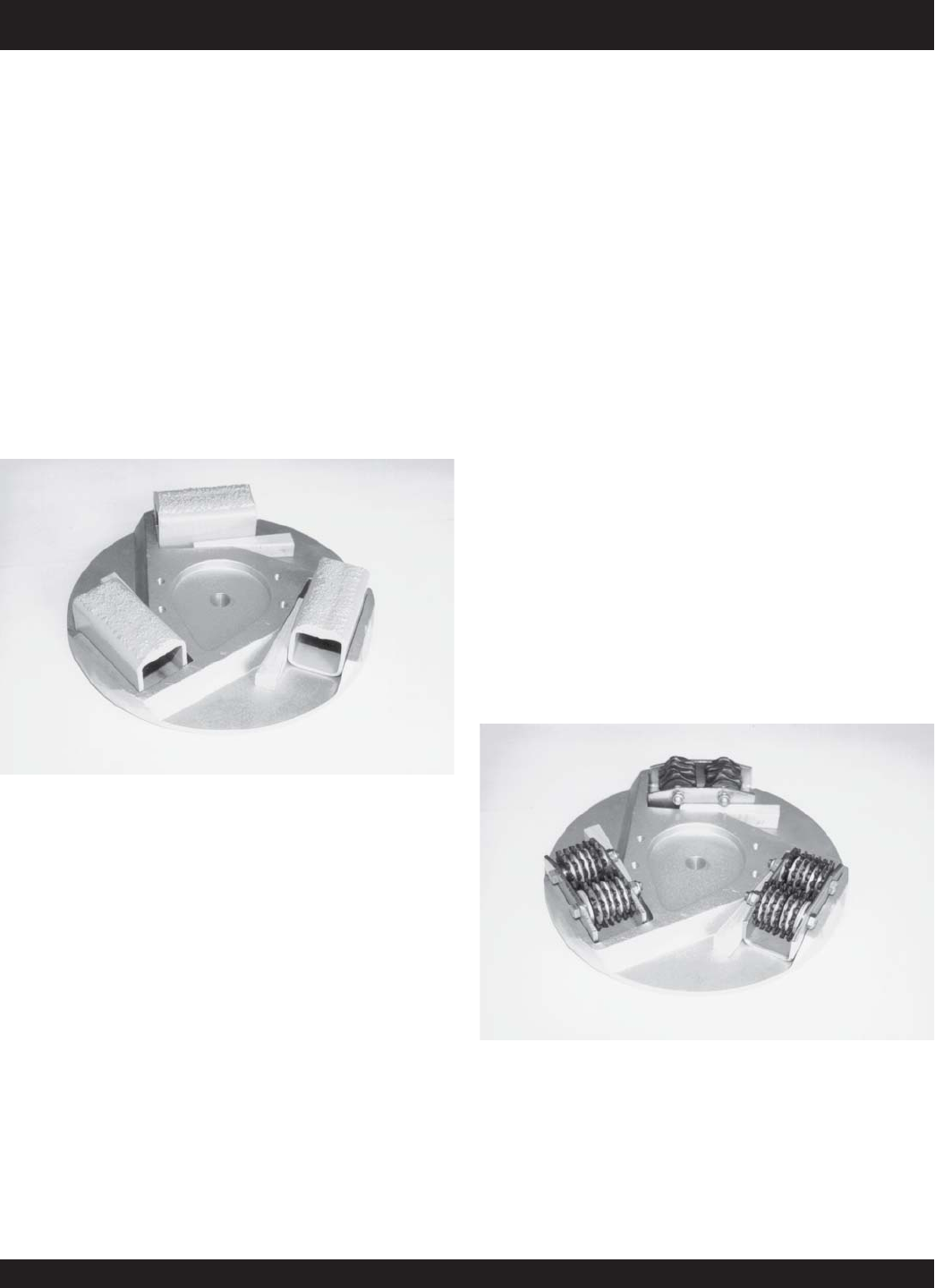
SFG10E ELECTRIC SURFACE GRINDER — OPERATION AND PARTS MANUAL — REV. #1 (07/16/07) — PAGE 14
insert flails. In turn, these costs must be compared to
anticipated service life. All flails will eventually wear to the
point of requiring replacement. The amount of unproductive
time spent to replace worn flails on a job can be substantially
greater than the actual replacement cost of many flails. It
then becomes a balance between purchase cost,
productivity, service life and labor cost.
c) Surface finish and texture. The finest grained surface
finish available from the scarifying process is comparable
to a “swept or broomed” like finish. If a smooth, flat finish is
desired, the scarifying process must be followed with a
grinding or polishing type process. Many job requirements
may call for large amounts of material to be removed, but
followed with additional specifications requiring a finer
surface finish or texture. Many times these jobs dictate the
use of an aggressive flail configuration because of
productivity and cost considerations. Less aggressive flail
configurations can then be utilized for the final finishing
sequence. Generally speaking, the more aggressive the flail
configurations, the more coarse the resulting finish and
texture.
Many flail configurations are available to meet a wide variety
of job applications and surface material specifications. To
give additional perspective to each configuration, a rating
system of 1 to 10 (10 being highest) has been devised.
FIGURE 6
Star Flail
The star flail is manufactured from high carbon steel that is
through hardened for additional service life. It is highly
effective for light cleaning or scarifying and delivers a finer
surface finish texture. FIGURE 7.
ASSEMBLY INSTRUCTIONS/OPERATIONS
Tungsten Carbide Grinding Block
This multi-accessory attachment is most often utilized on
larger concrete grinding projects where increased production
and service life are required. The block utilizes tungsten
carbide balls approximately 1/16 inch diameter that are
deposited in a molten matrix material during the
manufacturing process at a controlled rate. The end effect
is a multi layer deposit of tungsten carbide balls in the matrix
material. As the softer matrix material wears with use, it
exposes a new layer of fresh tungsten carbide balls to
continue the grinding process. The tungsten carbide grinding
block is considerably more aggressive than the C10 silicon
carbide grinding stone. With the ability to renew itself during
usage, the normal life expectancy for this accessory can
approach several hundred hours. The nominal dimensions for
the tungsten carbide grinding block is 2" x 2" x 4" and is secured
to the machine with a plastic wedge. FIGURE 5.
FIGURE 5
Scarifier Blocks
These multi-accessory attachments are comprised of flails
and spacer washers secured in a rigid steel case. FIGURE
6. Rotation of the multi-accessory disc causes the flails to
impact against the work surface with a variety of results.
Scarifier blocks are secured to the machine with plastic
wedges.
Several factors directly affect the selection of a flail design
for a specific job application:
a) The type and amount of material to be removed from the
work surface. Materials of higher yield and tensile strengths
along with the actual volume of material to be removed will
generally be the first factors under consideration.
b) Purchase cost versus service life. The original purchase
cost of plain, heat-treated steel flails must be compared
against the substantially higher costs of the tungsten carbide