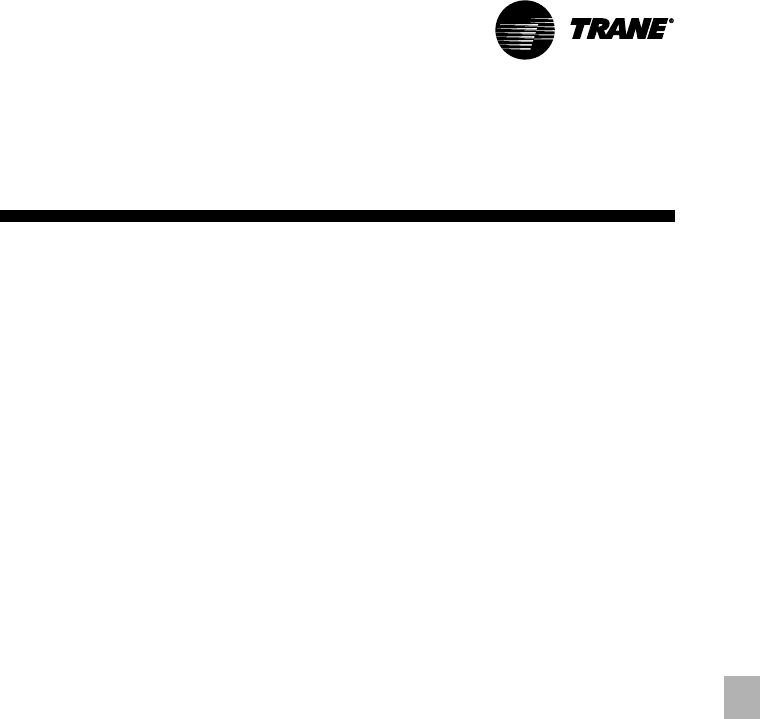
29
CTV-PRC007-EN
Roughing-in Dimensions
The dimensional drawings illustrate
overall measurements of the chiller. The
recommended space envelope indicates
clearances required to easily service the
CenTraVac chiller. A view of the unit is
superimposed on this drawing with unit
support feet shown.
All catalog dimensional drawings are
subject to change. Current submittal
drawings should be referred to for
detailed dimensional information.
Contact the local Trane sales office for
submittal and template information.
Evaporator and Condenser
Data Tables
Evaporator and condenser data is shown
in the Performance Data section. Data
includes minimum and maximum water
flow limits and water connection sizes for
all standard pass configurations and tube
type. Pressure drops are calculated by
the CenTraVac computer selection
program.
Part Load Performance
The CenTraVac chiller possesses
excellent performance characteristics
over its full range of operation. The
multi-stage direct drive compressor
enables stable and efficient operation
over a wide range of capacities, virtually
eliminating the need for energy wasting
hot gas bypass typically found on single
stage chillers.
An in-depth examination of project-
specific conditions and energy rate
structures should be performed to
appropriately evaluate total energy costs
over a period of time. TRACE
™
, Trane’s
unique energy analysis program, is
particularly well suited for this type of
analysis, as well as for economic
evaluation of equipment and system
alternatives.
Local utilities may offer substantial
monetary rebates for centrifugal chillers
with specific operating kW ratings.
Contact your local utility representative
or Trane sales office for further
information.
The electrical rate structure is a key
component of an economic evaluation.
Most power bills are now constituted of
1/3 demand charge and 2/3 usage
charge. The full load power
consumption of the chiller plant is likely
to set the kW peak and demand charge
for the billing period. This places an
increased emphasis on the need to keep
the full load consumption of the chiller
plant low.
There are a number of variables that
should be considered in developing an
accurate chiller load profile to use for
measuring how one machine compares
with another machine at part load. The
use of outdoor air economizers,
variations in chiller sequencing and
chiller plant load optimization strategies
should be considered. The use of a
decoupled or primary/secondary water
loop is generally acknowledged as the
simplest, most efficient way to control
multiple chiller water plants. This control
strategy results in one chiller operating
at a more fully loaded condition rather
than multiple chillers operating at part
load, which would require more
pumping energy.
ARI Standard 550/590 provides chiller
performance certification for the full load
condition and the “NPLV” (non-standard
part load value). The NPLV uses a
generic weighted chiller load profile to
simplify certification of part load
performance data. Although these
values are not necessarily a precise
indicator of actual energy use, they do
provide a valuable basis for comparison.
Selection
Procedure