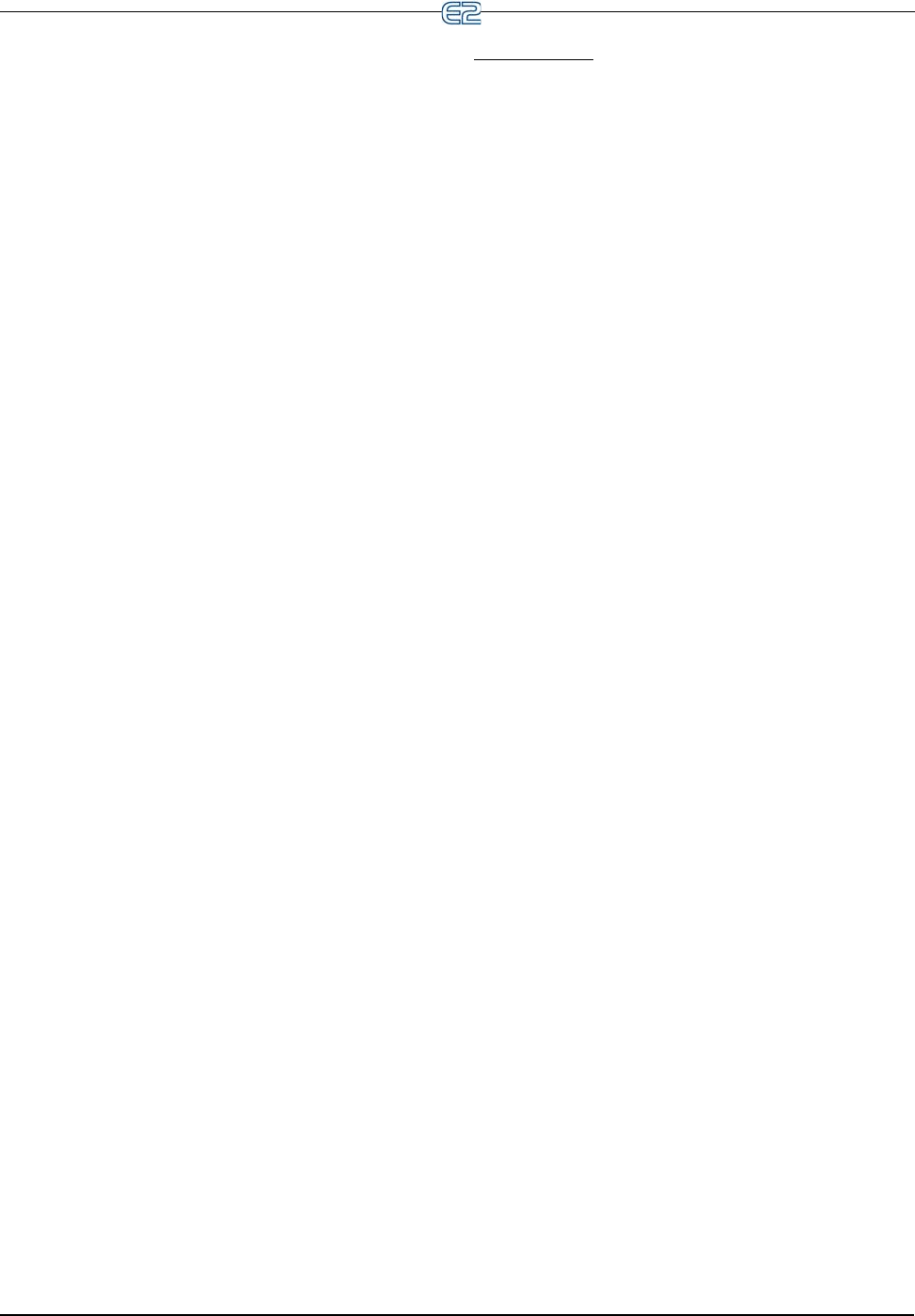
11-42 • E2 RX/BX/CX I&O Manual 026-1614 Rev 4 5-JAN-2013
assume this application will not use occupancy-based set-
points, and will use the occupied setpoint only (no switch-
ing).
