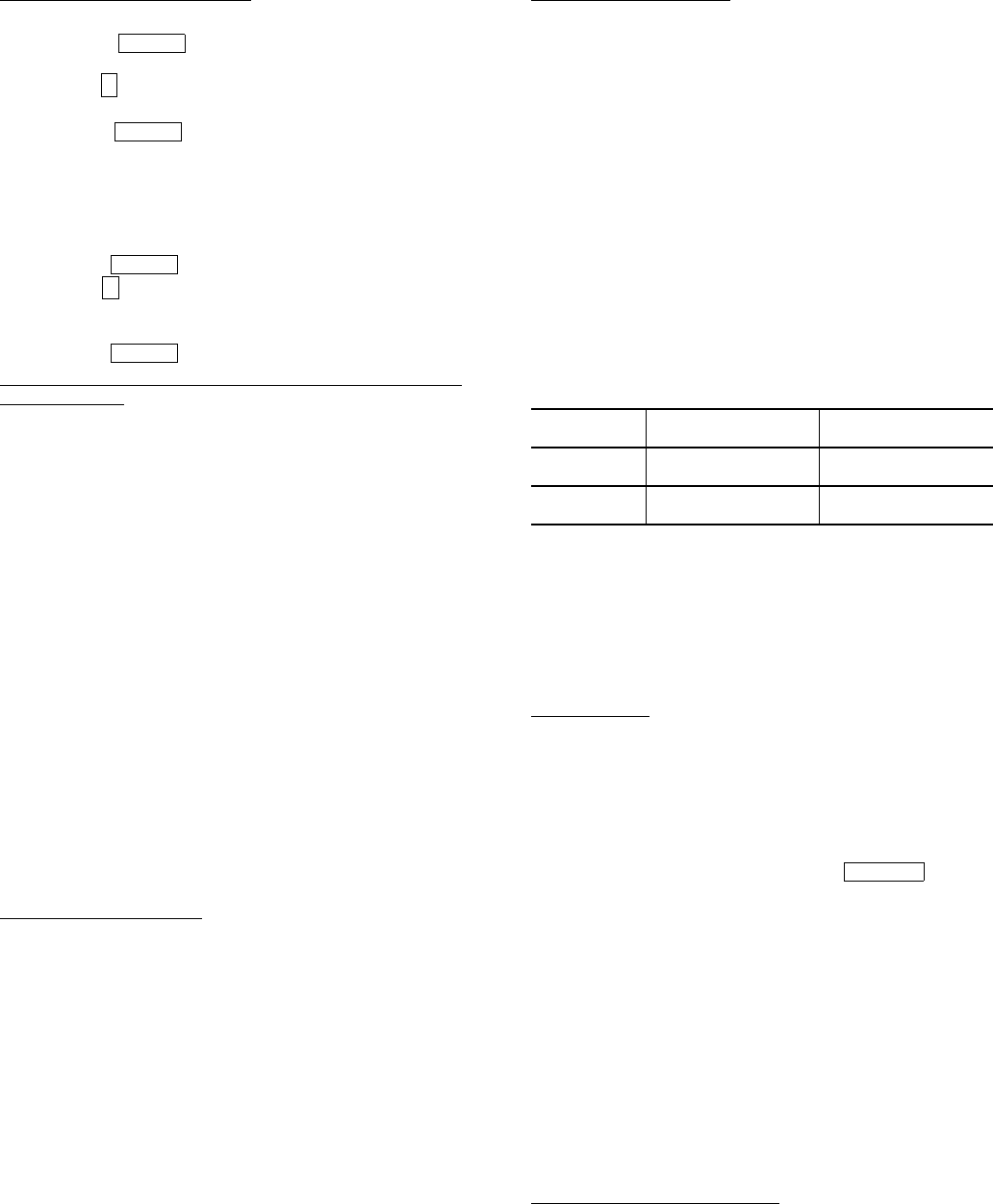
61
Protecting the VFD Configuration
1. Select parameter P.051 from the VFD keypad.
2. Press the softkey to access the parameter. A
zero will be displayed.
3. Use the arrow key to increment the value to 26. This is
the password number.
4. Press the softkey to save the value. P.051 will
by displayed.
NOTE: Parameter programming is disabled when the
PASSWORD LED is on and enabled when the PASS-
WORD LED is off.
5. Select parameter P.006 from the VFD Keypad.
6. Press the softkey to access the parameter.
7. Use the arrow key to increment the value to 107. This
is the password number to restrict displaying the remain-
ing P, and all of the H and r parameters.
8. Press the softkey to save the value.
Modify Minimum and Maximum Load Points (
∆
T1/P1;
∆
T2/
P2) If Necessary — These pairs of chiller load points, located
on the OPTIONS screen, determine when to limit guide vane
travel or open the hot gas bypass valve when surge prevention
is needed. These points should be set based on individual
chiller operating conditions.
A label that lists the configuration values of the controls is
located on the inside of the unit’s control panel. These values
are based upon the original selection of the chiller. Jobsite con-
ditions may require a slight modification to these parameters.
