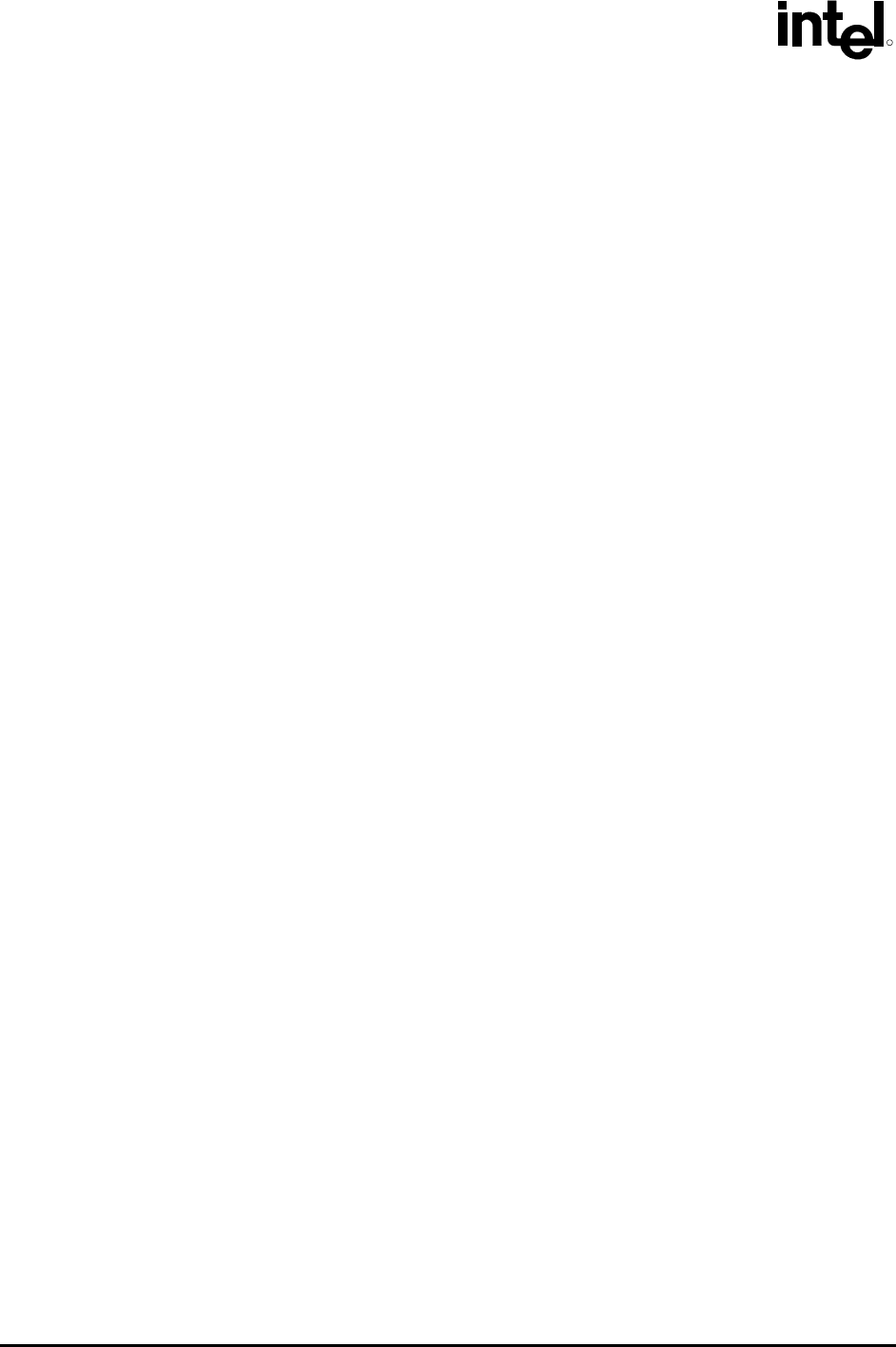
Validation Testing Requirements
R
34 mPGA604 Socket Design Guidelines
6.7 Quality Assurance Requirements
The OEM’s will work with the socket supplier(s) they choose to ensure socket quality.
6.8 Socket Test Plan
6.8.1 Submission of an mPGA604 Socket for Validation Testing
The socket supplier's mPGA604 socket will be sent to Intel's independent test facility for socket
validation testing. The sockets submitted must be per the drawing required in Section 6.4. Refer to
Sections 6.11 and 6.12 for production lot definition and number of samples required for validation
testing.
6.9 Mechanical Samples
A mechanical sample of mPGA604 socket, package, and heatsink (or suitable mockups that
approximate size and mass of the planned heatsink) will be used during the mated socket validation
testing. The maximum mass for mPGA604 socket package heatsink is recommended as (but not
limited to) 450g with the stipulation that the requirements of Section 3.1 be met. See data sheet and
related documentation for further information on heatsinks, thermal solutions and mechanical
support.
6.10 Socket Validation Notification
Upon completion of the testing and receipt of test data, Intel and/or the Intel designated test facility
will prepare a summary report for the socket supplier and Intel that will provide notification as to
whether the socket has passed or failed socket validation testing.
6.11 Production Lot Definition
A production lot is defined as a separate process run through the major operations including
molding, contact stamping, contact plating and assembly. These lots should be produced on separate
shifts or days of the week. Lot identification marking needs to be provided to Intel as verification of
this process.
6.12 Socket Validation
Socket validation must meet or exceed all guidelines called out in this spec which include: Visual
Inspection, CTF Dimensional Verification, Electrical Resistance, Loop Inductance, Pin to Pin
Capacitance, Contact Current Rating, Dielectric Withstand Voltage, Insulation, Durability, Porosity,
Plating Thickness, Solvent Resistance (if applicable), Solderability (Applicable for leaded sockets),
Post Reliability Visual and use conditions. The use conditions target failure rates are <1% at 7 years
and <3% at 10 years. Statistical sample sizes, taken randomly from multiple lots, for each test is
required.