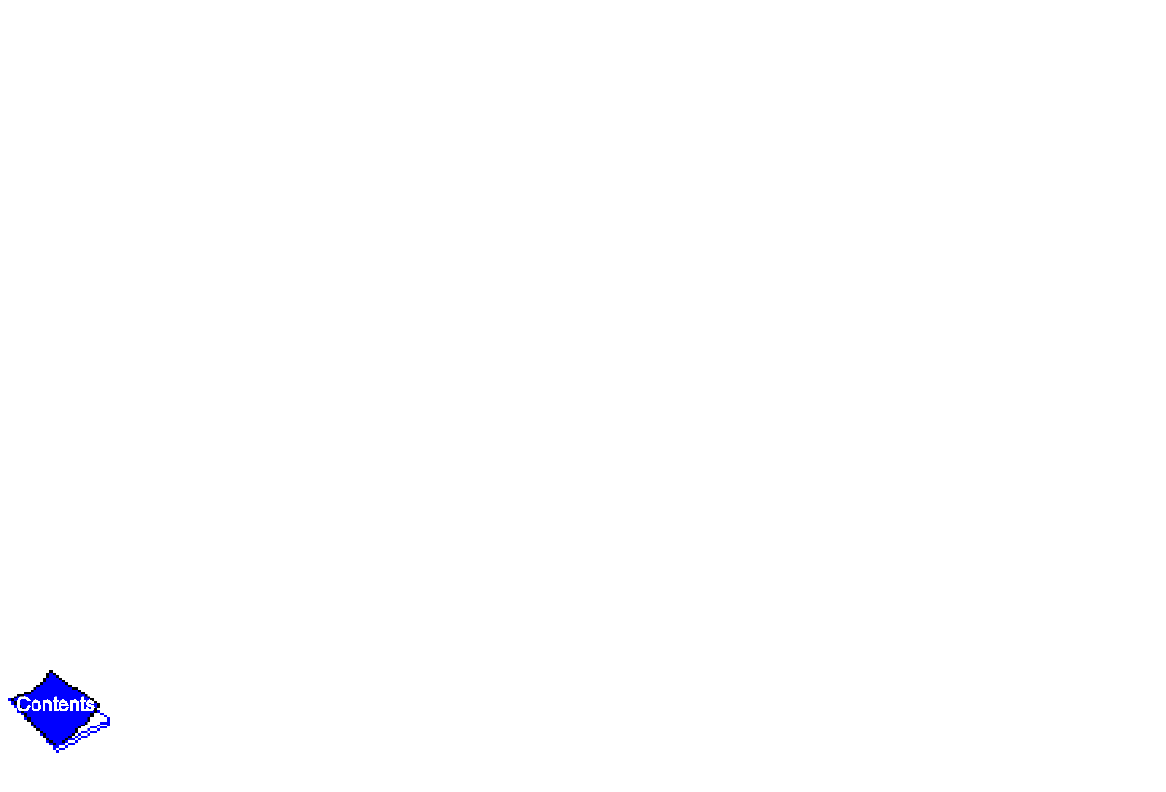
also is supplied with each unit.
Note: If a storage vessel is not used at the jobsite, factory-installed isolation valves on the
chiller may be used to isolate the machine charge in either the cooler or condenser. An
optional pumpout compressor system is used to transfer refrigerant from vessel to ves-
sel.
Refrigeration Cycle
The compressor continuously draws refrigerant vapor from the cooler, at a rate set by the
amount of guide vane opening. As the compressor suction reduces the pressure in the cooler,
the remaining refrigerant boils at a fairly low temperature (typically 38 to 42 F [3 to 6 C]). The
energy required for boiling is obtained from the water flowing through the cooler tubes. With
heat energy removed, the water becomes cold enough for use in an air conditioning circuit or
process liquid cooling.
After taking heat from the water, the refrigerant vapor is compressed. Compression adds still
more heat energy and the refrigerant is quite warm (typically 98 to 102 F [37 to 40 C]) when it is
discharged from the compressor into the condenser.
Relatively cool (typically 65 to 90 F [18 to 32 C]) water flowing into the condenser tubes
removes heat from the refrigerant and the vapor condenses to liquid.
The liquid refrigerant passes through orifices into the FLASC (Flash Subcooler) chamber