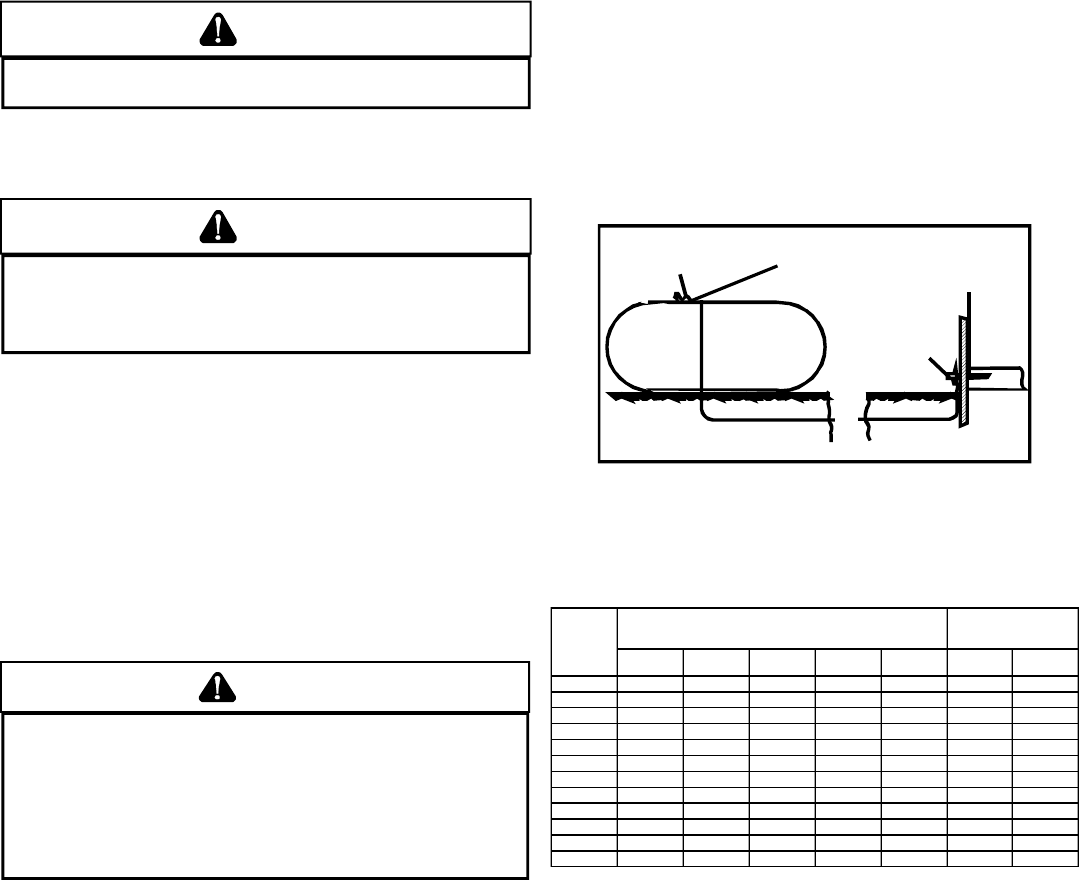
20
IO-242C 05/05
COUNTERFLOW I NSTALLATIONS
When the gas piping enters through the left side of the furnace,
the installer must supply a straight pipe to reach the exterior of the
furnace.
A ground joint union, drip leg, and manual shutoff valve must also
be supplied by the installer. In some cases, the installer may also
need to supply a transition piece from 1/2" to another pipe size.
When the gas piping enters through the right side of the furnace,
the installer must supply the following fittings (starting at the gas
valve):
• 90 degree elbow.
• Close nipple.
• 90 degree elbow.
• Straight pipe to reach exterior of furnace.
GAS PIPING CHECKS
Before placing unit in operation, leak test the unit and gas
connections.
WARNING
T
O AVOID THE POSSIBILITY OF EXPLOSION OR FIRE, NEVER USE A MATCH OR
OPEN FLAME TO TEST FOR LEAKS.
Check for leaks using an approved chloride-free soap and water
solution, an electronic combustible gas detector, or other approved
testing methods.
