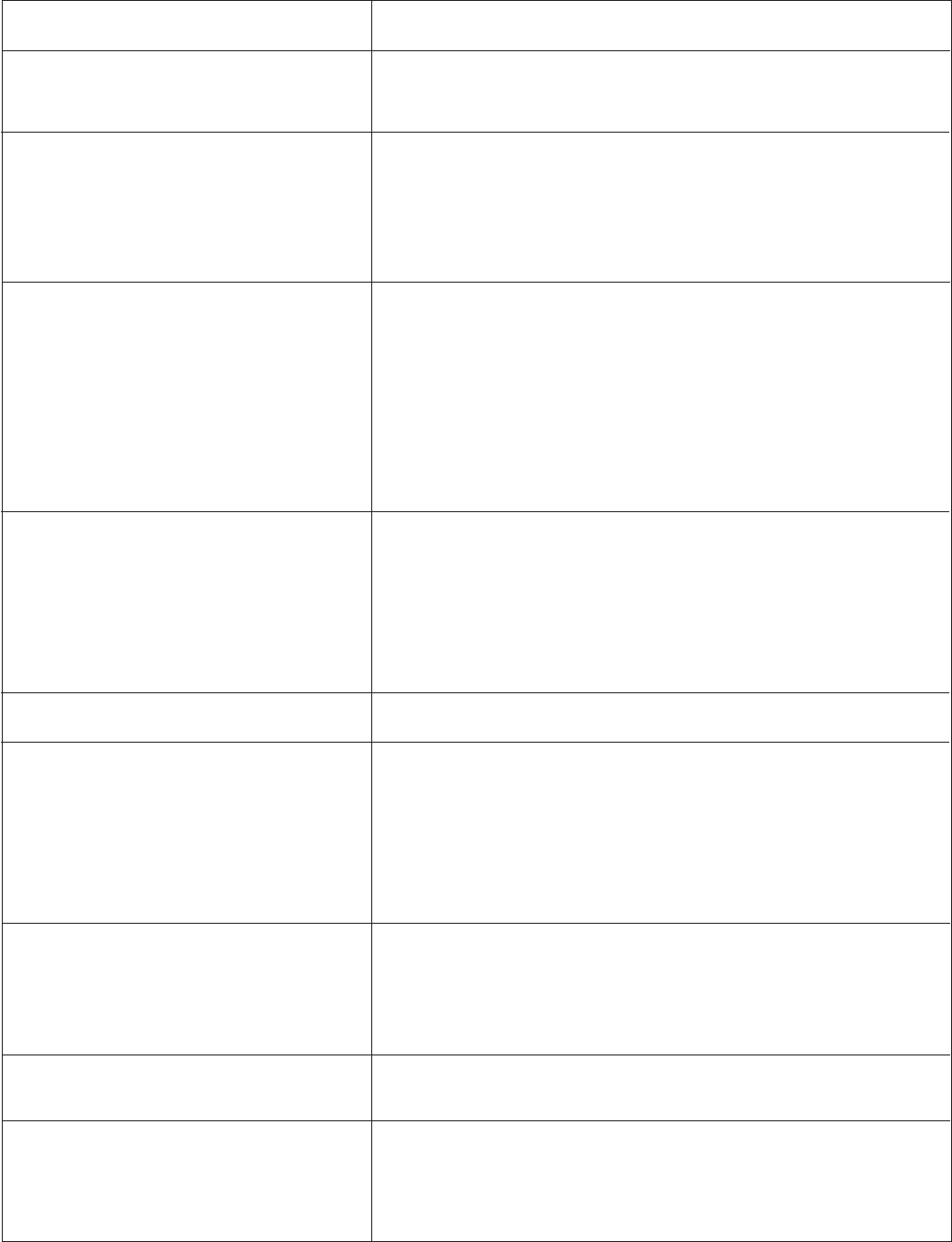
-20-
IX. TROUBLE SHOOTING GUIDE
1. Condensing unit fails to start when programming a new
batch.
2. Batch requires too much time to chill product down to
40° F. “Chill Cycles Batch Over 6-Hours” will ALARM
and a printout will note the chill cycle has exceeded
maximum safe time.
3. “Food Probe Failure” - ALARM will occur during a
chill cycle batch with printout noting the “Food Probe
Failure Warning.”