Note the Select cell does not have any on-board sched-
ule function to determine for itself whether the building is
occupied or unoccupied. It relies solely on the digital state
of the Occupancy input. If you wish to follow a schedule
for occupancy, this input must be tied to the output of a
Time Schedule application.
11.13.2.2 The Setpoint Float Cell
The Setpoint Float cell provides users to raise and
lower the control setpoint based on the value of a sensor
(called the “float” sensor). The float sensor can be any
type of analog sensor, but is typically a temperature sen
-
sor, since most of the applications for floating setpoints
involve HVAC and floating the setpoint based on outdoor
air temperature.
To set up the Setpoint Float cell, you must provide
three values: a High Float Value, a Low Float Value, and
an Output Range.
The Output Range is the maximum amount that the
PID Setpoint may vary. An Output Range of 4, for exam
-
ple, means that the control setpoint may only be increased
by a maximum of 2 and decreased by a maximum of 2.
The High Float Value and Low Float Value form a
range of values that determine what portion of the Output
Range is applied to the final control setpoint. For example,
suppose a Setpoint Float cell is given a High Float Value
of 100, a Low Float Value of 0, and an Output Range of 4.
When the float sensor value is at the high float value, the
setpoint will be increased by its maximum amount (2).
When the float sensor value is at the low float value, the
setpoint will be decreased by its minimum amount (2). For
all float sensor values in between the High Float and Low
Float values, the amount added or subtracted to the control
setpoint will vary linearly.
If floating setpoint control is not desired, this cell can
be effectively disabled by setting the value of the Float
Output Range to 0.
11.13.2.3 The PID Control Cell
The PID Control cell uses a PID algorithm to compare
the control input value with the control setpoint value. The
result of this comparison is a percentage from 0-100%.
The PID Control cell repeats this sequence ever few sec
-
onds, and the result is a PID percentage that adjusts over
time to provide the optimum amount of output to achieve
the setpoint.
The 0-100% output from the PID Control cell is passed
along to the Filter cell.
Bypassing PID
For users who simply wish to convert an analog output
to a pulse width modulation or sequenced (staged) output,
a Loop/Sequence Control application can be programmed
to bypass PID Control altogether. If this option is selected,
the Loop/Sequence Control application completely
ignores the Select, Setpoint Float, and PID Control cells,
and passes on the value of the control input directly to the
Filter cell.
Note that when bypassing PID, the control input must
be an analog percentage from another E2 application or a
0-10VDC analog signal from an input point.
11.13.2.4 The Filter Cell
The Filter cell’s primary function is to slow the rate of
change of the PID cell’s output. The filter reads the differ
-
ence between the current output value and the value x sec-
onds ago, where x = a user-specified period of time. The
difference between these two values is multiplied by the
filter ratio, which is a percentage between 0% and 100%.
The result of this multiplication is the output value. Note
that if the filter ratio is at 100%, or if the Filter cell is dis
-
abled, the input is not modified by the Filter cell.
11.13.2.5 The Override Cell
The Override cell’s function is to provide a method of
overriding the analog output going to the Sequencer and
PWM cells to a user-specified value instead of the value
called for by the Filter cell. The Override cell can override
the output to any value between 0% and 100%, and may
be either fixed or timed. A fixed override remains overrid
-
den until the user deactivates the override, while a timed
override remains in effect until a user-specified time has
elapsed.
11.13.3 Output Cell Descriptions
The Loop/Sequence Control application has three con-
trol outputs: a standard 0-100% analog output, a set of up
to eight staged outputs, and a pulse width modulation
(PWM) output. The analog control output comes directly
from the Override cell. However, the same control output
is fed into the Sequencer and PWM cells for translation
into digital staged outputs and pulse width modulation.
11.13.3.1 The Sequencer Cell
The Sequencer cell simply activates a certain percent-
age of the Digital State 1-8 outputs based on the percent-
age of the control output. For example, if the control
output is 50%, the Sequencer cell will activate 50% of the
total number of stages. The Sequencer cell will always
round DOWN; that is, if there are four stages in a
Sequencer cell and the output is 74%, the Sequencer cell
will only activate two stages (or 50% of the stages). When
the output climbs above 75%, the third stage will activate.