CAUTION
T
O PREVENT PROPERTY DAMAGE OR PERSONAL INJURY DUE TO FIRE, THE
FOLLOWING INSTRUCTIONS MUST BE PERFORMED REGARDING GAS
CONNECTIONS, PRESSURE TESTING, LOCATION OF SHUTOFF VALVE AND
INSTALLATION OF GAS PIPING.
NOTE: Never exceed specified pressures for testing. Higher
pressure may damage the gas valve and cause subsequent
overfiring, resulting in heat exchanger failure.
Disconnect this unit and shutoff valve from the gas supply piping
system before pressure testing the supply piping system with
pressures in excess of 1/2 psig (3.48 kPa).
This unit must be isolated from the gas supply system by closing
its manual shutoff valve before pressure testing of gas supply
piping system with test pressures equal to or less than 1/2 psig
(3.48 kPa).
PROPANE GAS TANKS AND PIPING
WARNING
IF THE GAS FURNACE IS INSTALLED IN A BASEMENT, AN EXCAVATED
AREA OR A CONFINED SPACE, IT IS STRONGLY RECOMMENDED TO
CONTACT A PROPANE SUPPLIER TO INSTALL A GAS DETECTING
WARNING DEVICE IN CASE OF A GAS LEAK.
•
S
INCE PROPANE GAS IS HEAVIER THAN AIR, ANY LEAKING GAS CAN
SETTLE IN ANY LOW AREAS OR CONFINED SPACES.
•
P
ROPANE GAS ODORANT MAY FADE, MAKING THE GAS UNDETECTABLE
EXCEPT WITH A WARNING DEVICE.
A gas detecting warning system is the only reliable way to detect a
propane gas leak. Rust can reduce the level of odorant in propane
gas. Do not rely on your sense of smell. Contact a local propane
gas supplier about installing a gas detecting warning system. If
the presence of gas is suspected, follow the instructions on Page
4 of this manual.
All propane gas equipment must conform to the safety standards
of the National Board of Fire Underwriters, NBFU Manual 58.
For satisfactory operation, propane gas pressure must be 11 inch
WC at the furnace manifold with all gas appliances in operation.
Maintaining proper gas pressure depends on three main factors:
1. Vaporization rate, depending on temperature of the liquid,
and “wetted surface” area of the container or containers.
2. Proper pressure regulation. (Two-stage regulation is
recommended for both cost and efficiency).
3. Pressure drop in lines between regulators, and between
second stage regulator and the appliance. Pipe size will
depend on length of pipe run and total load of all
appliances.
Complete information regarding tank sizing for vaporization,
recommended regulator settings, and pipe sizing is available
from most regulator manufacturers and propane gas suppliers.
Since propane gas will quickly dissolve white lead and most
standard commercial compounds, special pipe dope must be
used. Shellac-based compounds resistant to the actions of
liquefied petroleum gases such as Gasolac
®
, Stalactic
®
, Clyde’s
®
or John Crane
®
are satisfactory.
Refer to the following illustration for typical propane gas
installations and piping.
200 PSIG
Maximum
5 to 15 PSIG
(20 PSIG Max.)
Continuous
11" W.C.
Second Stage
Regulator
First Stage
Regulator
Propane Gas Installation (Typ.)
PROPANE GAS PIPING CHARTS
3/8" 1/2" 5/8" 3/4" 7/8" 1/2" 3/4"
10 730 1,700 3,200 5,300 8,300 3,200 7,500
20 500 1,100 2,200 3,700 5,800 2,200 4,200
30 400 920 2,000 2,900 4,700 1,800 4,000
40 370 850 1,700 2,700 4,100 1,600 3,700
50 330 770 1,500 2,400 3,700 1,500 3,400
60 300 700 1,300 2,200 3,300 1,300 310
80 260 610 1,200 1,900 2,900 1,200 2,600
100 220 540 1,000 1,700 2,600 1,000 2,300
125 200 490 900 1,400 2,300 900 2,100
150 190 430 830 1,300 2,100 830 1,900
175 170 400 780 1,200 1,900 770 1,700
200 160 380 730 1,100 1,800 720 1,500
Sizing Between First and Second Stage Regulator*
Maximum Propane Capacities listed are based on 2 psig pressure drop at 10 psig setting.
Capacities in 1,000 BTU/hour.
Nominal Pipe Size
Schedule 40
Tubing Size, O.D. Type L
Pipe or
Tubing
Length,
Feet