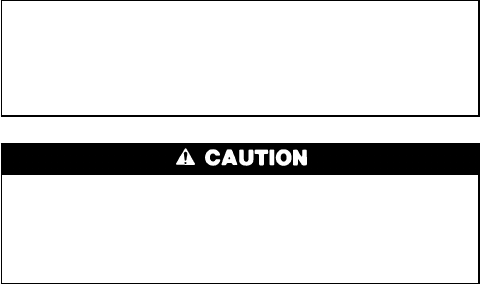
Tower Fan Relay — Low condenser water tempera-
ture can cause the chiller to shut down on low refrigerant
temperature. The tower fan relay, located in the starter, is
controlled by the PIC to energize and deenergize as the pres-
sure differential between cooler and condenser vessels changes
in order to prevent low condenser water temperature and to
maximize chiller efficiency. The tower fan relay can only
accomplish this if the relay has been added to the cooling
tower temperature controller. The TOWER FAN RELAY is
turned on whenever the CONDENSER WATER PUMP is
running, flow is verified, and the difference between cooler
and condenser pressure is more than 45 psid (310 kPad)
[30 psid (207 kPad)] or entering condenser water temper-
ature is greater than 85 F (29 C). The TOWER FAN RELAY
is deenergized when the condenser pump is off, flow is lost,
the evaporator refrigerant temperature is less than the over-
ride temperature, or the differential pressure is less than
40 psid (279 kPad) [28 psid (193 kPad)] and entering con-
densing water is less than 80 F (27 C).
IMPORTANT:A field-supplied water temperature con-
trol system for condenser water should be installed.
The system should maintain the leaving condenser wa-
ter temperature at a temperature that is 20° F (11° C)
above the leaving chilled water temperature.
The tower-fan relay control is not a substitute for a con-
denser water temperature control. When used with a
Water Temperature Control system, the tower fan relay
control can be used to help prevent low condenser wa-
ter temperatures.
Auto. Restart After Power Failure — This option
may be enabled or disabled, and may be viewed/modified in
the Config table of Equipment Configuration. If enabled, the
chiller will start up automatically after a single cycle drop-
out, low, high, or loss of voltage has occurred, and the power
is within ±10% of normal. The 15- and 3-minute inhibit tim-
ers are ignored during this type of start-up.
When power is restored after the power failure, and if the
compressor had been running, the oil pump will be ener-
gized for one minute prior to the evaporator pump ener-
gizing. Auto restart will then continue like a normal
start-up.
If power to the PSIO module has been off for more than
3 hours, the oil heat algorithm, discussed in the Oil Sump
Temperature Control section on page 32, will take effect be-
fore the compressor can start. Refrigerant normally migrates
into the oil when the oil heater is left off for extended pe-
riods of time. The PIC operates the oil pump for 1 to 2 min-
utes to ensure that the oil is free of excess refrigerant. Once
this algorithm is completed, the RESTART of the chiller will
continue.
Water/Brine Reset — Three types of chilled water or
brine reset are available and can be viewed or modified on
the Equipment Configuration table Config selection.
The LID default screen status message indicates when
the chilled water reset is active. The Control Point tempera-
ture on the Status01 table indicates the chiller’s current reset
temperature.
To activate a reset type, input all configuration informa-
tion for that reset type in the Config table. Then input the
reset type number in the SELECT/ENABLE RESET TYPE
input line.
RESET TYPE 1—Reset Type 1 requires an optional 8-input
module. It is an automatic chilled water temperature reset
based ona4to20mAinput signal. This type permits up to
± 30° F (± 16° C) of automatic reset to the chilled water or
brine temperature set point, based on the input froma4to
20 mA signal. This signal is hardwired into the number one
8-input module.
If the 4-20 mA signal is externally powered from the 8-input
module, the signal is wired to terminals J1-5(+) and J1-6(–).
If the signal is to be internally powered by the 8-input mod-
ule (for example, when using variable resistance), the signal
is wired to J1-7(+) and J1-6(–). The PIC must now be con-
figured on the Service2 table to ensure that the appropriate
power source is identified.
RESET TYPE 2—Reset Type requires an optional 8-input
module. It is an automatic chilled water temperature reset
based on a remote temperature sensor input. This reset type
permits ± 30° F (± 16° C) of automatic reset to the set point
based on a temperature sensor wired to the number one 8-input
module (see wiring diagrams or certified drawings). The tem-
perature sensor must be wired to terminal J1-19 and J1-20.
To configure Reset Type 2, enter the temperature of the
remote sensor at the point where no temperature reset will
occur. Next, enter the temperature at which the full amount
of reset will occur. Then, enter the maximum amount of re-
set required to operate the chiller. Reset Type 2 can now be
activated.
RESET TYPE 3—Reset Type 3 is an automatic chilled
water temperature reset based on cooler temperature differ-
ence. This type of reset will add ± 30° F (± 16° C) based on
the temperature difference between entering and leaving chilled
water temperature. This is the only type of reset available
without the need of the number one 8-input module. No wir-
ing is required for this type as it already uses the cooler
water sensors. To configure Reset Type 3, enter the chilled
water temperature difference (the difference between enter-
ing and leaving chilled water) at which no temperature reset
occurs. This chilled water temperature difference is usually
the full design load temperature difference. The difference in
chilled water temperature at which the full amount of
reset will occur is now entered on the next input line. Next,
the amount of reset is entered. Reset Type 3 can now be
activated.
Demand Limit Control, Option — (Requires
Optional 8-Input Module) —
The demand limit may
be externally controlled witha4to20mAsignal from an
energy management system (EMS). The option is set up on
the Config table. When enabled, the control is set for 100%
demand with 4 mA and an operator configured minimum de-
mand set point at 20 mA.
The Demand Reset input from an energy management
system is hardwired into the number one, 8-input module.
The signal may be internally powered by the module or
externally powered. If the signal is externally powered, the
signal is wired to terminals J1-1 (+) and J1-2 (–). If the sig-
nal is internally powered, the signal is wired to terminals
J1-3 (+) and J1-2 (–). When enabled, the control is set for
100% demand with 4 mA and an operator configured mini-
mum demand set point at 20 mA.
Surge Prevention Algorithm — This is an operator
configurable feature which can determine if lift conditions
are too high for the compressor and then take corrective
action. Lift is defined as the difference between the pressure
at the impeller eye and the impeller discharge. The maxi-
mum lift that a particular impeller can perform varies with
the gas flow across the impeller and the size of the impeller.
33