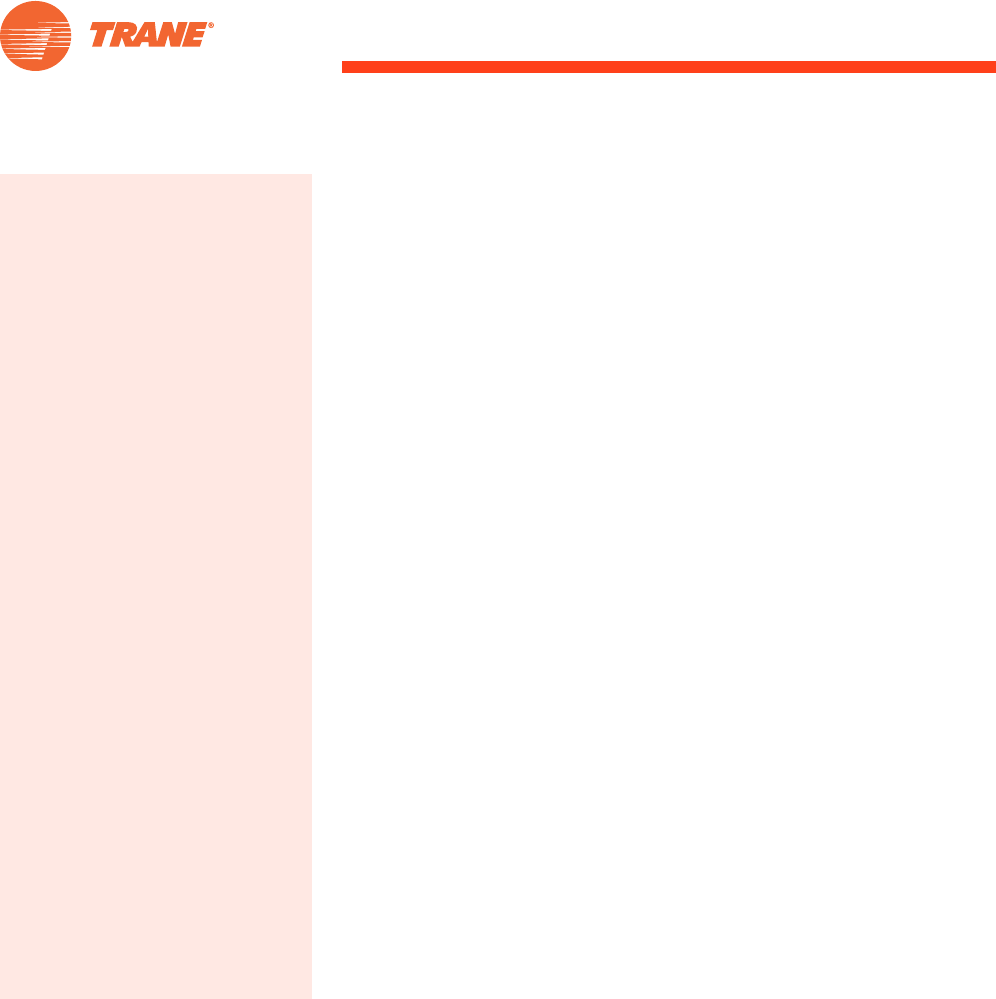
System Configurations
SYS-APM001-EN Chiller System Design and Control 57
secondary systems. The pressure drops previously satisfied by the
distribution pumps are instead satisfied by the now larger primary-only
pumps, permitting selection of larger, more efficient pumps (with efficiencies
similar to those of the secondary pumps in a primary–secondary system).
VPF systems present building owners with several cost-saving benefits that
are directly related to the pumps. The most obvious cost savings result from
eliminating the constant flow primary pumps, which, in turn, avoids the
material and labor expenses incurred with the associated piping connections,
mechanical room space, and electrical service. Although the number of
pumps is reduced, the sizes of both the pumps and the variable-frequency
drives increase since the pumps must be sized to overcome the entire
system’s pressure drop. This offsets some of the installed cost savings of
having fewer pumps.
Building owners often cite pump-related energy savings as the reason they
installed a VPF system. With the help of a software analysis tool such as
System Analyzer™, TRACE™ 700, Chiller Plant Analyzer, or EnergyPlus, you
can determine whether the anticipated energy savings justify the use of
variable-primary flow in a particular application.
It may be easier to apply a variable-primary-flow system rather than a
primary–secondary system to an existing constant-flow chilled-water plant.
Unlike the primary–secondary design, the bypass can be positioned almost
anywhere in the chilled-water loop and an additional pump is unnecessary.
Chiller selection requirements
Variable-flow systems require chillers that can operate properly when
evaporator flow varies. Varying the water-flow rate through the chiller
evaporator poses two control challenges for those who design and operate
VPF systems:
1 Maintaining the chiller flow rate between the minimum and maximum
limits of the evaporator
2 Managing transient flows without compromising stable operation,
especially in multi-chiller plants
Evaporator flow limits
Select for a minimum evaporator-flow limit that is ≤60 percent of the chiller’s
design flow rate. One benefit of VPF systems is reduced pumping energy. To
realize this benefit, chilled water flow must not remain constant. As the flow
decreases, it approaches the minimum flow rate of the chillers—so, how do
we select for a minimum chiller flow rate that will result in the pump-energy
savings?
The answer depends on the type of chiller, but generally speaking, lower is
better because it extends the ability of a single chiller to operate at low loads
without bypass flow. Most of the potential savings are realized by the time
that the system flow rate decreases to 50 percent of design.
Dispelling a common
misconception
True or false: “Chillers operate more
efficiently in a system with variable
rather than constant primary flow
because of the greater log mean
temperature difference (LMTD).”
It is true that the return water
temperature in a properly operating VPF
system remains constant as the amount
of flow changes. It is also true that the
LMTD can be increased by changing the
production (primary) side of the chilled-
water loop from constant to variable
flow. But there are other facts to
consider.
In a system with constant primary flow:
• Entering-evaporator temperature and
LMTD fall as the cooling load
diminishes.
• The convective heat transfer
coefficient, like the primary flow,
remains constant despite reductions
in load.
In a system with variable primary flow:
• The convective heat transfer
coefficient in the chiller evaporator
decreases with a reduction in flow.
• Reduced flow decreases the overall
heat-transfer effectiveness of the
chiller evaporator.
The net effect is that the power
consumption for a given chiller is
virtually the same whether the chiller’s
evaporator flow is variable or constant.