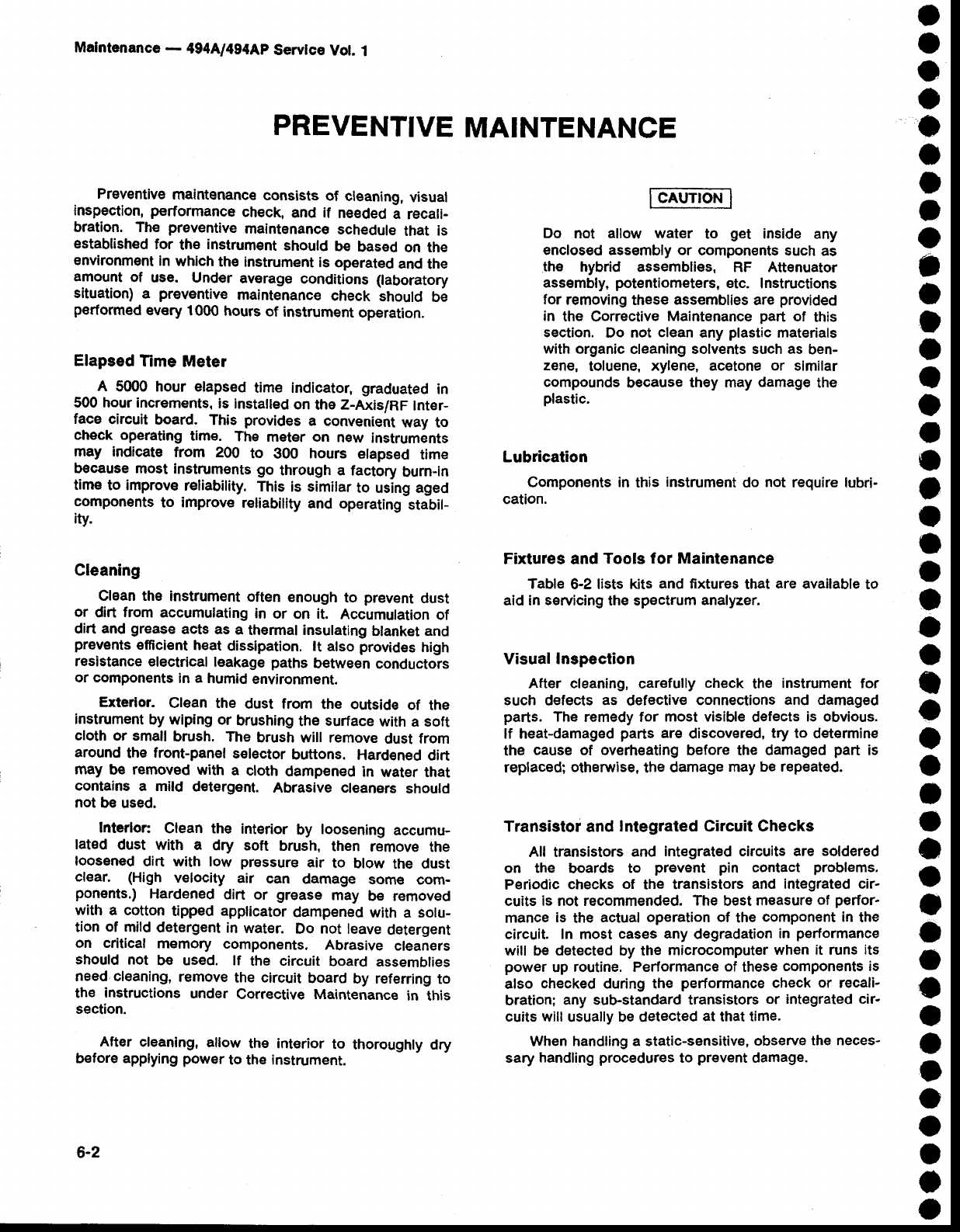
PREVENTIVE
MAINTENANCE
Preventive
maintenance
consists
of
cleaning,
visual
inspection,
performance
check,
and if
needed
a
recali-
bration. The
preventive
maintenance
schedule
that is
established
for
the
instrument
should
be
based
on the
environment
in
which
the
instrument
is operated
and
the
amount
of
use. Under
av€rage
conditions
(laboratory
situation)
a
preventive
maintenance
check
should
be
performed
every
1000
hours
of
instrument
operation.
