the taste of the
food prepared in the steamer, reduce liming in the
steam generator and extend equipment life. Local
water conditions vary from one location to another.
Ask your municipal water supplier for details about
your local water supply prior to installation.
Presence of sediment, silica, excess chlorides or other dissolved solids may lead to a recommendation
for alternate form(s) of water treatment. Test the water with the test strip included with the combi oven.
Other factors affecting steam generation are iron content, amount of chloridation and dissolved gases.
A local water treatment specialist should be consulted before installation of steam generating
equipment.
Water Supply Connections (Fig. 2)
A water filter system is recommended for the water supply line going to the treated water inlet of your
oven. Follow the recommendations for use and installation instructions shipped with the water filter.
If a water filter is not installed, the oven warranty may be limited.
Connect treated potable water ( must be cold) to the inlet labeled for treated water to supply the steam
generator tank. Untreated water contains scale producing minerals which, if supplied to the steam
generator, can precipitate onto the surfaces in the steam generator tank. Due to the temperatures in
the tank, the minerals can bake onto the surfaces and components. This can result in early component
failure and reduced product life. Sensors in the steam generator tank use ions in the water to detect
the water level. Do not use distilled (fully demineralized or de-ionized) water as this could provide a
false reading to the sensors. Strainers and filters will NOT remove minerals from the water.
Connect untreated potable water (must be cold) to the inlet labeled for
untreated water to supply the condenser which cools the drain water.
Both external-threaded nylon inlets
3
/4" hose bibb (
3
/4" NSHT, National
Straight Hose Thread) are located at the rear of the oven. The nylon threads
should be treated carefully so the connections do not leak. A manual shutoff
valve should be provided, convenient to the oven, for each water supply line;
both of these valves should be open when the oven is in operation. Water
pressure for both incoming water lines should be between 20 and 60 psig.
Refer also to CLEAN CYCLE DELIMING PROCEDURE, page 38.
Drain Connection
CAUTION: In order to avoid any back pressure in the oven, do not connect solidly to any drain
connection.
The drain connection, 1
1
/2" NPT threaded fitting, is located underneath the oven at the rear. The drain
line must be plumbed to an open gap-type drain. Drain piping must have suitable pitch, have
appropriate support along its length and have no connection to other piping. The material used in the
drain line should be heat resistant to at least 212°F. The open drain should be located between 3 and
5 feet away from the perimeter of the oven to reduce potential damage from moisture-corrosion. The
drain line from the oven must not be combined with any drain line from another device.
Fig. 2
Water Supply Inlets . . .
at Bottom Rear Corner of Oven
. . . Model VCG10H Shown.
GAS SUPPLY
TREATED WATER
UNTREATED WATER
ELECTRIC SUPPLY CORD
WATER REQUIREMENTS
Supply Pressure 20 — 60 psig
Hardness* less than 3 grains
Silica less than 13 ppm
Total Chlorine less than 4.0 ppm
pH range 7 — 8
Undissolved Solids less than 5 microns
* 17.1 ppm = 1 grain of hardness