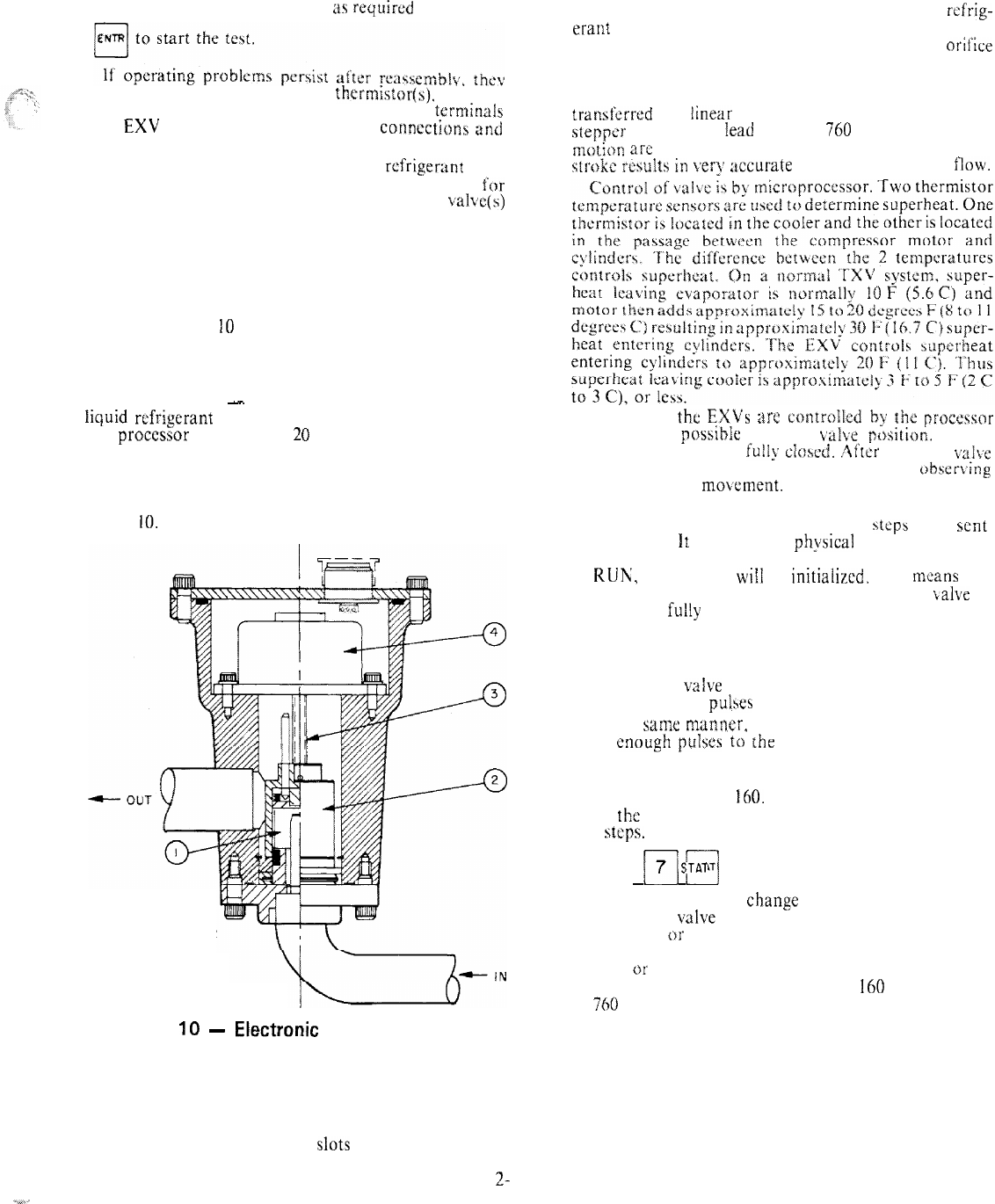
The EXV test can be repeated
r-rs
required by pressing
may be due to out-of-calibration thcrmistorfs), or inter-
mittent connections between processor board tcrn?inals
and EXV plug. Recheck all wiring connections
;tnd
voltage signals.