If after configuring a value for these points, surge preven-
tion is operating too soon or too late for conditions, these pa-
rameters should be changed by the operator.
An example of such a configuration is shown below.
Refrigerant: HCFC-134a
Estimated Minimum Load Conditions:
44 F (6.7 C) LCW
45.5 F (7.5 C) ECW
43 F (6.1 C) Suction Temperature
70 F (21.1 C) Condensing Temperature
Estimated Maximum Load Conditions:
44 F (6.7 C) LCW
54 F (12.2 C) ECW
42 F (5.6 C) Suction Temperature
98 F (36.7 C) Condensing Temperature
Calculate Maximum Load
— To calculate the maximum load
points, use the design load condition data. If the chiller full load
cooler temperature difference is more than 15 F (8.3 C), esti-
mate the refrigerant suction and condensing temperatures at
this difference. Use the proper saturated pressure and tempera-
ture for the particular refrigerant used.
Suction Temperature:
42 F (5.6 C) = 37 psig (255 kPa) saturated
refrigerant pressure (HFC-134a)
Condensing Temperature:
98 F (36.7 C) = 120 psig (1827 kPa) saturated
refrigerant pressure (HFC-134a)
Maximum Load ∆T2:
54 – 44 = 10º F (12.2 – 6.7 = 5.5º C)
Maximum Load ∆P2:
120 – 37 = 83 psid (827 – 255 = 572 kPad)
To avoid unnecessary surge prevention, add about 10 psid
(70 kPad) to ∆P2 from these conditions:
∆T2 = 10º F (5.5º C)
∆P2 = 93 psid (642 kPad)
Calculate Minimum Load
— To calculate the minimum load
conditions, estimate the temperature difference the cooler will
have at 10% load, then estimate what the suction and condens-
ing temperatures will be at this point. Use the proper saturated
pressure and temperature for the particular refrigerant used.
Suction Temperature:
43 F (6.1 C) = 38 psig (262 kPa) saturated
refrigerant pressure (HFC-134a)
Condensing Temperature:
70 F (21.1 C) = 71 psig (490 kPa) saturated
refrigerant pressure (HFC-134a)
Minimum Load ∆T1 (at 20% Load): 2 F (1.1 C)
Minimum Load ∆P1:
71 – 38 = 33 psid (490 – 262 = 228 kPad)
Again, to avoid unnecessary surge prevention, add 20 psid
(140 kPad) at ∆P1 from these conditions:
∆T1 = 2 F (1.1 C)
∆P1 = 53 psid (368 kPad)
If surge prevention occurs too soon or too late:
The differential pressure (∆P) and temperature (∆T) can be
monitored during chiller operation by viewing ACTIVE
DELTA P and ACTIVE DELTA T (HEAT_EX screen). Com-
paring SURGE/HGBP DELTA T to ACTIVE DELTA T will de-
termine when the SURGE PREVENTION function will occur.
The smaller the difference between the SURGE/HGBP DELTA
T and the ACTIVE DELTA T values, the closer to surge
prevention.
Units with VFD
— On units with VFD further adjustments can
be made if response to surge prevention or protection is not
functioning as desired. VFD GAIN and VFD INCREASE STEP
can be adjusted to allow for more aggressive changes in speed
when surge prevention or protection is active.
CONFIGURE DIFFUSER CONTROL IF NECES-
SARY — If the compressor is equipped with a variable dif-
fuser, (size 5 compressor) access the SETUP2 screen. Scroll to
DIFFUSER CONTROL and press the softkey.
Compare the diffuser and guide vane values (GUIDE VANE
25% LOAD PT, GUIDE VANE 50% LOAD PT, GUIDE VANE
75% LOAD PT, DIFFUSER 25% LOAD POINT, DIFFUSER
50% LOAD POINT, DIFFUSER 75% LOAD POINT) to the
values located on the label inside the control panel. See
Fig. 12.
Compressors with variable diffuser control have actuators
tested and stamped with the milliamp (mA) value that results in
100% actuator rotation. This value is configured on the
SETUP2 screen. It is labeled DIFFUSER FULL SPAN mA.
MODIFY EQUIPMENT CONFIGURATION IF NECES-
SARY — The EQUIPMENT SERVICE table has screens to
select, view, or modify parameters. Carrier’s certified drawings
have the configuration values required for the jobsite. Modify
these values only if requested.
SERVICE Screen Modifications
— Change the values on
these screens according to specific job data. See the certified
drawings for the correct values. Modifications can include:
• chilled water reset
• entering chilled water control (Enable/Disable)
• 4 to 20 mA demand limit
• auto restart option (Enable/Disable)
• remote contact option (Enable/Disable)
ENTER
↑
ENTER
ENTER
↑
ENTER
LOAD
SURGE PREVENTION
OCCURS TOO SOON
SURGE PREVENTION
OCCURS TOO LATE
At low loads
(<50%)
Increase P1 by
2 psid (14 kPad)
Decrease P1 by
2 psid (14 kPad)
At high loads
(>50%)
Increase P2 by
2 psid (14 kPad)
Decrease P2 by
2 psid (14 kPad)
ENABLE