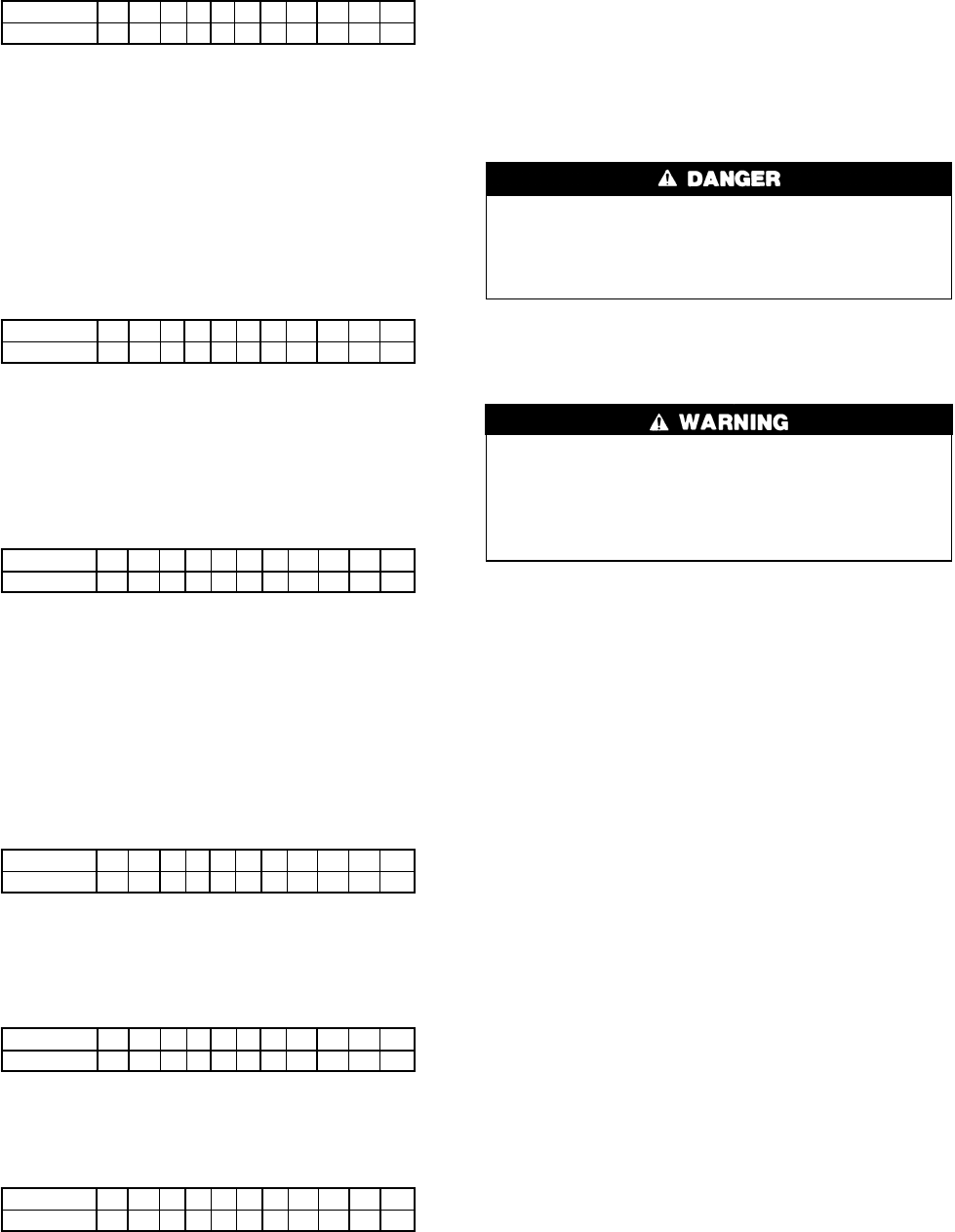
TRANSFER ALL REFRIGERANT TO CHILLER
COOLER/COMPRESSOR VESSEL
1. Push refrigerant into the chiller cooler vessel.
a. Valve positions:
VALVE 1a 1b 2 3 4 5 8 11 12 13 14
CONDITION C CC CCC
b. Turn off chiller water pumps and pumpout condenser
water.
c. Turn on pumpout compressor to push refrigerant out
of the condenser.
d. When all liquid is out of the condenser, close cooler
isolation valve 11.
e. Turn off the pumpout compressor.
2. Evacuate gas from the chiller condenser vessel.
a. Access the Control Test Pumpdown table on the LID
display to turn on the chiller water pumps.
b. Close pumpout valves 3 and 4; open valves 2 and 5.
