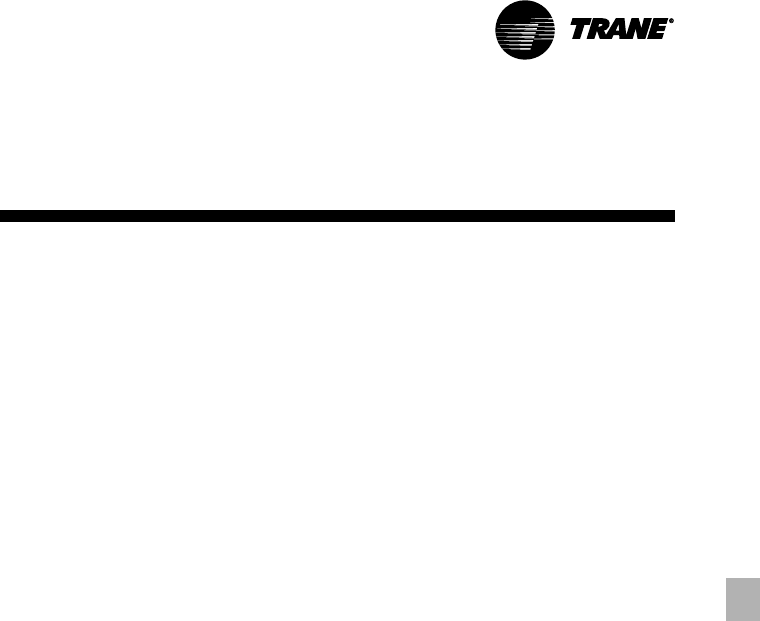
23
CTV-PRC007-EN
Heat Recovery
System
Options
Heat Recovery
Use of the Heat Recovery CenTraVac
™
can significantly reduce the energy
operating costs of many buildings by
using heat which normally would be
rejected to the atmosphere. Typical uses
for this heat are perimeter zone heating,
reheat air conditioning systems and any
hot water requirements. Any building
with a simultaneous heating and cooling
load is a potential candidate.
Most heating applications require water
temperatures higher than the
85°F to 95°F typically sent to the cooling
tower. Therefore, most heat recovery
chillers are required to produce higher
leaving condenser water temperatures,
and thus will not duplicate the energy
efficiencies of cooling-only machines.
Figure O-7 illustrates the typical
operating cycles of a cooling-only
machine and a heat recovery machine.
The most noticeable differences are:
1 The pressure differential provided by
the compressor is much greater for the
heat recovery cycle.
2 The amount of heat rejected from the
heat recovery condenser is greater
than that which would be rejected in
cooling-only operation.
3 There is a decrease in the refrigeration
effect. (RE) Higher condensing
pressures increase the intermediate
pressure in the economizer. Therefore,
the liquid in the economizer has a
higher enthalpy during the heat
recovery mode than during standard
chiller operation and the refrigeration
effect is slightly decreased. Because of
this decreased refrigeration effect, the
compressor must pump more gas per
ton of refrigeration.
The effect of this increased pressure
differential and decreased refrigeration
effect is a heat recovery machine which
has a higher kW/ton energy
consumption during heat recovery
operation.
Typical catalog kW/ton for heat recovery
machines operating in the heat recovery
mode range from .64 to .84 kW/ton
compared to a range of .61 to .79 for a
cooling-only machine. Not only can
there be an energy consumption penalty
paid due to the inherent differences in
operating cycles for heat recovery
machines, but traditional machine
design can add to that energy handicap.
In the past, a heat recovery machine’s
operating efficiency was normally
penalized year- round by having the
capability to produce high heating water
temperatures. Impellers are selected to
produce the maximum required
refrigerant pressure difference between
the evaporator and condenser,
Figure O-8. Usually, that meant the
impeller diameters were determined by
the heat recovery operating conditions.
During cooling-only operation, the
condensing pressures and temperatures
are normally lower than during the heat
recovery operation. So, in essence, the
impeller diameters were oversized. This
would result in a compressor efficiency
during cooling- only season which was
lower than if the impellers had been
selected for a cooling-only application.
The multi-stage compressor and
advanced impeller design on the
CenTraVac
™
chiller reduce this costly
energy penalty. Neither the capacity nor
the power consumption changes
substantially as the heat recovery
operating conditions divert from the
cooling-only condition. The multi-stage
compressor allows a closer match of
impeller size to the operating condition.
In addition, the computer designed
impellers and crossover are designed to
reduce losses as the kinetic energy of the
refrigerant gas is converted to static
pressure.
These advances make the Trane Heat
Recovery CenTraVac
™
chillers even more
attractive now than in the past.
•
The CenTraVac heat recovery chiller
was designed for efficient operation
with kW/ton efficiencies among the
best in the industry for heat recovery
chillers.
•
The energy penalty paid in the past to
operate a heat recovery machine in the
cooling-only mode is essentially
eliminated.