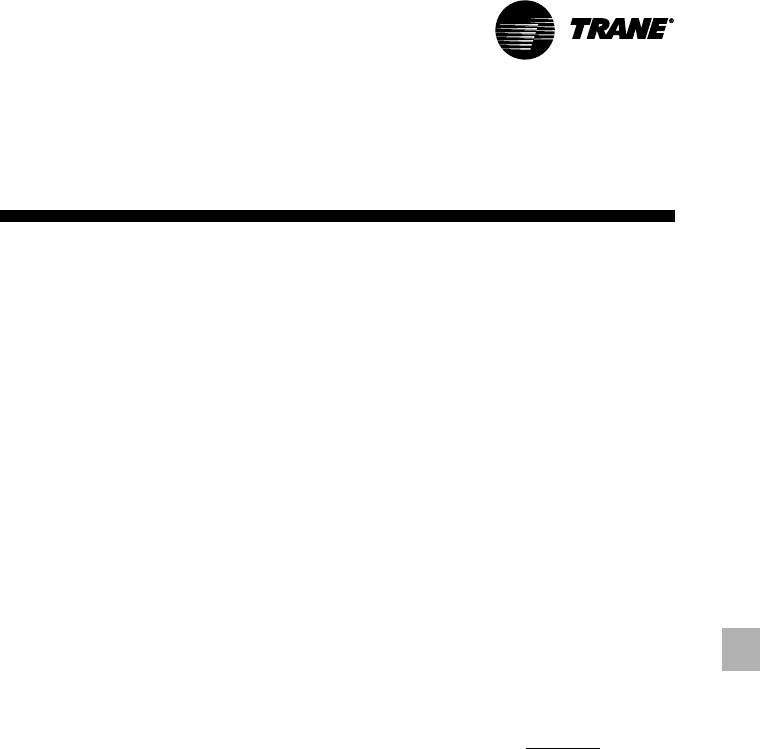
27
CTV-PRC007-EN
Condenser Water Limitations
Trane CenTraVac
™
chillers start and
operate over a range of load conditions
with controlled water temperatures.
Reducing the condenser water
temperature is an effective method of
lowering the chiller power input.
However, the effect of lowering the
condenser water temperature may cause
an increase in system power
consumption.
In many applications Trane CenTraVac
chillers can start and operate without
control of the condenser water
temperature. However, for optimum
system power consumption, and for any
applications with multiple chillers,
control of the condenser water circuit is
recommended. Integrated control of the
chillers, pumps and towers is easily
accomplished with Trane’s UCP2 and/or
Tracer system.
Water Treatment
The use of untreated or improperly
treated water in a chiller may result in
scaling, erosion, corrosion, algae or
slime. It is recommended that the
services of a qualified water treatment
specialist be used to determine what
treatment, if any, is advisable. The Trane
Company assumes no responsibility for
the results of untreated, or improperly
treated water.
Water Pumps
Avoid specifying or using 3600 rpm
condenser and chilled water pumps.
Such pumps may operate with
objectionable noises and vibrations. In
addition, a low frequency beat may occur
due to the slight difference in operating
rpm between water pumps and
CenTraVac motors. Where noise and
vibration-free operation are important,
The Trane Company encourages the use
of 1750 rpm pumps.
Chillers are designed to ARI conditions of
85°F, but Trane CenTraVac chillers can
operate to a 3 psig pressure differential
between the condenser and evaporator
at any steady state load without oil loss,
oil return, motor cooling, refrigerant
hang-up or purge problems. And this
differential can equate to safe minimum
entering condenser water temperatures
at or below 55°F, dependent on a variety
of factors such as load, leaving
evaporator temperature and component
combinations. Start-up below this
differential is possible as well, especially
with UCP2 soft start features
Water Flow
Today’s technology challenges ARI’s
traditional design of three gpm per ton
through the condenser. Reduced
condenser flows are a simple and
effective way to reduce both first and
operating costs for the entire chiller plant.
This design strategy will require more
effort from the chiller. But pump and
tower savings will typically offset any
penalty. This is especially true when the
plant is partially loaded or condenser
relief is available.
In new systems, the benefits can include
dramatic savings with:
•
Size and cost for condenser lines and
valves
•
Size and cost of the cooling tower.
•
Size and cost of the water pumps.
•
Pump energy (30 to 35% reduction).
•
Tower fan energy (30 to 35% reduction).
Replacement chiller plants can reap even
greater benefits from low flow
condensers. Because the water lines and
tower are already in place, reduced flows
would offer a tremendous energy
advantage. Theoretically, a 2 GPM/ton
design applied to a system that originally
used 3 GPM/ton would offer a 70%
reduction in pump energy. At the same
time, the original tower would require a
nozzle change but would then be able to
produce about two degrees colder
condenser water than before. These two
benefits would again typically offset any
extra effort required by the chiller.
Contact your local Trane Sales Office for
information regarding optimum
condenser water temperatures and flow
rates for a specific application.
Electrical Information
Minimum Circuit Ampacity
To properly size field electrical wiring, the
electrical engineer or contractor on a
project needs to know the minimum
circuit ampacity of the CenTraVac
™
machine. The National Electrical Code
(NEC), in Article 440-33, defines the
method of calculating the minimum
circuit ampacity. The minimum circuit
ampacity is defined as the sum of two
amperages: 125 percent of the
compressor motor Rated Load Amps
(RLA), plus the Full Load Amps (FLA) of
all remaining loads on the same circuit.
For starter to motor wiring, there are no
other remaining loads. For main power
supply to the starter, there is a remaining
load consisting of the 4 KVA control
power transformer which supplies power
to the controls, the oil pump motor, oil
sump heater and the purge unit motor.
Therefore, the remaining load FLA
equals 4000 divided by the unit design
voltage.
As an example, calculate the minimum
circuit ampacity of a machine which has
a design RLA of 350 amps and is to be
operated on a 460 volt power supply:
Minimum Circuit Ampacity =
4000 VA
(125% x 350 Amps) +
460 V
= 437.5 Amps + 8.7 Amps
= 446.2 Amps
After the minimum circuit ampacity has
been determined, the electrical engineer
or contractor will refer to the appropriate
conductor sizing table in the NEC to
determine the exact conductors required.
A typical table for 75°F conductors is
included in the Trane submittal. The
selection of conductors is based on a
number of jobsite conditions (i.e. type of
conductor, number of conductors, length
of conductors, ambient temperature
rating of conductors).
Branch-Circuit Short-Circuit and Ground
Fault Protection
Circuit breakers and fused disconnects
should be sized by the electrical engineer
or contractor in strict accordance with
NEC Article 440-21 and in accordance
with all local codes. This protection
should be for motor type loads and
should not be less than 150 percent of
the compressor motor rated load amps
(RLA).
Application
Considerations