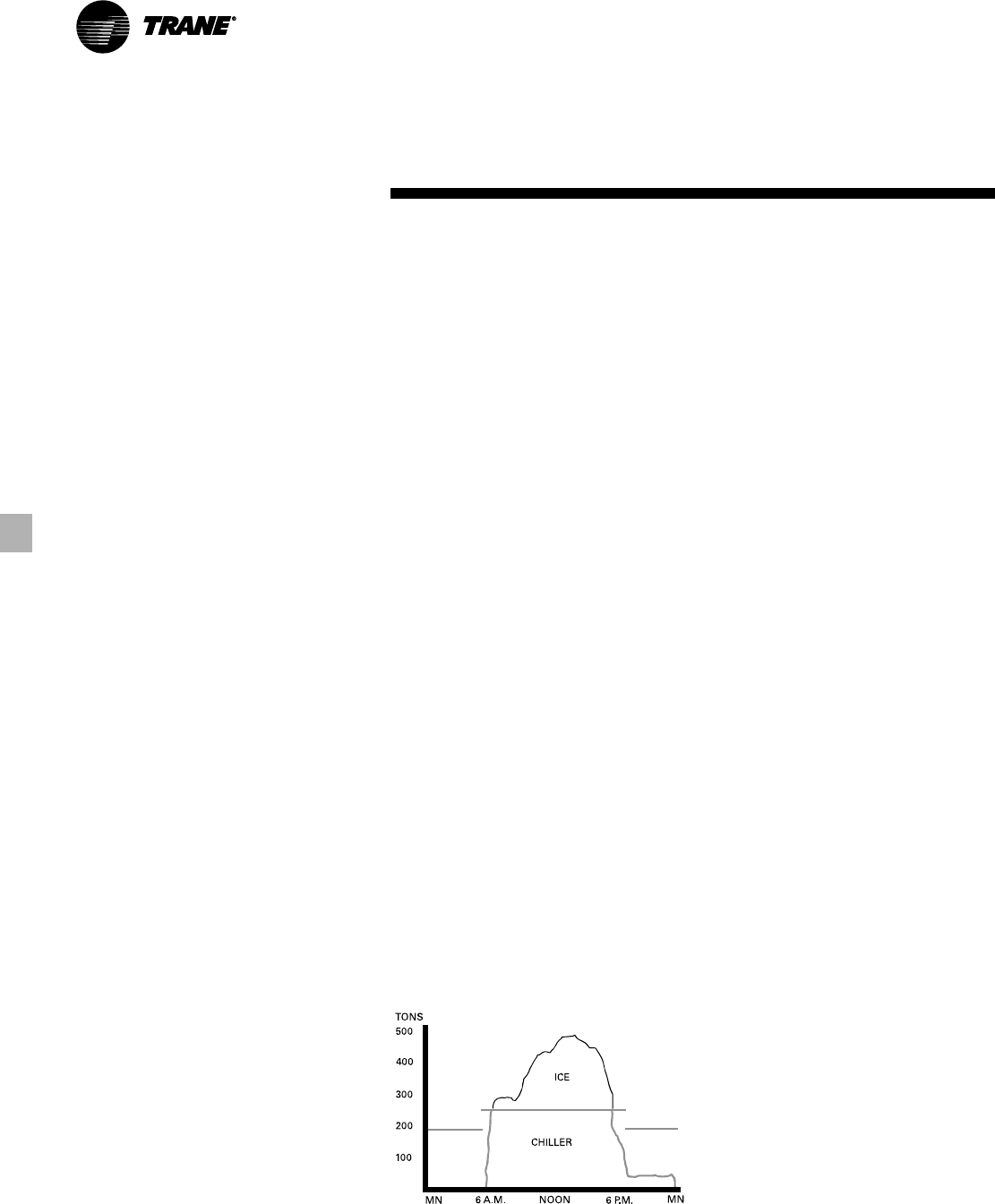
CTV-PRC007-EN22
Ice Storage Provides
Reduced Electrical Demand
Ice storage is the hottest thing in cooling
today. It has been accepted by building
owners and tenants who are concerned
about utility costs.
