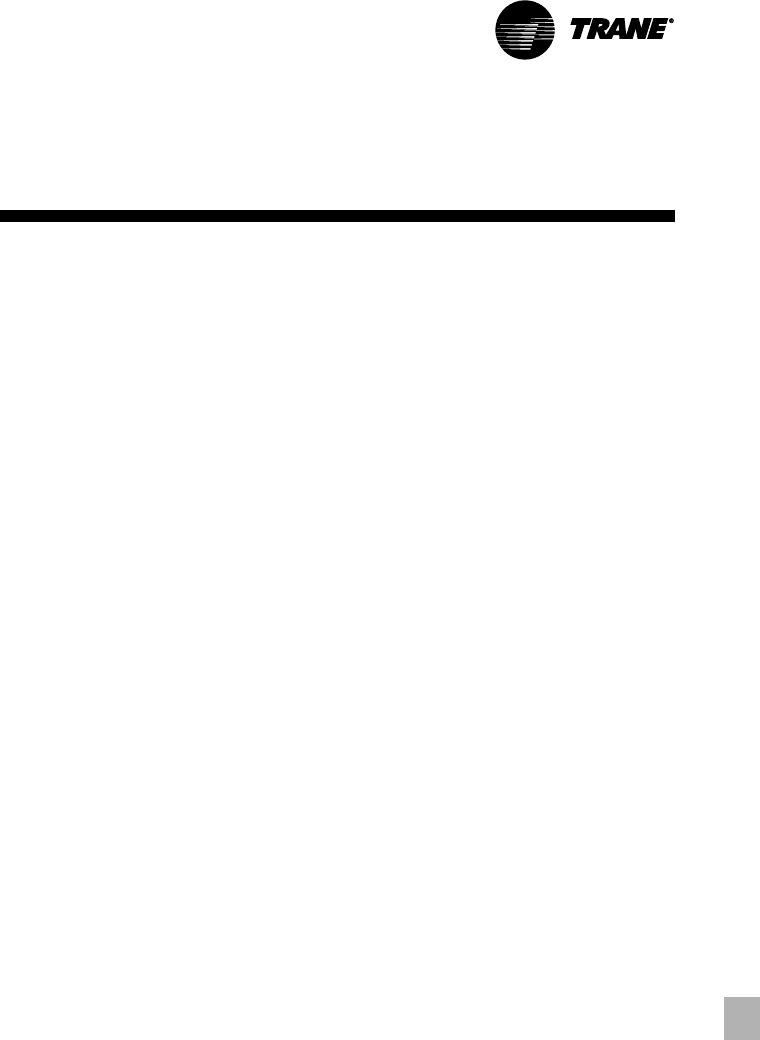
51
CTV-PRC007-EN
Trane Adaptive Frequency
™
Drive (AFD)
The Trane AFD is a closed-loop, liquid-
cooled, microprocessor based PWM
design that converts fixed utility voltage
and frequency to a variable voltage and
frequency via a two-step operation. The
AFD is both voltage and current
regulated. Output power devices: IGBT
transistors.
The AFD is factory mounted on the
chiller and ships completely assembled,
wired and tested.
Patented Trane AFD control logic is
specifically designed to interface with the
centrifugal water chiller controls. AFD
control adapts to the operating ranges
and specific characteristics of the chiller,
and chiller efficiency is optimized by
coordinating compressor motor speed
and compressor inlet guide vane
position. Chilled water control and AFD
control work together to maintain the
chilled water setpoint, improve efficiency
and avoid surge. If a surge is detected,
AFD surge avoidance logic will make
adjustments to move away from and
avoid surge at similar conditions in the
future.
AFD is capable of operating at an altitude
of 3300 feet rated output current. For
every 300 feet above 3300 feet, the rated
output current will be decreased by 1%.
AFD Design Features
•
NEMA 1 ventilated enclosure with a
hinged, locking door and door-
mounted circuit breaker with shunt
trip, is tested to a short circuit
withstand rating of 65,000 amps per UL
508. The entire package is UL/CUL
listed.
•
Digital keypad displays DC bus voltage,
drive output motor current; output
frequency (Hz); RPM; kW; percent
motor torque; and elapsed time. LED’s
also display drive status: running,
remote, jog, auto, forward, reverse or
program.
•
One programmable analog output
signal, (0-10 Vdc or 4-20 mA) for
customer use.
•
Three programmable relay outputs for
customer use.
•
Simple modular construction.
•
The drive is rated for 480/60/3 input
power, +/-10%, with a motor thermal
overload capability of 110%
continuous for 25 minutes to 150% for
60 seconds, linear between 110 and
150.
•
Input displacement power factor will
exceed .96 regardless of speed and load.
•
Minimum efficiency of 97% at rated
load and 60 hertz.
•
Soft-start; linear acceleration/coast to
stop.
•
Standard DC bus filter choke to limit
harmonic distortion.
•
All control circuit voltages are
physically and electrically isolated from
power circuit voltage.
•
150% instantaneous torque available
for improved surge control.
•
Critical frequency avoidance.
•
Output line-to-line and line-to-ground
short circuit protection.
•
Restart into a rotating motor.
•
AFD can be started without a motor
connected.
Mechanical
Specification
Chiller Unit Control Features for AFD
The chiller unit control panel standard
control capabilities provide for the
control/configuration interface to, and
the retrieval/display of the collaterally
additional AFD related data. AFD
standard design features controlled
through the starter module of UCP2
include:
•
Current limited to 100%.
•
Auto restart after an interruption of
power limited to four starts per hour,
30 seconds between starts.
•
Output speed reference signal 2-10
vdc.
•
Digital display on UCP2 panel: output
speed in hertz, output speed in rpm,
fault, amps, input line voltage.
•
Motor overload protection.
•
Loss of follower signal – in the event of
loss of input speed signal the AFD will
default to 38 hertz or hold speed based
on last reference received.
•
Phase loss, reversal, imbalance
protection.
•
Power loss ride through.
•
Overvoltage/undervoltage protection.
•
Motor overtemperature protection.
Environmental ratings:
•
32°F to 104°F (0°C to 40°F) operating
temperature
•
Altitude to 3300 feet (1000 m)
•
Humidity, 95% non-condensing
Input Line Reactor Option
Field installed option mounts on the
input side of the AFD to reduce harmonic
distortion and help meet IEEE-519
guidelines. NEMA 1 enclosure; 5%
impedance.