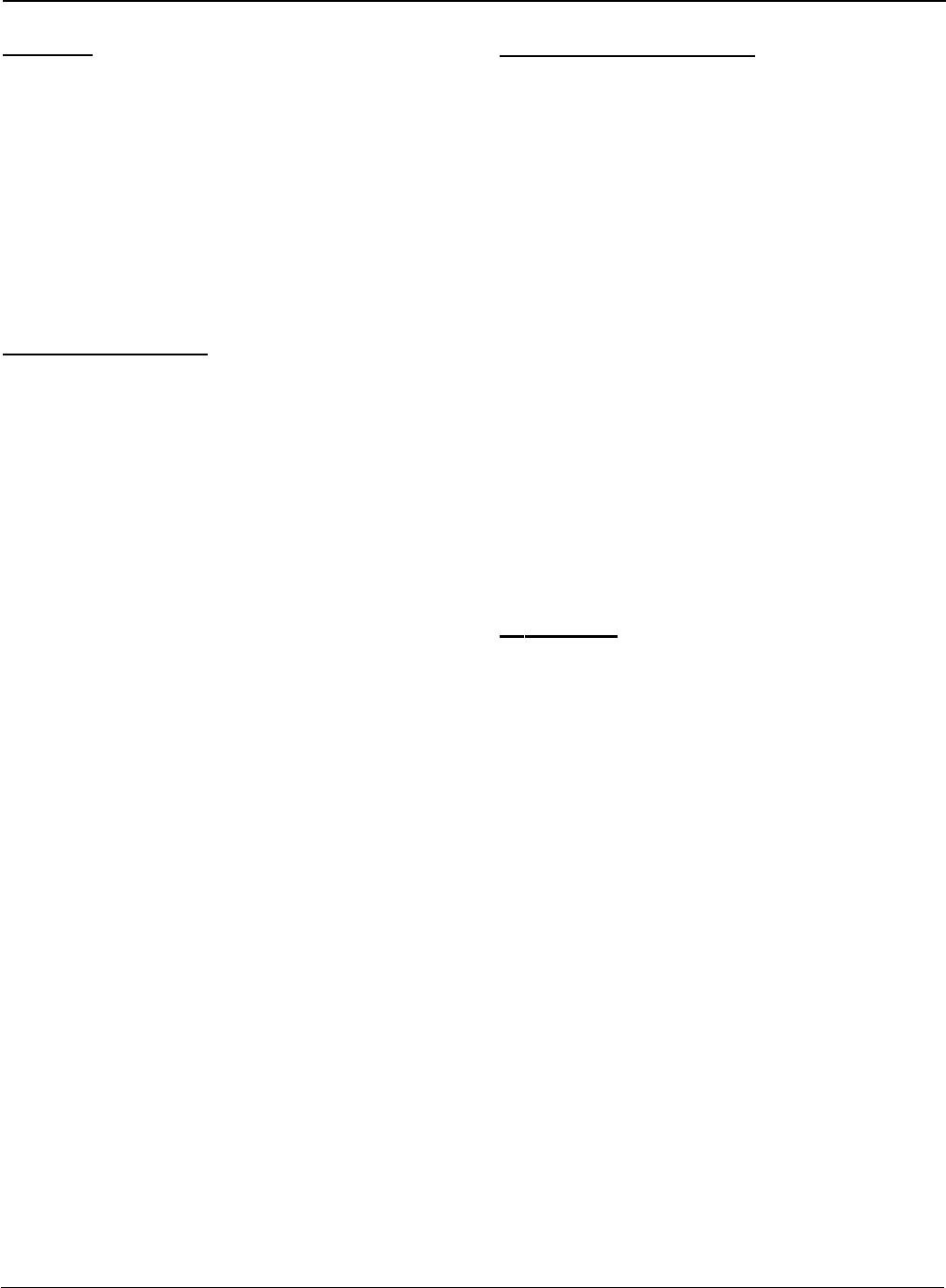
3M-Matic 800rf Case Sealer Theory of Operation
Copyright 1999, 3M IPC. All rights reserved. 5-15
Photocells
Six photocells positioned along the left side (front) of
the case sealer detect the presence of boxes as they
pass through the case sealer. Each photocell emits
infrared light that is normally reflected back to the
photocell from a reflector on the right side (rear) of
the case sealer. In their light-sensing condition, the
photocells provide a low (0 V) input to their respec-
tive PLC inputs. When a moving box blocks a
photocell light path, the photocell output to the PLC
becomes +24 VDC, signaling the boxs presence.
Motor Control Circuits
There are two motor control circuits in the 800rf: one
for the infeed drive motors, and one for the side belt
drive motors.
The infeed drive motor control circuit consists of the
Motor Control Relays K2 and K4 and the Overload
Circuit Breakers OL3 and OL4 and their related
auxiliary contacts. Energizing K2 and K4 closes their
contacts, providing AC (through the OL3 and OL4
contacts) to the infeed drive motors. The OL3 and
OL4 circuit breakers protect the infeed drive motors
from burnout due to overload conditions. If an
overload condition occurs in either motor, all of the
motor-related OL3 or OL4 contacts actuate. The
contacts in series with the motor open to remove
drive AC.
The side belt drive motor control circuit consists of
the Motor Control Relay K1 and the Overload Circuit
Breakers OL1 and OL2 and their related auxiliary
contacts. Energizing K1 closes its contacts, providing
AC (through the OL1 and OL2 contacts) to the side
belt drive motors. The OL1 and OL2 circuit breakers
protect the side belt drive motors from burnout due to
overload conditions. If an overload condition occurs
in either motor, all of the motor-related OL1 or OL2
contacts actuate. The contacts in series with the
motor open to remove drive AC.
Overload Circuit Breakers OL1, OL2, OL3, and OL4
can be adjusted to actuate at different current settings
within their 1-amp to 1.6-amp operating range.
Normally, they are set at 1.4 amp.
E-Stop/Guard Door Switches
This circuit consists of six switches connected in
series; the four Guard Door Interlocks GRD1, GRD2,
GRD3, and GRD4, and two E-Stop switches. These
switches are all normally closed, presenting a +24
VDC enable signal to PLC input IN 3. If any of
these switches open, +24 VDC is removed from the
Master Control Relay K3 and PLC IN 3, causing the
PLC to stop all case sealer operations.
A Guard Door Interlock switch opens whenever its
corresponding safety door is opened.
One E-Stop switch is mounted on the rear main
frame of the case sealer; the other E-Stop switch is
mounted on the Electrical Control Panel. The E-
Stop switches are red latching push-button switches
easily operated from either side of the case sealer.
When either E-Stop switch is pressed, it latches in
the down (open) position and the case sealer cannot
be restarted until the switch is unlatched (closed) by
turning the red latching push-button switch clock-
wise and releasing it.
STOP Switch
The STOP switch S1, located on the Electrical
Control Panel, is normally closed, presenting a +24
VDC enable signal to PLC input IN 0. Pressing the
STOP switch removes +24 VDC from PLC input IN
0, causing the PLC to stop case sealer operations and
return the case sealer to its home condition.