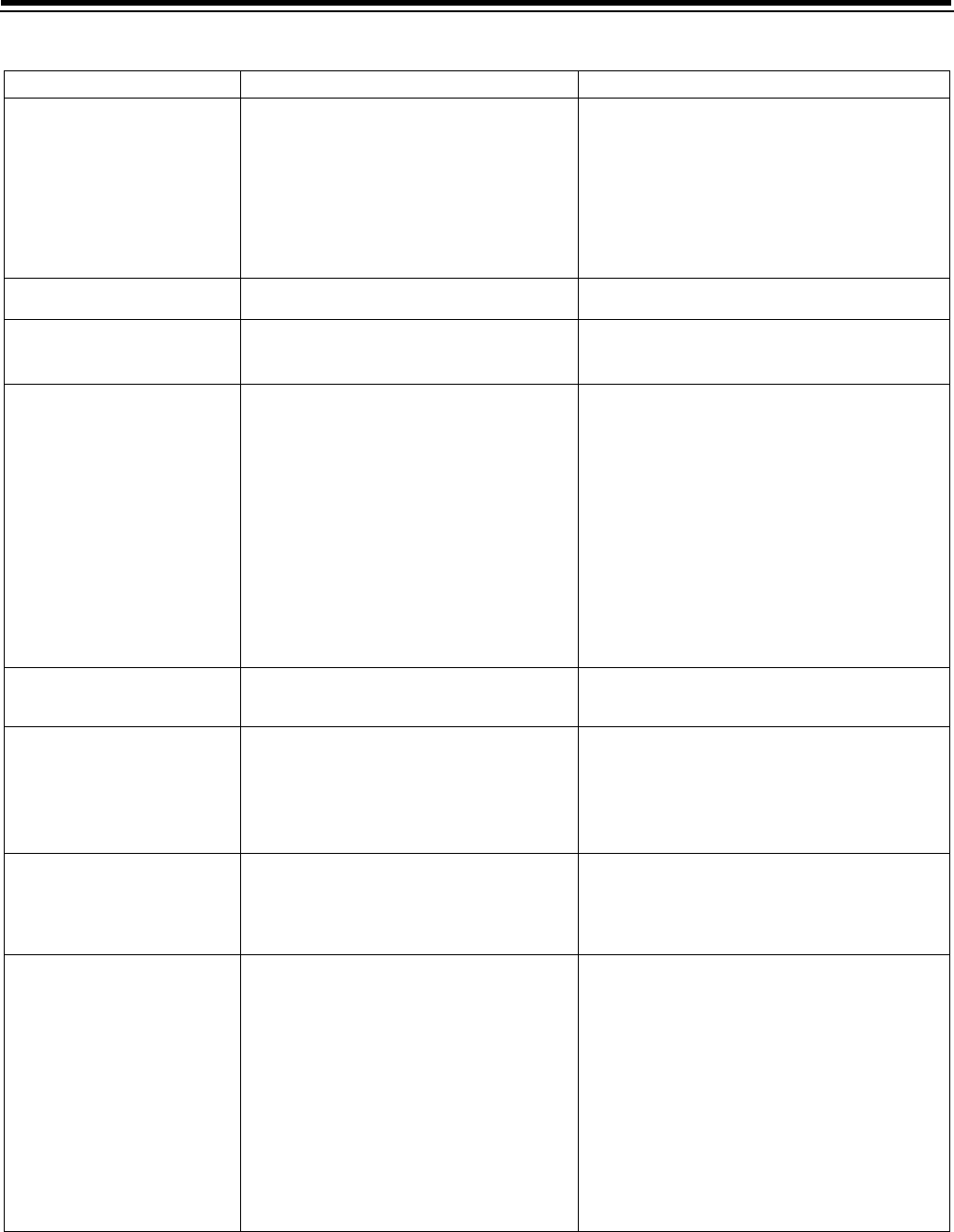
30
Problem Possible Cause Solution
6. No water flow display when
water is flowing (colon does
not blink).
A. Bypass valve in bypass position.
B. Meter probe disconnected or not fully
connected to meter housing.
C. Restricted meter turbine rotation due to
foreign material in meter !
D. Defective meter probe.
E. Defective circuit board.
A. Shift bypass valve into service position.
B. Fully insert probe into meter housing.
C. Remove meter housing, free up turbine and flush
with clean water. Turbine should spin freely. If not,
refer to the Water Meter Maintenance section.
D. Replace control.
E. Replace control.
7. Control display is frozen at
Regen Time Remaining.
A. Back to back regenerations were requested. A. Refer to the Manual Regeneration section.
8. Control regenerates at the
wrong time of day.
A. Power outages.
B. Time of day set incorrectly.
C. Time of regeneration set incorrectly.
A. Reset time of day to correct time of day.
B. Reset time of day to correct time of day.
C. Reset time of regeneration.
9. Timer stalled in regeneration
cycle.
A. Motor not operating.
B. Motor runs backwards.
C. No electric power at outlet.
D. Incorrect voltage or frequency (Hz).
E. Broken gear.
F. Defective switch.
G. Air leak in regenerant connections (pressure
locked flapper).
H. Binding of camshaft.
I. Water pressure greater than 125 psi during
regeneration.
J. Defective circuit board.
A. Replace control.
B. Replace control.
C. Repair outlet or use working outlet.
D. Replace timer and/or transformer with one of
correct voltage and frequency (Hz).
E. Replace control.
F. Replace control.
G. Check all junction points and make appropriate
corrections.
H. Remove foreign object obstruction from valve
discs or camshaft.
I. Install pressure regulator to reduce pressure.
J. Replace control.
10. Continuous regeneration.
Camshaft does not stop at the
end of regeneration.
A. Broken projection on drive gear.
B. Defective switch.
A. Replace control.
B. Replace control.
11. Control does not regenerate
automatically or when REGEN
button is depressed.
A. Transformer unplugged.
B. No electric power at outlet.
C. Defective motor.
D. Broken gear.
E. Binding in gear train.
F. Defective switch.
A. Connect power.
B. Repair outlet or use working outlet.
C. Replace control.
D. Replace control.
E. Replace control.
F. Replace control.
12. Control does not regenerate
automatically but does
regenerate when REGEN
button is depressed.
A. If water flow display is not operative, refer to
item 5 in this table.
B. Incorrect hardness and capacity settings.
C. Defective circuit board.
A. Refer to item 5 in this table.
B. Set new control values. Refer to the Programming
section.
C. Replace control.
13. Run out of soft water between
regenerations.
A. Improper regeneration.
B. Fouled resin bed.
C. Incorrect salt setting.
D. Incorrect hardness or capacity settings.
E. Water hardness has increased.
F. Restricted meter turbine rotation due to
foreign material in meter housing !
G. Excessive water usage below 1/5 gallon per
minute.
A. Repeat regeneration making certain that correct
salt dosage is used.
B. Use resin cleaner.
C. Set salt control to proper level. Refer to the
Programming section in this manual.
D. Set to correct values. Refer to the Programming
section in this manual.
E. Set to new value. Refer to the Programming
section in this manual.
F. Remove meter housing, free up turbine, and flush
with clean water. Turbine should spin freely, if not,
replace meter.
G. Repair leaky plumbing and/or fixtures.