4. “Refrigeration Failure” - ALARM with a printout
noting the warning will occur when the interior
temperature exceeds 100° F for more than 20-minutes.
Blast Chill refrigeration system will shut down as a
safety default. The compressors and blower fans are
shut off and the control key pad is locked out.
5. “Power Loss Notification” - Printout notes the time
power was lost and the time in which it was restored.
6. Cannot program a new batch.
7. Printer not printing.
8. No display on control.
9. Condensation on exterior surface.
a. Check power supply to condensing unit.
b. Batch was not programmed properly, was START pressed after programming batch? If
“YES” the display should return to TIME and TEMPERATURE.
c. System problem. Call for service.
a. Is the door closed properly? If not, close door completely.
b. Too much product loaded. Adjust the load to not exceed capacity of the unit.
c. Product depth in pan exceeds 2-1/2”. Reduce pan load per guidelines on page 7.
d. Has pan been covered with a lid, plastic wrap or foil, and is this not in direct contact with
the product? Cover product correctly as per guidelines on page 7.
e. Perhaps the product loaded is of a high density. Allow additional chilling time.
f. Dirty condenser coil. Clean condenser as per instructions on page 6.
g. Evaporator coil iced. Allow to defrost (press DEFROST to initiate a manual defrost).
a. “Food Probe Failure” - printer will notify the operator that it is converting to Constant Chill
mode. Food probe(s) may not have been assigned while programming the chill cycle batch.
Review new batch procedures on page 13.
b. Press the food probe button, if the display reads “---”, press “PRINT.” If a (-99°) F probe
temperature is displayed then there is an open circuit. Check the probe plug connection.
c. Press the food probe button, if the display reads “---”, press “PRINT.” If a 500° F probe
temperature is displayed then there is an open circuit. Check the probe plug connection.
d. Food probe was placed in excessively hot product. Product temperatures exceeding
210° F can result in the probe reporting false temperatures. Cool food probe and test again.
f. Food probe fails and will then operate correctly at a later time. Program a Blast Chill batch
using the suspect probe. Wiggle the food probe wire. If a second “Food Probe Failure”
occurs the food probe is defective. Replace with new food probe.
g. Damaged or defective food probe. Replace with new food probe.
“Refrigeration Failure” CORRECTION - Remove power from the unit. Unplug and then
replug the unit or reset the circuit breaker (OFF and back ON). The Blast Chiller will reset
and turn ON. “Power Loss Failure” will printout when reset.
a. Batch programming was incomplete or incorrect and chill cycle did not start. Try program-
ming batch again.
b. Too much product loaded. Adjust the load to not exceed capacity of the unit.
c. Dirty condenser coil. Clean condenser as per instructions on page 6.
d. Refrigeration system failure, unit will not cool after having been reset. Call service for
repair.
a. Power was lost to the Blast Chill unit. If product was inside the unit see the 72-Hour Data
Log to determine if product temperature was compromised.
NOTE: Always press the “RESET” button twice to clear the old complete batch data from
memory before programming a new batch.
a. The LOCK feature may be activated. See page 13 to unlock the control.
b. Unit may be in a defrost cycle. Batch can be programmed at this time and will Auto Start
after the Defrost Cycle is complete.
c. Program chill cycle batch is in process, a new batch can be programmed after completion
of current batch.
d. A batch may have been only partially programmed. Press “RESET” twice to clear any
incomplete batch information.
a. Printer is out of paper. Replace printer paper roll as per instructions on page 6.
b. Printer ribbon is out of ink. Replace printer ribbon cartridge.
c. Printer paper may be installed incorrectly, allowing the paper to feed behind the printer
ribbon. Remove the paper from the printer and reinstall the paper as per instructions on
page 6.
d. Paper does not feed or jams behind the paper feed slot in the cover. Remove paper and
reinstall as per instructions on page 6.
a. Check power supply and circuit breaker.
b. Confirm unit is correctly plugged into a working power outlet.
c. System problem. Call for service.
Condensation on the exterior surface of the unit is perfectly normal during periods of high
humidity, otherwise refer below for other possible causes.
a. Check door alignment and gasket for proper seal.
b. On Roll-In/Roll-Thru models, check bottom door sweep for proper adjustment.
c. Electric door heater malfunction. Call for service.
SYMPTOM PROBABLE CAUSE/SOLUTION