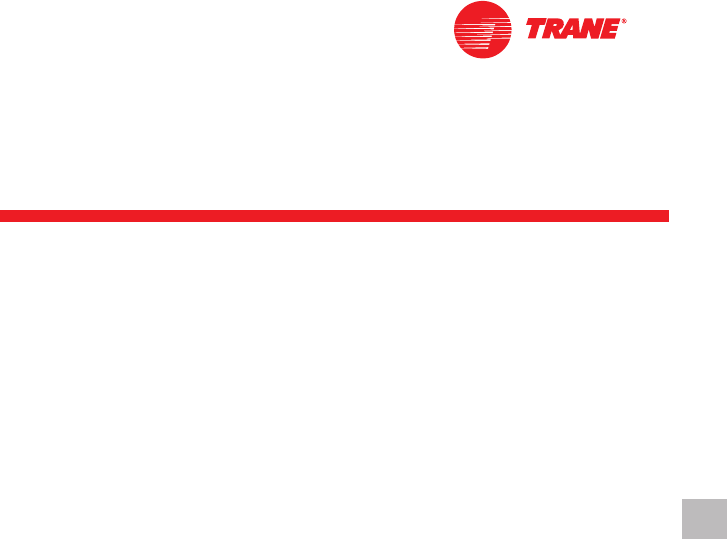
Application Considerations
11
RLC-PRC005-E4
Variable Flow in the Evaporator
An attractive chilled-water system
option may be a variable primary flow
(VPF) system. VPF systems present
building owners with several cost-
saving benefits that are directly related
to the pumps. The most obvious cost
savings result from eliminating the
secondary distribution pump, which in
turn avoids the expense incurred with
the associated piping connections
(material, labor), electrical service, and
variable-frequency drive. Building
owners often cite pump-related energy
savings as the reason that prompted
them to install a VPF system. With the
help of a software analysis tool such as
System Analyzer
™
, TRACE
™
, or DOE-2,
you can determine whether the
anticipated energy savings justify the
use of variable primary flow in a
particular application. It may also be
easier to apply variable primary flow in
an existing chilled-water plant. Unlike
the “decoupled” design, the bypass can
be positioned at various points in the
chilled-water loop and an additional
pump is unnecessary. The evaporator in
the Model RTAC can withstand up to 50
percent water flow reduction as long as
this flow is equal to or above the
minimum flow-rate requirements. The
microprocessor and capacity control
algorithms are designed to take a
minimum of 10 percent change in water
flow rate per minute.
Short Water Loops
The proper location of the temperature
control sensor is in the supply (outlet)
water connection or pipe. This location
allows the building to act as a buffer and
assures a slowly-changing return-water
temperature. If there is not a sufficient
volume of water in the system to
provide an adequate buffer, temperature
control can be lost, resulting in erratic
system operation and excessive
compressor cycling. A short water loop
has the same effect as attempting to
control using the building return water.
Typically, a two-minute water loop is
sufficient to prevent a short water loop.
Therefore, as a guideline, ensure that
the volume of water in the evaporator
loop equals or exceeds two times the
evaporator flow rate. For a rapidly
changing load profile, the amount of
volume should be increased. To prevent
the effect of a short water loop, the
following item should be given careful
consideration: a storage tank or larger
header pipe to increase the volume of
water in the system and, therefore,
reduce the rate of change of the return
water temperature.
Applications Types
• Comfort cooling
• Industrial process cooling
• Ice or thermal storage
• Low-temperature process cooling.
Ice Storage Provides
Reduced Electrical Demand
An ice-storage system uses a standard
chiller to make ice at night, when utilities
charge less for electricity. The ice
supplements, or even replaces,
mechanical cooling during the day,
when utility rates are at their highest.
This reduced need for cooling results in
big utility cost savings.
Another advantage of ice storage is
standby cooling capacity. If the chiller is
unable to operate, one or two days of
ice may still be available to provide
cooling. In that period of time, the chiller
can be repaired before building
occupants feel any loss of comfort.
The Trane Model RTAC chiller is uniquely
suited to low-temperature applications
like ice storage because of the ambient
relief experienced at night. This allows
the Model RTAC chiller to produce ice
efficiently, with less stress on the
machine.
Simple and smart control strategies are
another advantage the Model RTAC
chiller offers for ice-storage applications.
Trane Tracer
™
building management
systems can actually anticipate how
much ice needs to be made at night,
and operate the system accordingly. The
controls are integrated right into the
chiller. Two wires and preprogrammed
software dramatically reduce field
installation cost and complex
programming.