VALVE 1a 1b 2 3 4 5 8 11 12 13 14
CONDITION CC CCCCC
c. Turn on pumpout condenser water.
d. Run the pumpout compressor until the chiller com-
pressor reaches 18 in. Hg vac (40 kPa abs.). Monitor
pressure at the LID and refrigerant gages.
e. Close valve 1b.
f. Turn off pumpout compressor.
g. Close valves 1a, 2, and 5.
VALVE 1a1b2345811121314
CONDITION C C CCCCCC C C C
h. Turn off pumpout condenser water.
i. Proceed to the Pumpdown test on the LID to turn off
chiller water pumps and lockout chiller compressor.
RETURN REFRIGERANT TO NORMAL OPERATING
CONDITIONS
1. Be sure that the chiller vessel that was opened has been
evacuated.
2. Access the Control Test Terminate Lockout table to view
vessel pressures and turn on chiller water pumps.
3. Open valves 1a, 1b, and 3.
VALVE 1a 1b 2 3 4 5 8 11 12 13 14
CONDITION C CCCC C C C
4. Crack open valve 5, gradually increasing pressure in the
evacuated vessel to 68 psig (469 kPa) [35 psig (141 kPa)].
Feed refrigerant slowly to prevent tube freeze up.
5. Leak test to ensure vessel integrity.
6. Open valve 5 fully.
VALVE 1a1b2345811121314
CONDITION CCCCCCC
7. Open valve 11 to equalize the liquid refrigerant level
between vessels.
8. Close valves 1a, 1b, 3, and 5.
9. Open isolation valves 11, 12, 13, and 14 (if present).
VALVE 1a1b2345811121314
CONDITION C C CCCCC
10. Proceed to Terminate Pumpdown Lockout test to turn
off water pumps and enable the chiller compressor for
start-up.
GENERAL MAINTENANCE
Refrigerant Properties —
HCFC-22 or HFC-134a
is the standard refrigerant in the 19XL. At normal atmo-
spheric pressure, HCFC-22 will boil at –41 F (–40 C) and
HFC-134a will boil at –14 F (–25 C) and must, therefore, be
kept in pressurized containers or storage tanks. The refrig-
erants are practically odorless when mixed with air. Both
refrigerants are non-combustible at atmospheric pressure.Read
the Material Safety Data Sheet and the latestASHRAE Safety
Guide for Mechanical Refrigeration to learn more about safe
handling of these refrigerants.
HCFC-22 and HFC-134a will dissolve oil and some
non-metallic materials, dry the skin, and, in heavy con-
centrations, may displace enough oxygen to cause
asphyxiation. When handling this refrigerant, protect the
hands and eyes and avoid breathing fumes.
Adding Refrigerant — Follow the procedures de-
scribed in Trimming Refrigerant Charge section, page 54.
Always use the compressor Pumpdown function in the
Control Test table to turn on the evaporator pump and
lock out the compressor when transferring refrigerant.
Liquid refrigerant may flash into a gas and cause pos-
sible freeze-up when the chiller pressure is below
65 psig (448 kPa) [30 psig (207 kPa)].
Removing Refrigerant — If the optional pumpout unit
is used, the 19XL refrigerant charge may be transferred to a
pumpout storage tank or to the chiller condenser or cooler
vessels. Follow procedures in the Pumpout and Refrigerant
Transfer Procedures section when removing refrigerant from
the pumpout storage tank to the chiller vessel.
Adjusting the Refrigerant Charge — If the addi-
tion or removal of refrigerant is required for improved chiller
performance, follow the procedures given under the Trim
Refrigerant Charge section, page 62.
Refrigerant Leak Testing — Because HCFC-22 and
HFC-134a are above atmospheric pressure at room tempera-
ture, leak testing can be performed with refrigerant in the
chiller. Use an electronic, halide leak detector, soap bubble
solution, or ultra-sonic leak detector. Be sure that the room
is well ventilated and free from concentration of refrigerant
to keep false readings to a minimum. Before making any
necessary repairs to a leak, transfer all refrigerant from the
leaking vessel.
Leak Rate — ASHRAE recommends that chillers should
be immediately taken off line and repaired if the refrigerant
leakage rate for the entire chiller is more than 10% of the
operating refrigerant charge per year.
Additionally, Carrier recommends that leaks totalling less
than the above rate but more than a rate of 1 lb (0.5 kg)
per year should be repaired during annual maintenance or
whenever the refrigerant is pumped over for other service
work.
Test After Service, Repair, or Major Leak — If
all refrigerant has been lost or if the chiller has been opened
for service, the chiller or the affected vessels must be pres-
sured and leak tested. Refer to the Leak Test Chiller section
to perform a leak test.
61