An ice storage system uses a standard
chiller to make ice at night when utilities
charge less for electricity. The ice
supplements or even replaces
mechanical cooling during the day when
utility rates are at their highest. This
reduced need for cooling results in big
utility cost savings.
Another advantage of ice storage is
standby cooling capacity. If the chiller is
unable to operate, one or two days of ice
may still be available to provide cooling.
In that time the chiller can be repaired
before building occupants feel any loss
of comfort.
The Trane CenTraVac chiller is uniquely
suited to low temperature applications
like ice storage because it provides
multiple stages of compression.
Competitive chillers provide only one
stage. This allows the CenTraVac chiller
to produce ice efficiently, with less stress
on the machine.
Simple and smart control strategies are
another advantage the CenTraVac chiller
has for ice storage applications. Trane
Tracer
™
building management systems
can actually anticipate how much ice
needs to be made at night and operate
the system accordingly. The controls are
integrated right into the chiller. Two
wires and preprogrammed software
dramatically reduce field installation cost
and complex programming.
Trane centrifugal chillers are well suited
for ice production. The unique multi-
stage compressor design allows the
lower suction temperatures required to
produce ice and the higher chiller
efficiencies attributed to centrifugal
chillers. Trane three stage and two stage
centrifugal chillers produce ice by
supplying ice storage vessels with a
constant supply of 22 to 24°F glycol.
Centrifugal chillers selected for these
lower leaving fluid temperatures are also
Ice Storage Demand Cost Savings
Ice Storage
System
Options
selected for efficient production of
chilled fluid at nominal comfort cooling
conditions. The ability of Trane chillers to
serve “double duty” in ice production
and comfort cooling greatly reduces the
capital cost of ice storage systems.
A glycol solution is used to transfer heat
from the ice storage tanks to the
centrifugal chiller and from the cooling
coils to either the chiller or ice storage
tanks. The use of a freeze protected
solution eliminates the design time, field
construction cost, large refrigerant
charges, and leaks associated with ice
plants. Ice is produced by circulating 22-
24°F glycol through modular insulated
ice storage tanks. Each tank contains a
heat exchanger constructed of
polyethylene tubing. Water in each tank
is completely frozen with no need for
agitation. The problems of ice bridging
and air pumps are eliminated.
When cooling is required, ice chilled
glycol is pumped from the ice storage
tanks directly to the cooling coils. No
expensive heat exchanger is required.
The glycol loop is a sealed system,
eliminating expensive annual chemical
treatment costs. The centrifugal chiller is
also available for comfort cooling duty at
nominal cooling conditions and
efficiencies. The modular concept of
glycol ice storage systems and the
proven simplicity of Trane Tracer
™
controls allow the successful blend of
reliability and energy saving
performance in any ice storage
application.
The ice storage system is operated in six
different modes: each optimized for the
utility cost of the hour.
1 Provide comfort cooling with chiller
2 Provide comfort cooling with ice
3 Provide comfort cooling with ice and
chiller
4 Freeze ice storage
5 Freeze ice storage when comfort
cooling is required
6 Off
Tracer optimization software controls
operation of the required equipment and
accessories to easily transition from one
mode of operation to another. For
example:
Even with ice storage systems there are
numerous hours when ice is neither
produced or consumed, but saved. In
this mode the chiller is the sole source of
cooling. For example, to cool the
building after all ice is produced but
before high electrical demand charges
take effect, Tracer sets the centrifugal
chiller leaving fluid setpoint to its most
efficient setting and starts the chiller,
chiller pump, and load pump.
When electrical demand is high, the ice
pump is started and the chiller is either
demand limited or shut down
completely. Tracer controls have the
intelligence to optimally balance the
contribution of ice and chiller in meeting
the cooling load.
The capacity of the chiller plant is
extended by operating the chiller and ice
in tandem. Tracer rations the ice,
augmenting chiller capacity while
reducing cooling costs.
When ice is produced, Tracer will lower
the centrifugal chiller leaving fluid
setpoint and start the chiller, chiller and
ice pumps, and other accessories. Any
incidental loads that persists while
producing ice can be addressed by
starting the load pump and drawing
spent cooling fluid from the ice storage
tanks.
For specific information on ice storage
applications, contact your local Trane
sales office.