Elapsed
Time
Meter
A
5000
hour elapsed
time indicator,
graduated
in
500 hour increments.
is
installed
on
thE Z-AxislRF
Inter-
face
circuit
board.
This
provides
a convenient
way
to
check operating
time.
The
meter on
new
instruments
may indicate
from
200
to
300
hours
elapsed
time
because most
instruments go
through a factory
burn-in
tim€
to improve
reliabitity.
This
is simitar
to using aged
components
to
improve
reliability
and operating
stabil-
ity.
Cleaning
Clean the
instrument
often
enough
to
prevent
dust
or
dirt
from
accumulating
in
or on it.
Accumulation
of
dirt and
grease
acts as
a
thermal insulating
blanket
and
prevents
efficient
heat
dissipation. lt
also
provides
high
resistance electrical
leakagg paths
between
conductors
or components
in
a
humid
environment.
Exterlor.
Clean
the
dust
from the outside
of the
Instrument
by wiping or
brushing
the
surface
with
a
soft
cloth or small
brush. The
brush will remove
dust from
around
the
front-panel
selector
buttons.
Hardened
dirt
may be rernoved with
a cloth
dampened
in
water that
contains
a mild
d€tergent.
Abrasive
cleaners
should
not be
used.
Interlon
Clean the
interior
by
loosening
accumu-
lated
dust
with a
clry
soft
brush,
then
remove
the
loosened
dirt with low
pressure
air
to
blow
the dust
cl€ar. (High
velocity
air
can
damage
som€
com-
ponents.)
Hardened
dirt
or
grease
may
be removed
with a cotton
tipped
applicator
dampened
with
a solu-
tion
of
mild
detergent
in
wat€r.
Do
not
leave
detergent
on critical
memory
components.
Abrasive
cleaners
should not
b€
used.
lf
the circuit
board
assemblies
need cleaning,
remove
the circuit
board
by referring
to
the
instructions
under
Corrective MaintenancE
in this
section.
After
cleaning,
allow
the interior
to
thoroughly dry
before applying
pow€r
to the instrument.
Maintenance
-
4g4Al4g4Ap
Servlce
Vot.
1
a
o
o
o
o
t
o
t
o
a
I
t
t
o
o
I
o
t
I
o
o
t
a
a
I
o
o
a
a
o
a
o
o
o
o
o
o
o
o
o
o
o
o
o
Do
not
allow
water
to
get
inside any
enclosed assembly or
compon€nts such
as
thE hybrid
assemblies, RF Attenuator
assembly,
pot€ntiometers,
etc.
Instructions
for
removing
these
assemblies
are
provided
in
the Corrective
Maintenance
part
of
this
section.
Do not
clean
any
plastic
materials
with organic
cleaning solvents such as
ben-
zene,
toluene,
xylene, ac€tone or similar
compounds
because
they may
damage
the
plastic.
Lubrication
Components in
this
instrument
do
not
require lubri-
cation.
Fixtures and
Tools for Maintenance
Table
6-2 lists kits
and
fixtures
that
are
available
to
aid in
servicing
the spectrum
analyzer.
Visual
Inspection
After
cleaning, carefully
check
the
instrument for
such
defects
as
defective
connections
and damaged
parts.
The
remedy for
most visible
defects
is obvious.
lf heat-damaged
parts
are
discovered,
try to
determine
the
cause
of
overheating
before the
damaged
part
is
replaced;
othenwise,
the
damage
may be
rep€ated.
Transistor
and
Integrated Circuit Checks
All transistors
and
integrated circuits are
soldered
on the
boards
to
prevent pin
contact
problems,
Periodic
checks
of
the
transistors
and integrated
cir-
cuits is not recommended.
The
best
measure
of
perfor-
mance
is
the
actual operation of
the
component in
the
circuit.
In
most
cases any
degradation
in
performance
will
be detected by the
microcomputer
when it runs its
power
up
routine. Performance
of
these
components is
also
checked
during the
performance
check or recali-
bration;
any sub-standard transistors
or integrated cir-
cuits will
usually be detected
at
that time.
When
handling a static-sensitive,
observe
the neces-
sary
handling
procedures
to
prevent
damage.
6-2