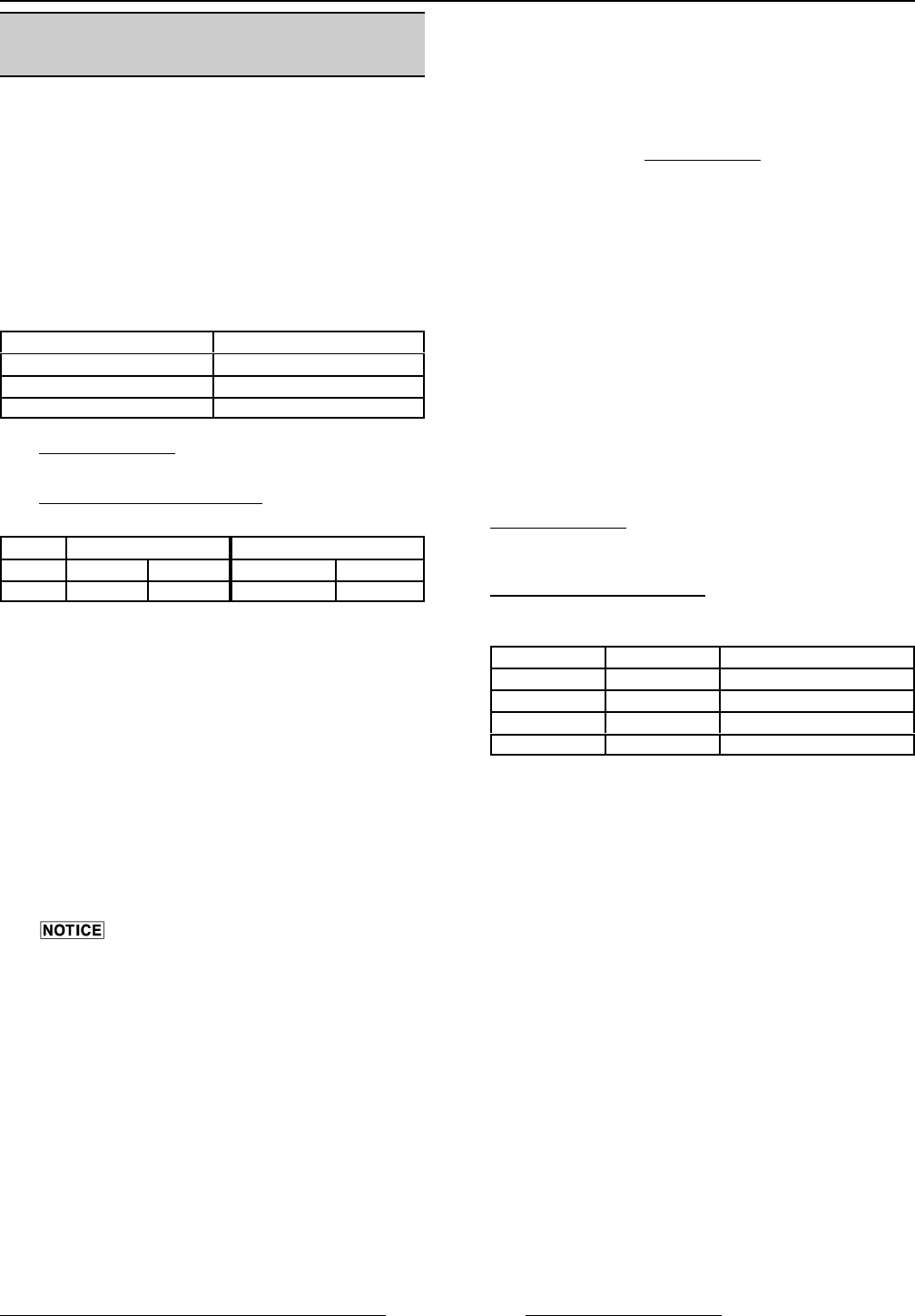
OV500 SERIES RACK OVEN - GENERAL
OV500G2 GAS OVEN
SPECIFICATIONS
â WATER:
1/2" NPT, 30-75 PSI cold water required, customer to
install in-line filter, shut off valve and line strainer.
Ï DRAIN:
2 3/4" (front) or 5 1/2" (rear) connection A.F.F. (See
notes). Route to air-gap drain. Do not slope drain
upwards. Plug the drain connection that is not in use.
Kit provided to extend drain to either side of oven.
Rear Drain: 3/4" NPTF
Front Drain: 3/8" NPTF
Ð POWER:
Two supplies required.
120/60/1 20 AMP dedicated circuit required and one
of the following voltage options.
