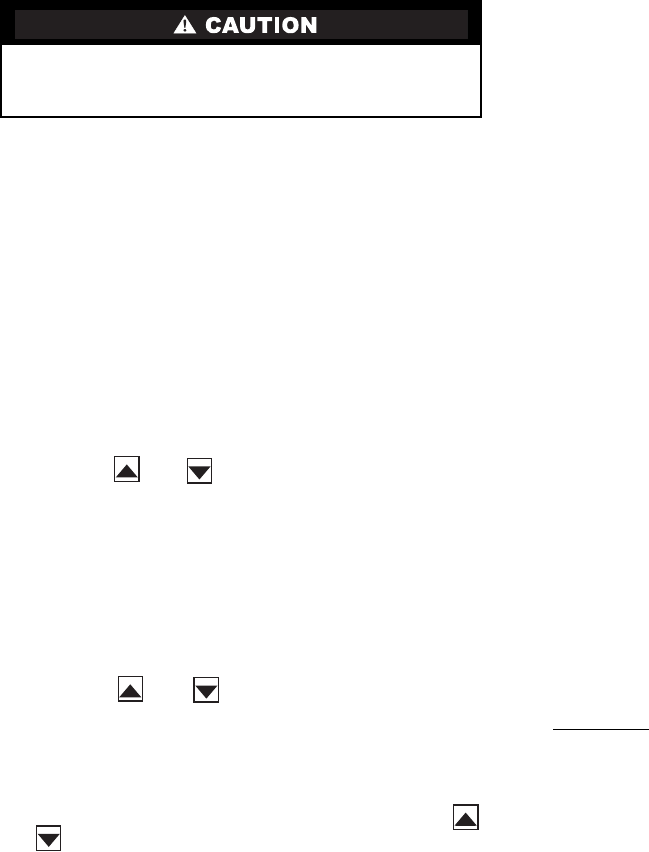
69
PROGRAMMING
Motormaster V control is completely configured according to
the inputs provided. No additional programming is necessary.
The drive can display 71 program parameters. Parameters
50-60 are monitor functions and cannot be changed. The
remainder of the parameters can be changed after entering a
password.
To enter password and change program values:
1. Press Mode.
2. Upper right decimal point blinks.
3. Display reads “00” (see Fig. 37). To enter the PRO-
GRAM mode to access the parameters, press the Mode
button (see Fig. 37). This will activate the PASSWORD
prompt (if the password has not been disabled). The dis-
play will read “00” and the upper right-hand decimal
point will be blinking.
4. Use the and buttons to scroll to the password
value (the factory default password is “111”) and press
the Mode button. Once the correct password value is en-
tered, the display will read “P01”, which indicates that the
PROGRAM mode has been accessed at the beginning of
the parameter menu (P01 is the first parameter).
NOTE: If the display flashes “Er”, the password was incorrect,
and the process to enter the password must be repeated.
5. Press Mode to display present parameter setting.
Upper right decimal point blinks.
Use the and buttons to scroll to the desired
parameter number.
Once the desired parameter number is found, press the
Mode button to display the present parameter setting. The up-
per right-hand decimal point will begin blinking, indicating
that the present parameter setting is being displayed, and that it
can be changed by using the up and down buttons. Use
and to change setting. Press Mode to store new setting.
Pressing the Mode will store the new setting and also exit
the PROGRAM mode. To change another parameter, press the
Mode key again to re-enter the PROGRAM mode (the param-
eter menu will be accessed at the parameter that was last
viewed or changed before exiting). If the Mode key is pressed
within two minutes of exiting the PROGRAM mode, the pass-
word is not required access the parameters. After two minutes,
the password must be entered in order to access the parameters
again.
To change password: first enter the current password then
change parameter P44 to the desired password.
To disable automatic control mode and enter manual speed
control mode:
1. Change P05 to ‘01- keypad’.
2. Push UP and DOWN arrow key to set manual speed.
3. Set P05 to ‘05 - R22’ to restore automatic control.
To provide manual start/stop control:
With power removed from VFD, remove start command
jumper and install a switch between the appropriate start termi-
nals as required in Fig 37.
EPM CHIP — The drive uses a electronic programming mod-
ule (EPM) chip to store the program parameters. This is an EE-
PROM memory chip and is accessible from the front of the
VFD. It should not be removed with power applied to the
VFD.
LIQUID LINE PRESSURE SET POINT ADJUST-
MENT — Adjusting the set point is not recommended due to
possible interaction with other head pressure software algo-
rithms or controls. In situations where the set point must be
changed, the set point for R-22 is found in P34. A higher value
will result in a higher liquid line set point. Example: increasing
the factory default (P34) set point from 18.0 to 19.0 will in-
crease the liquid line pressure by approximately 10 psi.
LOSS OF SCN COMMUNICATIONS — Sterlco Comfort
Network (SCN) communications with external control
systems can be affected by high frequency electrical noise gen-
erated by the Motormaster V control. Ensure unit is well
grounded to eliminate ground currents along communication
lines.
If communications are lost only while Motormaster V con-
trol is in operation, order a signal isolator (CEAS420876-2)
and power supplies (CEAS221045-01, 2 required) for the SCN
communication line.
Fault Codes
— The drive is programmed to automatically re-
start after a fault and will attempt to restart three times after a
fault (the drive will not restart after CF, cF, GF, F1, F2-F9, or
Fo faults). If all three restart attempts are unsuccessful, the
drive will trip into FAULT LOCKOUT (LC), which requires a
manual reset.
NOTE: Since faults may be reset as incoming power is cycled,
you may need to observe current fault code before the Sterling
unit control turns off the VFD. Most recent faults can be
accessed using parameter 50. If necessary, remove start jumper
and energize condenser fan contactor using Service Test. This
will allow programming and access to fault history.
It is strongly recommended that the user NOT change any
programming without consulting Sterling service personnel.
Unit damage may occur from improper programming.