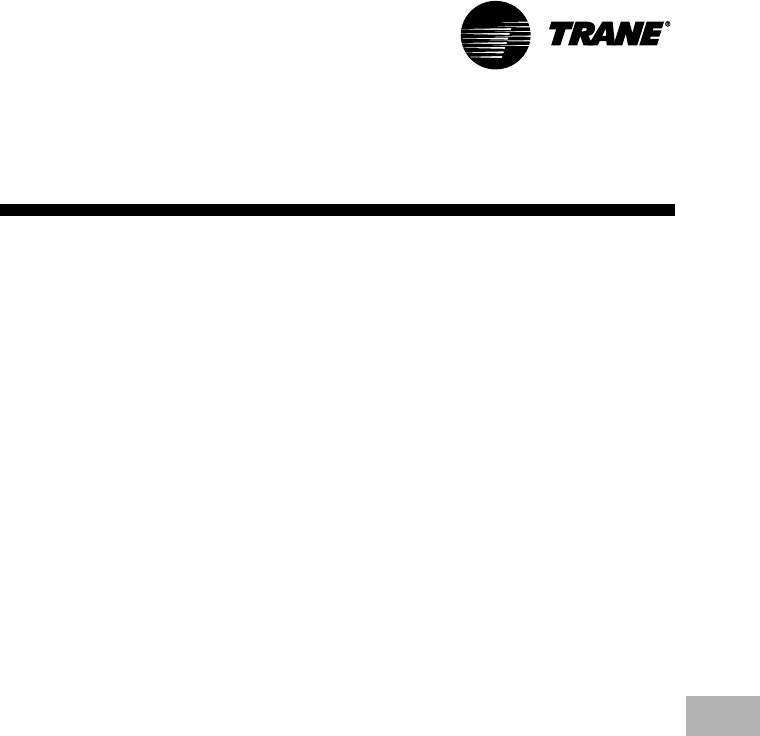
Controls
UNT-PRC001-EN 35
Control Features
The following control functions are
standard features on units with Tracer
ZN.010, ZN.510, or ZN.520.
Entering Water Temperature Sampling
Function
A system that uses a two-way control
valve option might not sense the correct
entering water temperature during long
periods when the control valve is closed.
If the demand for heating or cooling does
not exist for a long period, the entering
water will eventually approach ambient
temperature.
Using the entering water temperature
sampling function, the controller pro-
vides accurate two-pipe system
changeover—without sacrificing the
benefits of two-way control valves. Also,
it eliminates inefficient bleed or bypass
lines that can allow unnecessary
waterflow through the system.
This function periodically samples the
entering water temperature by opening
the hydronic valve. The valve opens for
20 seconds to allow the water tempera-
ture to stabilize. Then the controller reads
the entering water temperature for up to
three minutes to see if the correct water
temperature is available for the selected
operating mode.
The entering water temperature must be
five degrees or more above the space
temperature to allow hydronic heating
and five degrees or more below the
space temperature to allow hydronic
cooling. If the correct water temperature
for the operating mode is available, the
unit begins normal heating or cooling
operation. If the correct water tempera-
ture is not available, the controller closes
the control valve and waits 60 minutes
before attempting to sample the entering
water temperature again.
A factory-mounted thermistor senses
the entering water temperature on
changeover cooling/heating coil units. If
the fan-coil has a factory-mounted piping
package, the sensor is strapped to the
entering water pipe. If the fan-coil does
not have a piping package, the sensor is
coiled in the end pocket for mounting on
customer-supplied piping. This sensor
must detect accurate water temperature
for proper changeover.
Features
Automatic Heat/Cool Mode
Determination
The controller automatically determines
whether heating or cooling is needed—
based on space and system conditions.
Utilizing a proportional/integral (PI) control
algorithm to maintain the space tempera-
ture at the active heating or cooling
setpoint. The controller measures the
space temperature and active setpoint
temperature to determine the unit’s
heating or cooling capacity (zero to
100%).
Occupied/Unoccupied Operation
The occupancy input utilizes a binary
switch (i.e. motion sensor, timeclock, etc.)
that allows the zone sensor to utilize it’s
unoccupied internal setpoints.
Random Start
This feature randomly staggers multiple
unit start-up to reduce electrical demand
spikes.
Warm-up
The two-position fresh air damper option
closes during the occupied mode when
the space temperature is three degrees
or more below the heating setpoint
temperature. The damper remains
closed during warm-up until the space
temperature is within two degrees of the
heating setpoint temperature.
Cool-down
The two-position fresh air damper option
closes during the occupied mode when
the space temperature is three degrees
or more above the cooling setpoint
temperature. The damper remains
closed during cool-down until the space
temperature is within two degrees of the
cooling setpoint temperature.
Manual Output Test Function
This feature is an invaluable tool for
troubleshooting a unit. By simply press-
ing the controller’s test button, service
personnel can manually exercise outputs
in a pre-defined sequence.
Peer to Peer Communication (ZN.510
and ZN.520)
Peer to peer communication allows
multiple units in one space to share the
same zone sensor and provide simulta-
neous heating and cooling. The ZN.510 or
ZN.520 controller can share information
between units on the same communica-
tion link using a twisted pair wire in the
field. Unit configuration must be modified
with Rover service tool.
Economizing Control (ZN.520)
With the controller configured for
economizing control, it will calculate the
required cooling capacity every ten
seconds and modulate the damper option
open to the calculated position. If the
setpoint is not satisfied, the damper will
continue to open until the setpoint
condition has been met or the damper is
100 percent open. If this still does not
satisfy the setpoint, the cooling valve
option will begin to open and try to satisfy
the load requirements. Once capacity
exceeds the load requirements, the valve
will begin to close until the setpoint has
been reached or the damper reaches its
minimum position, which is field-adjust-
able. This option uses a three-wire,
floating point damper actuator.
A thermistor to sense discharge air is
factory mounted near the discharge
surface of the last coil for use in econo-
mizing and cascade temperature control.
Summit
®
can also utilize this temperature
value as a read-only point. Cascade
temperature control uses both the zone
and discharge air temperatures to more
accurately calculate the required unit
capacity.
A thermistor to sense fresh air is factory
mounted at the unit’s fresh air opening for
use in economizer applications or as a
read-only point for Summit. If the fresh air
temperature is a read-only value, it will
not impact the control algorithm. In an
economizer application, a fresh air
temperature signal must be provided
either by this thermistor or Summit.