Other possible causes of improper refrigerant flow
control could be restrictions in liquid line. Check
i‘or
plugged filter drier(s), stuck liquid line solenoid
valve(s)
or restricted metering slots in the EXV. Formation of ice
or frost on lower body of electronic expansion valve is
one symptom of restricted metering slots. Clean or
replace valve if necessary.
NOTE: Frosting of valve is normal during compressor
Quick Test steps and at initial start-up. Frost should
dissipate after 5 to
10
minutes operation of a system that is
operating properly. If valve is to be replaced, wrap valve
with a wet cloth to prevent excessive heat from damaging
internal components.
EXV OPERATION
-
These valves control the flow of
liquid refrigerant into the cooler. They are operated by
the
processor
to maintain
20
degrees F of superheat
between the cooler entering refrigerant thermistor and the
lead compressor entering gas thermistor (located between
the compressor motor and the cylinders). There is one
EXV per circuit. A cutaway drawing of valve is shown
in Fig.
IO.
4 -STEPPER MOTOR
3 -LEAD SCREW
2 -PISTON
1 -ORIFICE ASSEMBLY
Fig. 10
-
Electronic Expansion Valve
High-pressure liquid refrigerant enters valve through
bottom. A series of calibrated
slots
have been machined
in side of orifice assembly. As refrigerant passes through
orifice, pressure drops and refrigerant changes to a 2-
phase condition (liquid and vapor). To control refrlg-
erant flow for different operating conditions, piston
moves up and down over orifice, thereby changing orifice
size. Piston is moved by a linear stepper motor. Stepper
motor moves in increments and is controlled directly by
processor module. As stepper motor rotates, motion is
transferred into linear movement by lead screw. Through
stepper
motor and
lead
screws, 760 discrete steps of
n~otjc‘rn
arc obtained. The large number of steps and long
st~‘cdkt’
r*csults
in very itccurate control of refrigerant flow.
Because
tht:
EXVs
art:
wntmEItd
hy
rtw
processor
module, it is possible to track
vaIvc
pr>sition.
During
initial start-up, EXV is fully
cloxcd.
After
start-up,
v;rIkc
position is tracked by processor by constantly
thsct-ving
amount of valve movement.
The processor keeps track of the EXV position by
counting the number of open and closed
steps
it has
sent
to each valve.
II
has no direct
phvsical
feedback of valve
position. Whenever the unit is switched from STANDBY
to
RUIN,
both valves will be initialized. This
means
the
processor will send enough closing pulses to the
\,alve
to
move it from fully open to fully closed and then reset the
position counter to zero.
The EXV open Quick Tests will send enough pulses to
the valve to drive it from fully closed to fully open. The
position of the
valve
at the start of the test has no effect
on the number of
puI$cs
sent.
In the same manner, the EXV close Quick Tests will
send
enough
pulses
tr,
rhe
valve to drive it from fully
open to fully closed,
When the EXV opens, the metering slots are not
uncovered until step
160.
This is fully closed position
when
the
circuit is operating. The fully open position is
760
steps.
The
m
r]
STAT
subfunction shows the EXV valve
positions. They should
ch,ange
constantly while the unit
operates. If a
vrxlve
should stop moving for any reason
(mechanical
or
electrical) other than a processor or
thermistor failure. the processor will continue to attempt
to open
<)r
close the valve to correct the superheat. Once
the calculated valve position reaches
160
(fully closed)
or 760 (fully open) it will remain there. If the EXV posi-
tion reading remains at 160 or 760 and the cooler and
compressor refrigerant thermistor displays are reading
the measured temperature correctly, the EXV is not
moving. Follow the EXV checkout procedure to deter-
mine the cause.
The EXV is also used to limit cooler suction tem-
perature to 55 F (13 C). This makes it possible for the
chiller to start at higher cooler water temperatures with-
out overloading compressor. This is commonly referred
to as MOP (maximum operating pressure).
21