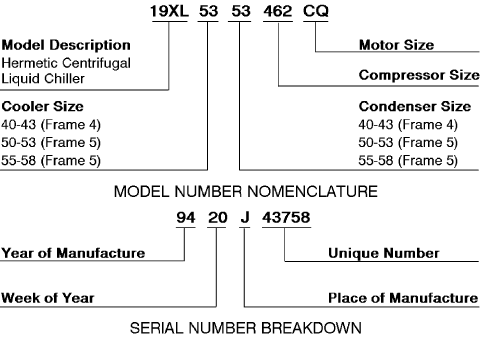
CHILLER FAMILIARIZATION
(Fig. 1, 2A, and 2B)
Chiller Information Plate —
The information plate
is located on the right side of the chiller control center
panel.
System Components — The components include the
cooler and condenser heat exchangers in separate vessels,
motor-compressor, lubrication package, control center, and
motor starter.All connections from pressure vessels have ex-
ternal threads to enable each component to be pressure tested
with a threaded pipe cap during factory assembly.
Cooler — This vessel (also known as the evaporator) is
located underneath the compressor. The cooler is main-
tained at lower temperature/pressure so that evaporating
refrigerant can remove heat from water flowing through its
internal tubes.
Condenser — The condenser operates at a higher
temperature/pressure than the cooler, and has water flowing
through its internal tubes in order to remove heat from the
refrigerant.
Motor-Compressor — This component maintains sys-
tem temperature/pressure differences and moves the heat
carrying refrigerant from the cooler to the condenser.
Control Center — The control center is the user inter-
face for controlling the chiller. It regulates the chiller’s
capacity as required to maintain proper leaving chilled water
temperature. The control center:
• registers cooler, condenser, and lubricating system
pressures
• shows chiller operating condition and alarm shutdown
conditions
• records the total chiller operating hours
• sequences chiller start, stop, and recycle under micro-
processor control
• provides access to other CCN (Carrier Comfort Network)
devices
Factory-Mounted Starter (Optional) — The starter
allows the proper start and disconnect of electrical energy
for the compressor-motor, oil pump, oil heater, and control
panels.
Storage Vessel (Optional) — There are 2 sizes
of storage vessels available. The vessels have double relief
valves, a magnetically coupled dial-type refrigerant level
gage, a one-inch FPT drain valve, and a
1
⁄
2
-in. male flare
vapor connection for the pumpout unit. A 30-in.-0-400 psi
(–101-0-2750 kPa) gage also is supplied with each unit.
NOTE: If a storage vessel is not used at the jobsite, factory-
installed isolation valves on the chiller may be used to iso-
late the chiller charge in either the cooler or condenser.
An optional pumpout compressor system is used to transfer
refrigerant from vessel to vessel.
REFRIGERATION CYCLE
The compressor continuously draws refrigerant vapor from
the cooler, at a rate set by the amount of guide vane opening.
As the compressor suction reduces the pressure in the cooler,
the remaining refrigerant boils at a fairly low temperature
(typically 38 to 42 F [3 to 6 C]). The energy required for
boiling is obtained from the water flowing through the cooler
tubes. With heat energy removed, the water becomes cold
enough for use in an air conditioning circuit or process liq-
uid cooling.
After taking heat from the water, the refrigerant vapor
is compressed. Compression adds still more heat energy
and the refrigerant is quite warm (typically 98 to 102 F
[37 to 40 C]) when it is discharged from the compressor into
the condenser.
Relatively cool (typically 65 to 90 F [18 to 32 C]) water
flowing into the condenser tubes removes heat from the
refrigerant and the vapor condenses to liquid.
The liquid refrigerant passes through orifices into the
FLASC (Flash Subcooler) chamber (Fig. 3). Since the FLASC
chamber is at a lower pressure, part of the liquid refrigerant
flashes to vapor, thereby cooling the remaining liquid. The
FLASC vapor is recondensed on the tubes which are cooled
by entering condenser water. The liquid drains into a float
chamber between the FLASC chamber and cooler. Here a
float valve forms a liquid seal to keep FLASC chamber
vapor from entering the cooler. When liquid refrigerant passes
through the valve, some of it flashes to vapor in the reduced
pressure on the cooler side. In flashing, it removes heat from
the remaining liquid. The refrigerant is now at a temperature
and pressure at which the cycle began.
MOTOR/OIL REFRIGERATION
COOLING CYCLE
The motor and the lubricating oil are cooled by liquid
refrigerant taken from the bottom of the condenser vessel
(Fig. 3). Flow of refrigerant is maintained by the pressure
differential that exists due to compressor operation.After the
refrigerant flows past an isolation valve, an in-line
filter, and a sight glass/moisture indicator, the flow is split
between motor cooling and oil cooling systems.
Flow to the motor flows through an orifice and into the
motor.There is also another orifice and a solenoid valve which
will open if additional motor cooling is required. Once past
the orifice, the refrigerant is directed over the motor by a
spray nozzle. The refrigerant collects in the bottom of the
motor casing and then is drained back into the cooler through
the motor refrigerant drain line. A back pressure valve or an
orifice in this line maintains a higher pressure in the motor
shell than in the cooler/oil sump. The motor is protected by
a temperature sensor imbedded in the stator windings. Higher
motor temperatures (above 125 F [51 C]) energize a sole-
noid to provide additional motor cooling. A further increase
in temperature past the motor override set point will over-
ride the temperature capacity control to hold, and if the
motor temperature rises 10° F (5.5° C) above this set point,
will close the inlet guide vanes. If the temperature rises above
the safety limit, the compressor will shut down.
Fig. 1 — 19XL Identification
5