Voltage Full Load AMPS
208 - 240/60/1 8.8 - 7.6 AMPS
208-240/60/3 5.0 - 4.4 AMPS
440 - 480/60/3 2.4 - 2.2 AMPS
Ñ GAS:
Natural Gas (N.G.)
1 1/4" NPT, W.C.N.G. (N.G. rated 1025 BTU/CU.
FT. SP. GR. 1.00)
Liquified Propane Gas (L.P.G.)
1 1/4" NPT, W.C.L.P.G. (L.P.G. rated 2440
BTU/CU.FT., SP. GR. 1.52)
Natural Gas Liquified Propane Gas
BTU/HR 300,000 350,000 300,000 350,000
W.C. 5.0 -14.0" 6.0 - 14.0" 10.0" - 14.0" 12.0 - 14.0"
Ò HOOD VENT:
10" DIA connection collar. Air proving switch factory
installed & integrated with burner system operation.
Oven provided rely with max. 10 amp 1/2 H.P. @
120V output for fan operation. If larger, use oven
relay to control additional separately powered
contactor / relay for hood fan. Customer to supply
duct and ventilator fan per state and local codes.
Chamber vents are factory ducted to this integral
hood. 900 CFM required, 0.6" W.C. static pressure
drop through hood. Hood is UL710 Listed when
grease filters are installed. Type B gas vent can be
used except when bake products are grease laden.
NOTES:
1. A.F.F.: Above finished floor.
2. Customer responsible to finish and install all utilities
to and from oven.
3. All services must comply with all Federal, State and
Local codes.
4. To reduce the risk of fire, the appliance is
to be installed on non-combustible surface only, with
no combustible material within 18 inches above the
appliance. The appliance is to be mounted on floors
of non-combustible construction with non-
combustible flooring and surface finish and with no
combustible material against the underside, or on
non-combustible slabs or arches having no
combustible material against the underside. Such
construction shall in all cases extend not less than 12
inches beyond the equipment on all sides.
5. The floor must be of non-combustible material, and
must be level with surrounding area with a maximum
slope of 1/8" per foot up to 3/4" maximum in all
directions. Floor anchors require a minimum 1" thick
solid floor substrate.
6. Oven is UL/C-UL classified and CSA (AGA/CGA)
approved for 0" clearance on the side and rear walls.
Unit requires 1" to 4" clearance for rear drain
connection.
7. Top of oven requires a minimum of 24" for service
accessibility.
8. Customer responsible to install flue piping. Flue must
be vented outside of building.
9. Manufacturer reserves the right to make changes in
sizes and specifications.
Export Ratings
â WATER:
1/2” NPT, 2.1-5.2 Bar cold water required, customer
to install in-line filter, shut off valve and line strainer.
Flow rate of 8 l/min..
Ð POWER:
Single supply connection provided: 200V/50-
60Hz/3ph/5.3A or 380-415V/50Hz/3ph/ 2.8 - 2.5A
circuit required.
1 kVA transformer supplied for control circuit
operation voltage of 110V. This is a multifunction
transformer, so output voltage should be verified
before operation. Some wiring may be required to
obtain proper output voltage.
Oven fan (1.1kW) operates @ 380-415V 3ph 50 Hz
2.4- 2.2A
Ñ GAS:
Natural Gas (N.G.)
3/4” NPT (N.G. Rated 38.2Mj/m
3
or 9120 Kcal/m
3
SP Gr 1.00)
Liquefied Propane Gas (LPG)
3/4” NPT (LPG Rated 90.9Mj/m
3
or 21710 Kcal/m
3
SP Gr 1.52)
Natural Gas Liquified Propane Gas
kCAL/HR 75,600 75,600
cm W.C. 12.7 - 25.4 30.5 - 35.6
Mj/HR 317 317
kPa 1.25 - 3.50 3.00 - 3.50
NOTE: Pressure not to exceed 35.6 cm W.C. or 3.5 kPa
Ò HOOD VENT:
25.4 cm DIA. Connection collar. Customer is to
supply duct and ventilator fan per federal and/or local
codes. Chamber vent (steam) and combustion
exhaust are discharged into the hood. An air proving
switch is factory installed and integrated with burner
system operation. If proper ventilation is not
provided, burner will not operate. Oven provides a
relay to activate a customer supplied and powered
contactor/relay, so that when oven is powered up
external fan will operate. The hood requires a
minimum of 25.5 m
3
/min for safe operation. For fan
calculation purposes you should assume 0.15 kPa
resistance through the hood. Grease filters (optional)
may be installed in the hood instead of standard
baffle.
F25361 (January 2010)Page 7 of 60